There are a lot of tuts now on most of the major smoothing and basic detailing techniques for pepakura based models. This small specific detail instructional is mostly for those still using the fiberglass/aquaresin/hotglue route but you might find some useful tidbits for folks slushcasting and sanding the basic model. Example pics are from some of my old WIP’s.
Materials List:
Bondo Spot Putty
Elmer’s White All Purpose Glue
Dry Plaster Mix
Non-corrugated Cardboard
Sharpie Permanant Marker
½ inch metal file
Ice pick (the small kind with a screwdriver handle)
Xacto knife
1. You need a model that is fiberglassed or casted to begin to use these techniques. So you’ll start with something like this.
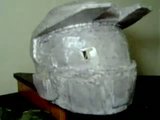
Trick 1. Smoothing a large curve. (Only on low to moderate wear pieces: no handplates, boots, cod/butt)
Believe it or not, plaster is a very effective cheap compound for this. Since the final product is basically dry gypsum, it sands extremely easily especially while still slightly damp. This lets you get the shape you want with minimal effort. However, plaster is very brittle and will crack and detach from your armor without proper reinforcement. The dried and cured plaster (an hour to several depending on thickness) soaks up liquids like a sponge. What you want is for the gypsum to plastify. To do this, apply spot putty or white glue across its surface in a thin layer that the plaster will soak up. This material will solidify within the plaster matrix and strengthen it to something akin to bondo that will adhere better to the model’s surface. Giving it a layer or two of primer also will give it some additional protection from breaking.
Used here on the top and back of the helm.
Trick 2. Squaring small platforms. (Cheeklights especially!)
A small, inflexible metal file is great for getting those sharp edges back on small platforms after sanding an area. Hold the file parallel to the platform and make 4-5 passes for each width of the file. This also works for getting rid of the occasional resin drop marring your perfect surface.
Used here on the cheeklights and lower visor platform.
Trick 3. Recessed line details. (all pieces)
As I’ve seen on many HD builds, people will use various means to mark where they will cut detail lines and recessed details. The rule to remember is the old “measure twice, cut once”. Use a Sharpie (blue or black preferred) to mark where you think your lines should go. This serves a dual purpose, to give you an idea of the symmetry and accuracy of your lines and also a guide while you are cutting them. The marker tip will usually clog with dust or paint after awhile so be sure to have a spare or two. Cut the lines with a dremel cutting wheel (reinforced or EZ-LOCK) at approximately ¼ inch depth. At sharp corners, use some overlap to make sure you have all lines cut at a uniform depth. The bigger the wheel you use, the straighter your lines will be but the further your overlap at corners will be. Cover the overlapped lines with spot putty. Then use an ice pick to assure uniformity of dimension for your lines. Don’t be afraid to fill your lines with spot putty, smooth it out and do it again if it doesn’t look right to you. Use the same principle to cut the holes for recessed pieces when required. For most recessed details, you are better off using a small cardboard template that you can pour mud around in the regular smoothing process. Remove it later and clean the resulting recess with an Xacto knife.
Used here on the back of the helm.
Trick 4. Adding small positive relief details. (All pieces)
4.1 Cardboard.
The best kind to use for this is the type that has printed ink on one side (most battery packages, cereal boxes, soda/beer case boxes, etc.). First cut a piece in the shape you want, ink printed side out. In the case that you have multiple or symmetrical pieces, use the first as a template to cut more pieces of the same size always with the printed side out. Use a small amount of Elmer’s glue on the non-printed side to wet the cardboard and make it flexible. It usually takes a good 30 seconds to rub it in to the point where the card is soaked. Now it will conform to any curve and stick permanently to your desired surface. Align it correctly and let it set and completely dry. The glue will make the card impermiable and after a coat of primer, it will be set to paint. It is critical that you keep all glue off the printed side. The surface you have when you primer it is the final one. Sanding will not help you.
Used here on the side vents of the helm.
4.2 Odds ‘n Ends
Many times the best detail bits are already laying around your house in the form of small screws and bolts, old wires and phone chords, bits of pipe, caps of old bottles etc. Look around and find what works for you. One of my favorite little pieces is pink pearl erasers. You can cut them easily, sand them easily, and they take paint well.
Hope this helps a few folks.
Comments and crits welcome.
Materials List:
Bondo Spot Putty
Elmer’s White All Purpose Glue
Dry Plaster Mix
Non-corrugated Cardboard
Sharpie Permanant Marker
½ inch metal file
Ice pick (the small kind with a screwdriver handle)
Xacto knife
1. You need a model that is fiberglassed or casted to begin to use these techniques. So you’ll start with something like this.
Trick 1. Smoothing a large curve. (Only on low to moderate wear pieces: no handplates, boots, cod/butt)
Believe it or not, plaster is a very effective cheap compound for this. Since the final product is basically dry gypsum, it sands extremely easily especially while still slightly damp. This lets you get the shape you want with minimal effort. However, plaster is very brittle and will crack and detach from your armor without proper reinforcement. The dried and cured plaster (an hour to several depending on thickness) soaks up liquids like a sponge. What you want is for the gypsum to plastify. To do this, apply spot putty or white glue across its surface in a thin layer that the plaster will soak up. This material will solidify within the plaster matrix and strengthen it to something akin to bondo that will adhere better to the model’s surface. Giving it a layer or two of primer also will give it some additional protection from breaking.
Used here on the top and back of the helm.
Trick 2. Squaring small platforms. (Cheeklights especially!)
A small, inflexible metal file is great for getting those sharp edges back on small platforms after sanding an area. Hold the file parallel to the platform and make 4-5 passes for each width of the file. This also works for getting rid of the occasional resin drop marring your perfect surface.
Used here on the cheeklights and lower visor platform.
Trick 3. Recessed line details. (all pieces)
As I’ve seen on many HD builds, people will use various means to mark where they will cut detail lines and recessed details. The rule to remember is the old “measure twice, cut once”. Use a Sharpie (blue or black preferred) to mark where you think your lines should go. This serves a dual purpose, to give you an idea of the symmetry and accuracy of your lines and also a guide while you are cutting them. The marker tip will usually clog with dust or paint after awhile so be sure to have a spare or two. Cut the lines with a dremel cutting wheel (reinforced or EZ-LOCK) at approximately ¼ inch depth. At sharp corners, use some overlap to make sure you have all lines cut at a uniform depth. The bigger the wheel you use, the straighter your lines will be but the further your overlap at corners will be. Cover the overlapped lines with spot putty. Then use an ice pick to assure uniformity of dimension for your lines. Don’t be afraid to fill your lines with spot putty, smooth it out and do it again if it doesn’t look right to you. Use the same principle to cut the holes for recessed pieces when required. For most recessed details, you are better off using a small cardboard template that you can pour mud around in the regular smoothing process. Remove it later and clean the resulting recess with an Xacto knife.
Used here on the back of the helm.
Trick 4. Adding small positive relief details. (All pieces)
4.1 Cardboard.
The best kind to use for this is the type that has printed ink on one side (most battery packages, cereal boxes, soda/beer case boxes, etc.). First cut a piece in the shape you want, ink printed side out. In the case that you have multiple or symmetrical pieces, use the first as a template to cut more pieces of the same size always with the printed side out. Use a small amount of Elmer’s glue on the non-printed side to wet the cardboard and make it flexible. It usually takes a good 30 seconds to rub it in to the point where the card is soaked. Now it will conform to any curve and stick permanently to your desired surface. Align it correctly and let it set and completely dry. The glue will make the card impermiable and after a coat of primer, it will be set to paint. It is critical that you keep all glue off the printed side. The surface you have when you primer it is the final one. Sanding will not help you.
Used here on the side vents of the helm.
4.2 Odds ‘n Ends
Many times the best detail bits are already laying around your house in the form of small screws and bolts, old wires and phone chords, bits of pipe, caps of old bottles etc. Look around and find what works for you. One of my favorite little pieces is pink pearl erasers. You can cut them easily, sand them easily, and they take paint well.
Hope this helps a few folks.
Comments and crits welcome.