Please note: Construction finished... the continuation of the build is further down this page and on the next. Please enjoy, and feel free to comment or ask questions 
Okay, so I have an individual that requested some help with the Reach foam files they found in the 405th 4Shared database in Foam Templates/Reach/Base/Male/Forearm. They are new to working with foam, so when they told me they were confused with the layout of the individual parts, I told them I would take a look-see. After looking at the files, I realized the issues he was experiencing could stump just about any beginner, and maybe even some with a bit more experience than that. I am not saying they are bad files... because they are not. They simply need a bit of explanation to help users along.
With that, let's begin.
FIRST AND FOREMOST, due credit must be given. Model by Ruze789 and Foam Unfold by L3x Blu3r1v3r
Tools required:
EVA foam - These parts utilize approx. 3/4 of a 2'X2' sheet of EVA Foam for both left and right forearms
*Scalpel handle with #11 blades (I used just one blade and sharpened it between each piece at a minimum)
Ball point pen
Printed templates (X2) I used the default size of H:200mm W:101mm D:114mm
*Box Cutter blade - I use the small, rectangle, single edge ones (the kind you put in a cheap box-cutter)
*Cutting mat (or other surface to protect your table or whatever is under your foam!)
Hot glue gun
*High temp glue sticks (I ONLY use hot temp and not low or multi-temp ones... they make a difference!)
Heat gun
*Dremel with barrel sander bit (120 grit)
* indicates optional or personal preference. I have found that using these items generally yield superior builds if used correctly.
So, now that we have covered the tools, let's look at the file. Note: I am only focusing on the 2D portion for now and just a reminder, this is the Left only:
The numbers being all jumbled up will become apparent in the photo after this one.
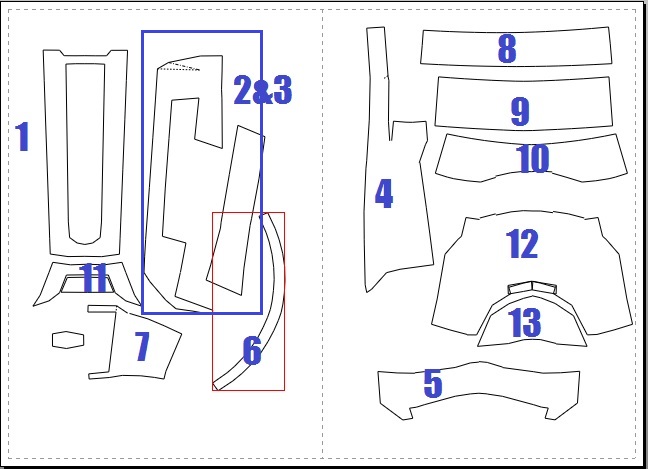
And now my cut-outs:
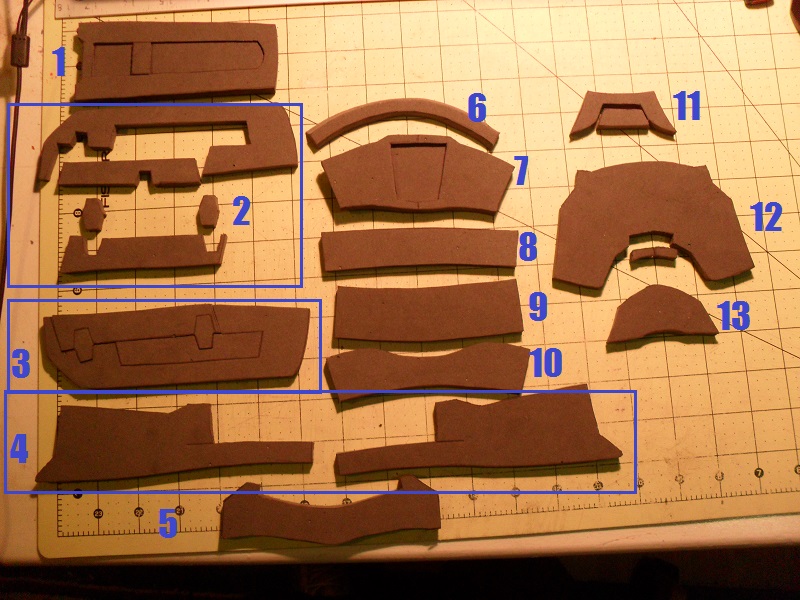
Now, to explain how I came up with these cuts, and special instructions for each one if needed.
1. This part is pretty self explanatory. Cut the outside line, then the inside one. TIP: When cutting the inside, hold your blade perpendicular to the foam when you approach a corner or curve and lightly use a sawing motion so you get a clean 90 degree cut
2 & 3. This is where you will need the 2nd copy. Cut out the smaller rectangle from one copy, and transfer it to the other. Align it so that it completes the gap in the larger part. Also, this is where you will position the oblong hex pieces to bridge between multiple parts (PLEASE NOTE, WHERE I PLACED MINE IS NOT GAME ACCURATE! ADJUST ACCORDINGLY!). As you can see in my foam cut-outs, #2 is an exploded view, whereas #3 is it all assembled. Notice how cutting it out of a single piece creates perfect seams. Try to do this whenever possible. So, you notice that there are two in foam, but only one is the template. This was done to save space I believe. You will need to use your cutout twice, flipping it upside down to create the second piece.
4. This is another piece that gets flipped to create the mirror piece. Where the "V" is, I simply eliminated that gap and just cut the line (you can see the cut and ink line where the "V" would have been. I did this for two reasons. 1. Foam is forgiving. Cutting unnecessary "V"s will result in noticeable seams. 2. If it does become necessary to cut the "V" in due to the piece not forming properly, I can always cut it in later... but it is really difficult to go the other way around
5. Simple cut
6. This one is a bit more difficult and is where I used my box cutting blade. Also, a bit of pre-planning is required. The outside curve and the sides are cut normal... BUT the inside curve has an approx. 60 degree OUTWARD angle cut into it. I stress the outward bit because you have to plan this on your EVA mat when transferring the template to allow for the extra EVA that angle will require. Be sure not to butt another piece too close to it in attempts to save EVA. I have found using a box cutter blade gives excellent control of the angle while maintaining a very clean cut.
7. This is another tricky one to transfer to the EVA from the template. If you look at the template piece, then my cut out piece, it becomes pretty clear what I had to do. Note: The bisecting line on the outside piece is just a drawn line, not a cut. This was necessary to keep alignment on the template piece when it is flipped over to trace the opposite side.
8, 9, & 10. Simply trace and cut
11. This one was cut out of a single piece. I did not put the gap you see in the template, I simply eliminated it. Once again, this makes the two pieces join perfectly.
12. Just like the previous one, this too was cut from one piece by eliminating the gap. The only difference is I took the small piece and rotated it 90 degrees (so now it was lying on its long edge with finished surface of the EVA facing the larger piece. I then cut a small "V" in the back without fully cutting the piece in two.
13. Yay!! A simple cut for the final one
(Even though it looks like it could be coupled with #12, it varies in shape a bit too drastic for my liking.
Now, do it all over again for the other arm!
Since it is 4:30am here, I will continue (and most likely finish) the construction phase of this part "tomorrow"
I hope this tutorial helps those that may be in the same predicament as my friend, and if I get good feedback, I will continue to do more parts. (I need something to do since all my main projects are on hold due to lack of parts, supplies, and cash! Luckily, I make sure I ALWAYS have EVA on hand for times like these!)
Okay, so I have an individual that requested some help with the Reach foam files they found in the 405th 4Shared database in Foam Templates/Reach/Base/Male/Forearm. They are new to working with foam, so when they told me they were confused with the layout of the individual parts, I told them I would take a look-see. After looking at the files, I realized the issues he was experiencing could stump just about any beginner, and maybe even some with a bit more experience than that. I am not saying they are bad files... because they are not. They simply need a bit of explanation to help users along.
With that, let's begin.
FIRST AND FOREMOST, due credit must be given. Model by Ruze789 and Foam Unfold by L3x Blu3r1v3r
Tools required:
EVA foam - These parts utilize approx. 3/4 of a 2'X2' sheet of EVA Foam for both left and right forearms
*Scalpel handle with #11 blades (I used just one blade and sharpened it between each piece at a minimum)
Ball point pen
Printed templates (X2) I used the default size of H:200mm W:101mm D:114mm
*Box Cutter blade - I use the small, rectangle, single edge ones (the kind you put in a cheap box-cutter)
*Cutting mat (or other surface to protect your table or whatever is under your foam!)
Hot glue gun
*High temp glue sticks (I ONLY use hot temp and not low or multi-temp ones... they make a difference!)
Heat gun
*Dremel with barrel sander bit (120 grit)
* indicates optional or personal preference. I have found that using these items generally yield superior builds if used correctly.
So, now that we have covered the tools, let's look at the file. Note: I am only focusing on the 2D portion for now and just a reminder, this is the Left only:
The numbers being all jumbled up will become apparent in the photo after this one.
And now my cut-outs:
Now, to explain how I came up with these cuts, and special instructions for each one if needed.
1. This part is pretty self explanatory. Cut the outside line, then the inside one. TIP: When cutting the inside, hold your blade perpendicular to the foam when you approach a corner or curve and lightly use a sawing motion so you get a clean 90 degree cut
2 & 3. This is where you will need the 2nd copy. Cut out the smaller rectangle from one copy, and transfer it to the other. Align it so that it completes the gap in the larger part. Also, this is where you will position the oblong hex pieces to bridge between multiple parts (PLEASE NOTE, WHERE I PLACED MINE IS NOT GAME ACCURATE! ADJUST ACCORDINGLY!). As you can see in my foam cut-outs, #2 is an exploded view, whereas #3 is it all assembled. Notice how cutting it out of a single piece creates perfect seams. Try to do this whenever possible. So, you notice that there are two in foam, but only one is the template. This was done to save space I believe. You will need to use your cutout twice, flipping it upside down to create the second piece.
4. This is another piece that gets flipped to create the mirror piece. Where the "V" is, I simply eliminated that gap and just cut the line (you can see the cut and ink line where the "V" would have been. I did this for two reasons. 1. Foam is forgiving. Cutting unnecessary "V"s will result in noticeable seams. 2. If it does become necessary to cut the "V" in due to the piece not forming properly, I can always cut it in later... but it is really difficult to go the other way around
5. Simple cut
6. This one is a bit more difficult and is where I used my box cutting blade. Also, a bit of pre-planning is required. The outside curve and the sides are cut normal... BUT the inside curve has an approx. 60 degree OUTWARD angle cut into it. I stress the outward bit because you have to plan this on your EVA mat when transferring the template to allow for the extra EVA that angle will require. Be sure not to butt another piece too close to it in attempts to save EVA. I have found using a box cutter blade gives excellent control of the angle while maintaining a very clean cut.
7. This is another tricky one to transfer to the EVA from the template. If you look at the template piece, then my cut out piece, it becomes pretty clear what I had to do. Note: The bisecting line on the outside piece is just a drawn line, not a cut. This was necessary to keep alignment on the template piece when it is flipped over to trace the opposite side.
8, 9, & 10. Simply trace and cut
11. This one was cut out of a single piece. I did not put the gap you see in the template, I simply eliminated it. Once again, this makes the two pieces join perfectly.
12. Just like the previous one, this too was cut from one piece by eliminating the gap. The only difference is I took the small piece and rotated it 90 degrees (so now it was lying on its long edge with finished surface of the EVA facing the larger piece. I then cut a small "V" in the back without fully cutting the piece in two.
13. Yay!! A simple cut for the final one
Now, do it all over again for the other arm!
Since it is 4:30am here, I will continue (and most likely finish) the construction phase of this part "tomorrow"
I hope this tutorial helps those that may be in the same predicament as my friend, and if I get good feedback, I will continue to do more parts. (I need something to do since all my main projects are on hold due to lack of parts, supplies, and cash! Luckily, I make sure I ALWAYS have EVA on hand for times like these!)