After looking for foam templates that were accurate and easy to interpret for the Halo 4 Master Chief shoulder armor, I finally gave up searching and decided to make my own. After a first attempt that failed, I came up with this, Ver. 2.0 
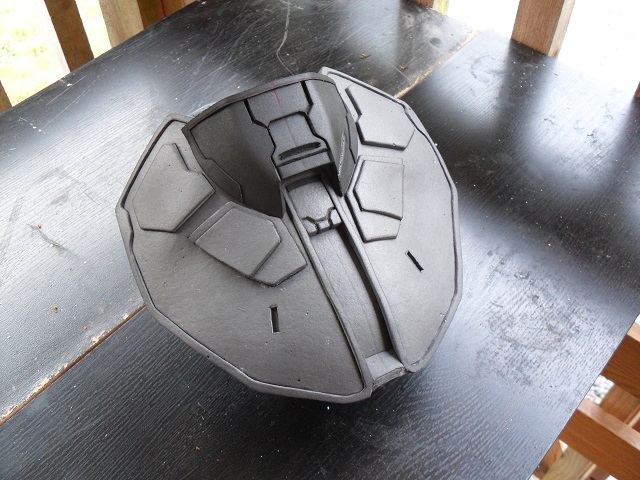
First off (I can't help it), due credit must be given: Template by EVAkura
(this template is redistributable, but please give credit) Be sure it prints to only one page, with no borders. NOTE: At this time, this links to a .jpg that may not print to scale. I tested it with the same file provided, making sure the margins were off, it was not scaled to fit the page (print actual size), in landscape format, and it came out perfect. NEW UPDATE: I have replaced the original hand-drawn file with one that I remade digitally. It is scaled MUCH larger now. Just be sure your print settings are set to 300dpi.
Tools required:
EVA foam - These parts utilize approx. 1/2 of a 2'X2' sheet of EVA Foam for both left and right shoulders. Note: I used 3/8" thick EVA
Craft foam - 1/4" (6mm) Craft foam is used for the topmost piece. 1/2 of a standard sheet is more than enough.
Scalpel handle with #11 blades (I used just one blade and sharpened it between each piece at a minimum) MUST HAVE SHARP BLADE FOR OPTIMAL ACCURACY.
Ball point pen
Printed template. The default constructed size is H:190mm W:210mm D:75mm. This template only requires 1 page!
*Cutting mat (or other surface to protect your table or whatever is under your foam!)
Super Glue (This build will NOT be using ANY hot glue. I strongly advise not attempting this build with it)
Heat gun
Dremel with barrel sander bit (120 grit)
Now for the build. After printing the template, take the main portion (largest piece), and cut out around the outside, as well as the parts you see in the photo below. Lay it down onto your EVA and trace that half, then flip over, align the center line, and trace the mirrored side. It is very important that you make sure your pen marks are VERY VISIBLE! I will explain why in a bit. DO NOT CUT THE EVA AT THIS POINT.
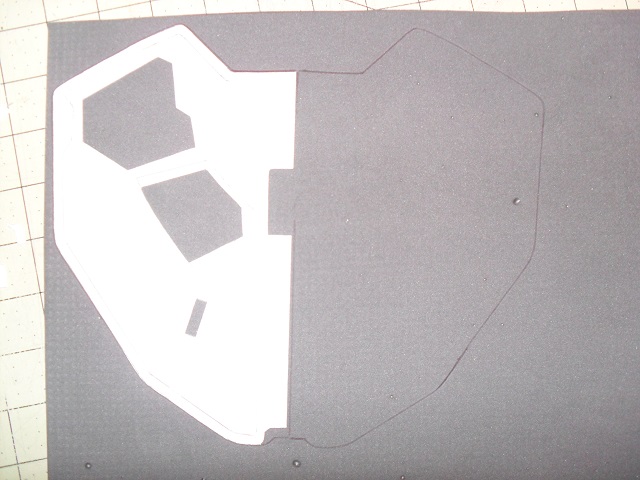
Then, continue on to the next few parts of the template (using the photo below for reference). Make sure that all of your previous lines align with the template and trace out the new cut-outs. DO NOT CUT THE EVA AT THIS POINT.
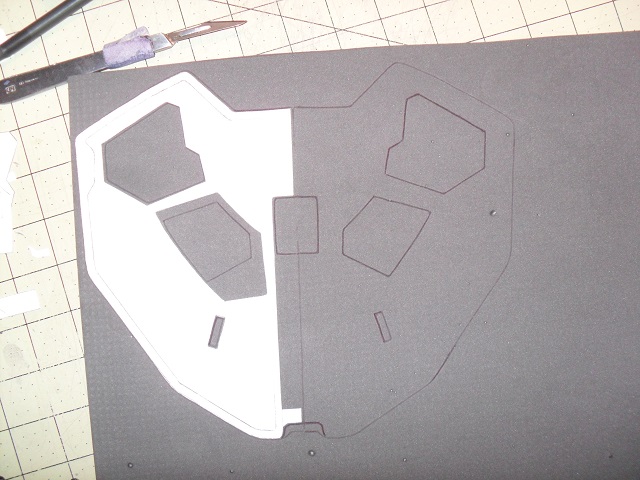
Now for the last cut-outs. After you have done this step, ONLY cut the outermost outline of the EVA.
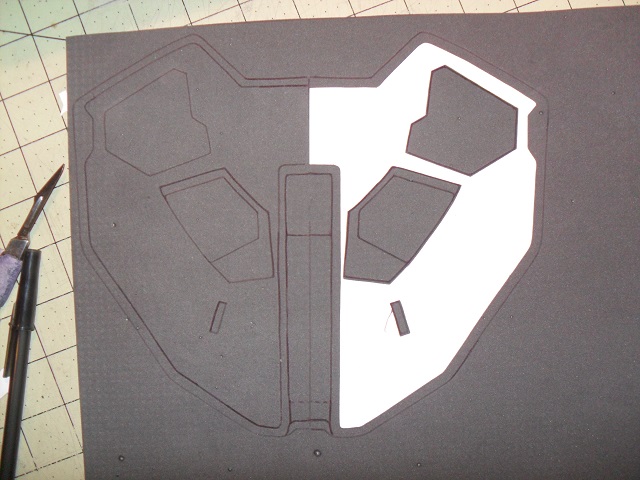
The next step is to heat form this part. The reason why I stressed making sure your pen outlines are so visible is because heat forming tends to fade out the ink quite a bit, and you certainly will need to be able to see them after heat forming! It is best to have a few good reference photos to compare the shape that you need to replicate, but I will give a few pointers just the same. Other than the obvious curve, the shoulder has a compound curve that makes the front dip down, as well as the sides. This gives us the perfect opportunity to exploit the properties of EVA.
Heat the part to temperature (if you are not experienced with heat forming, practice on some scrap to get the hang of it beforehand) and start with the outside bends. Then, following the photo below, hold the EVA with one hand and with the other (the one with the arrow) push your fingers down and pull in the direction of the arrow (away, not up). Be sure not to stretch the EVA, but you will need to stress it to the point just before that. This will concave the EVA to give the compound angles needed.
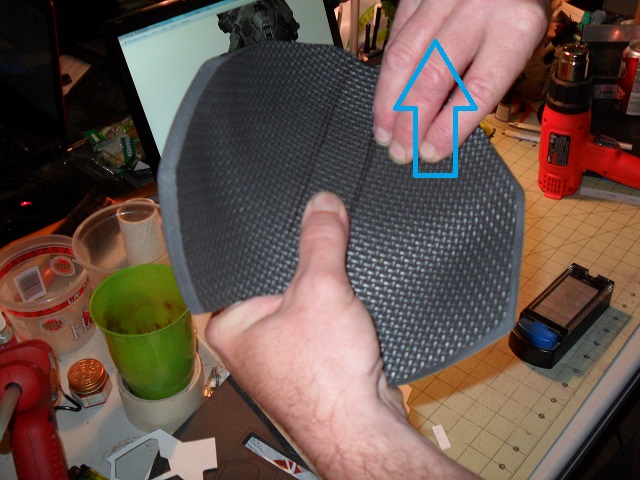
Then, flip it over (right side up meow), and using photo below as reference, heat form the EVA for this bend. Where the line is, is where you want the majority of the bend to be.
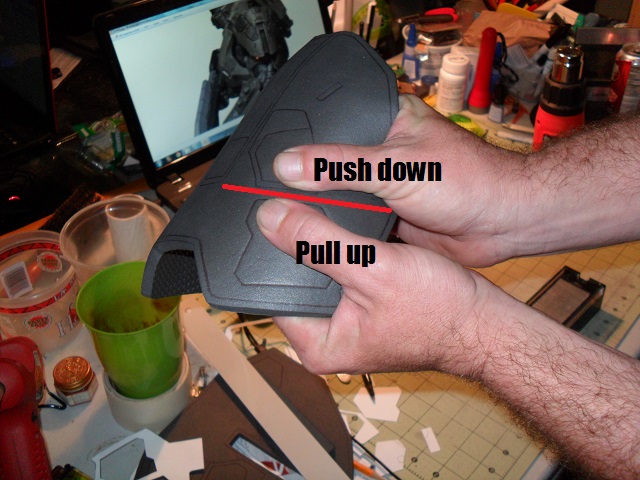
At this point, your piece should look similar to this:
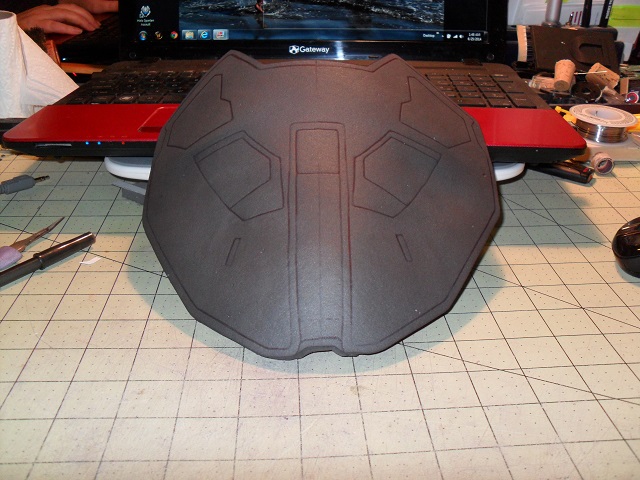
Now it is time to cut out the "plates" and the two recessed rectangles. The rectangle pieces are pretty straightforward. With the plates, I carefully cut them out by suspending the piece in one hand and cutting with the other. I recommend not cutting this on a hard or flat surface to avoid loosing its shape. Obviously, be careful of the blade. Once they are cut out, use the barrel (just the rubber barrel) bit in your dremel to "sand" the top edges of the plates. The friction created will round them a bit without taking away any material if done lightly. Then, glue in place, making sure that they are stepped above the surface of the main armor by about 1/8". When supergluing, glue one side at a time. Always apply glue to the piece that is lowest in profile. In this case, that would be the main armor, not the plates. This will help keep any glue from being visually exposed. It will take a bit of bending to get the other sides glued after the first one is done, but if done carefully, it works quite well, and becomes easier over time. Once finished, they should look similar to this:
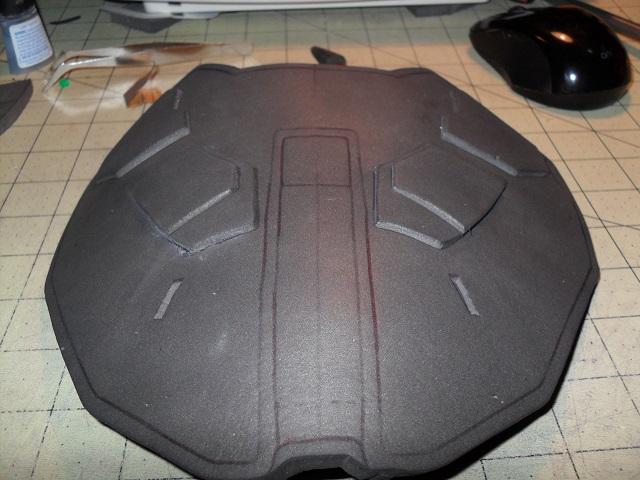
Now, cut out the center piece shown below. The left arrow shows the front that needs a 45 degree angle cut. The middle shows the detail line on the top, and a slit cut in the bottom. The piece will bend here when reassembled. The arrow on the right shows that piece is cut completely off, then re-glued a step higher. Detail lines are then added.
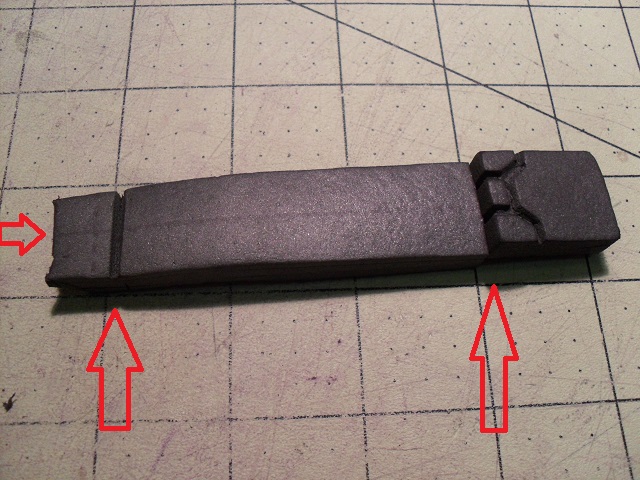
Cut a small piece of foam about 1/8" thick and glue it to the end of this piece here:
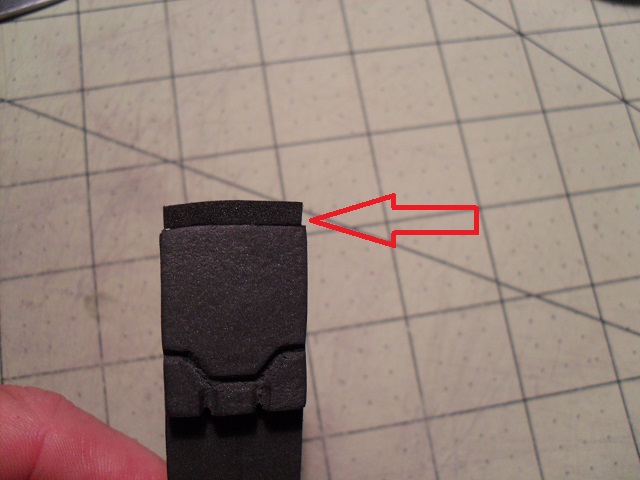
This piece makes up the distance lost when the piece is angled down in the reassembly process. Also, it is not on the template.
Glue this piece back in place, but recess it about 1/4". This part, you will want to double-check with reference pictures, or my final image for further understanding if unclear.
Now it is time to cut out the outside edge.
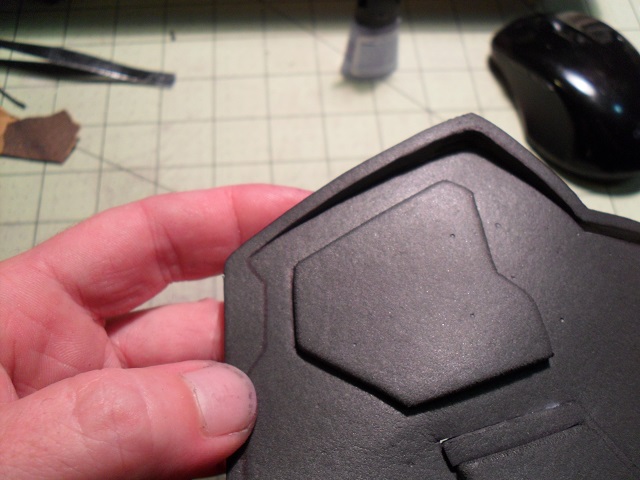
Once finished, it should look like this:
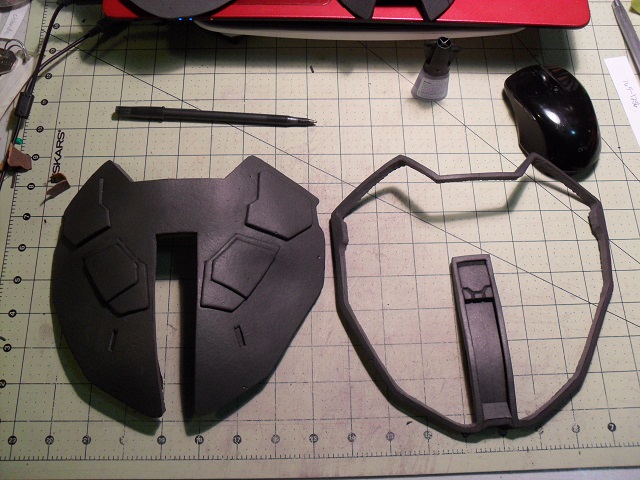
Continuing on the next post due to image quantity restrictions.
First off (I can't help it), due credit must be given: Template by EVAkura
Tools required:
EVA foam - These parts utilize approx. 1/2 of a 2'X2' sheet of EVA Foam for both left and right shoulders. Note: I used 3/8" thick EVA
Craft foam - 1/4" (6mm) Craft foam is used for the topmost piece. 1/2 of a standard sheet is more than enough.
Scalpel handle with #11 blades (I used just one blade and sharpened it between each piece at a minimum) MUST HAVE SHARP BLADE FOR OPTIMAL ACCURACY.
Ball point pen
Printed template. The default constructed size is H:190mm W:210mm D:75mm. This template only requires 1 page!
*Cutting mat (or other surface to protect your table or whatever is under your foam!)
Super Glue (This build will NOT be using ANY hot glue. I strongly advise not attempting this build with it)
Heat gun
Dremel with barrel sander bit (120 grit)
Now for the build. After printing the template, take the main portion (largest piece), and cut out around the outside, as well as the parts you see in the photo below. Lay it down onto your EVA and trace that half, then flip over, align the center line, and trace the mirrored side. It is very important that you make sure your pen marks are VERY VISIBLE! I will explain why in a bit. DO NOT CUT THE EVA AT THIS POINT.
Then, continue on to the next few parts of the template (using the photo below for reference). Make sure that all of your previous lines align with the template and trace out the new cut-outs. DO NOT CUT THE EVA AT THIS POINT.
Now for the last cut-outs. After you have done this step, ONLY cut the outermost outline of the EVA.
The next step is to heat form this part. The reason why I stressed making sure your pen outlines are so visible is because heat forming tends to fade out the ink quite a bit, and you certainly will need to be able to see them after heat forming! It is best to have a few good reference photos to compare the shape that you need to replicate, but I will give a few pointers just the same. Other than the obvious curve, the shoulder has a compound curve that makes the front dip down, as well as the sides. This gives us the perfect opportunity to exploit the properties of EVA.
Heat the part to temperature (if you are not experienced with heat forming, practice on some scrap to get the hang of it beforehand) and start with the outside bends. Then, following the photo below, hold the EVA with one hand and with the other (the one with the arrow) push your fingers down and pull in the direction of the arrow (away, not up). Be sure not to stretch the EVA, but you will need to stress it to the point just before that. This will concave the EVA to give the compound angles needed.
Then, flip it over (right side up meow), and using photo below as reference, heat form the EVA for this bend. Where the line is, is where you want the majority of the bend to be.
At this point, your piece should look similar to this:
Now it is time to cut out the "plates" and the two recessed rectangles. The rectangle pieces are pretty straightforward. With the plates, I carefully cut them out by suspending the piece in one hand and cutting with the other. I recommend not cutting this on a hard or flat surface to avoid loosing its shape. Obviously, be careful of the blade. Once they are cut out, use the barrel (just the rubber barrel) bit in your dremel to "sand" the top edges of the plates. The friction created will round them a bit without taking away any material if done lightly. Then, glue in place, making sure that they are stepped above the surface of the main armor by about 1/8". When supergluing, glue one side at a time. Always apply glue to the piece that is lowest in profile. In this case, that would be the main armor, not the plates. This will help keep any glue from being visually exposed. It will take a bit of bending to get the other sides glued after the first one is done, but if done carefully, it works quite well, and becomes easier over time. Once finished, they should look similar to this:
Now, cut out the center piece shown below. The left arrow shows the front that needs a 45 degree angle cut. The middle shows the detail line on the top, and a slit cut in the bottom. The piece will bend here when reassembled. The arrow on the right shows that piece is cut completely off, then re-glued a step higher. Detail lines are then added.
Cut a small piece of foam about 1/8" thick and glue it to the end of this piece here:
This piece makes up the distance lost when the piece is angled down in the reassembly process. Also, it is not on the template.
Glue this piece back in place, but recess it about 1/4". This part, you will want to double-check with reference pictures, or my final image for further understanding if unclear.
Now it is time to cut out the outside edge.
Once finished, it should look like this:
Continuing on the next post due to image quantity restrictions.