I'd like to get some feedback on internal supports for larger 3D printed prop. I've resumed getting a Halo 3 Fuel Rod Cannon ready for printing and while I have a good plan for the body of it, the forward arches are becoming an issue.
The hand guard and arch are only connected to the body by the handle and the connection on the top right just behind where the ammunition is loaded. Seeing as this is a shoulder mounted launcher most of its mass should be supported while on the shoulder. My worry are the highlighted bits, the arch itself will be under 2cm wide at its thinnest with some additional bulk on the backside where I plan to add support pegs.
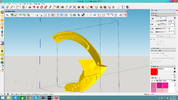
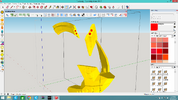
The pegs will be about 12mm in diameter and around 25-30mm long depending on the part. This method of pegged supports and super glue has worked well on my carbine but this build will be much more intricate.
Ideally I don't want too much of a load on this area and would prefer to beef up internal supports from the handle to the rest of the prop. I'd also like to keep everything 3D printed to avoid a run to the hardware store for PVC or something similar so I'm open to ideas and feedback on how to best keep this monster from snapping.
The hand guard and arch are only connected to the body by the handle and the connection on the top right just behind where the ammunition is loaded. Seeing as this is a shoulder mounted launcher most of its mass should be supported while on the shoulder. My worry are the highlighted bits, the arch itself will be under 2cm wide at its thinnest with some additional bulk on the backside where I plan to add support pegs.
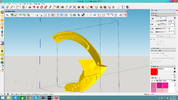
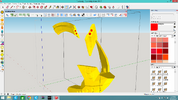
The pegs will be about 12mm in diameter and around 25-30mm long depending on the part. This method of pegged supports and super glue has worked well on my carbine but this build will be much more intricate.
Ideally I don't want too much of a load on this area and would prefer to beef up internal supports from the handle to the rest of the prop. I'd also like to keep everything 3D printed to avoid a run to the hardware store for PVC or something similar so I'm open to ideas and feedback on how to best keep this monster from snapping.