This is a rewrite of my original build log on Roosterteeth.com, which is available here: http://roosterteeth.com/members/journal/entry.php?id=3341059
Due to the 405th.com limit of 25 images per post, this will be posted in multiple parts, as I migrate all the pictures across.
-----------------------------------------------------------------------------------------------------------------------------------------------------------------------------
This project is a follow-up to the Halo 4 Spartan armour I made a few months back from EVA foam, to make Felix from Red vs Blue Seasons 11 and 12. I made it in two months, for PAX AUS '14.
To match the armour, I made a Halo 4 DMR to match, also in EVA foam. A little small, but light and only took a day. I made it back-mounted, with high-strength magnets, which turned out to be a hit at PAX, especially with the other Spartans!
To prepare for CanCon here in Canberra on Jan 25/26, I made a Halo 4 Sniper Rifle as another weapon to match the character.
The whole project took just over a week, start to finish. I'll explain my process and show my progress here, to demonstrate how I did it.
GOALS
I started with a few goals in mind:
- the barrel had to be removable for transport
- the without-barrel length had to be under a meter
- the whole thing had to be durable enough to take to a con
These extra goals were a nicety, if things worked out ok:
- as far as possible, it had to be made from EVA Foam
- it had to have a sliding bolt-action
- the magazine had to be removable
- the scope had to be able to be looked through
Initial research was on what the rifle looked like, in comparison with the Halo 1/2/3/Reach versions, and starting to think about layers.
INSPIRATION
During research, I found this guy, who made a H4 Sniper from MDF / wood - and it was badass:
props.punishedpixels.com/2013/05/24/halo-4-sniper-rifl...
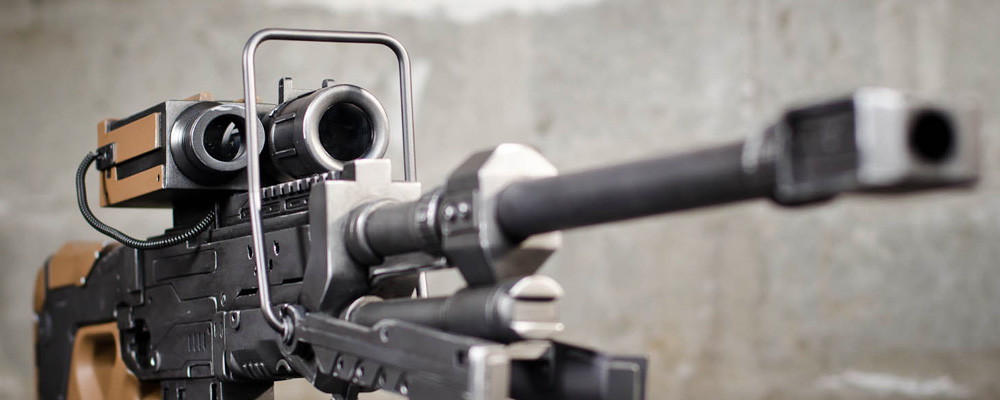
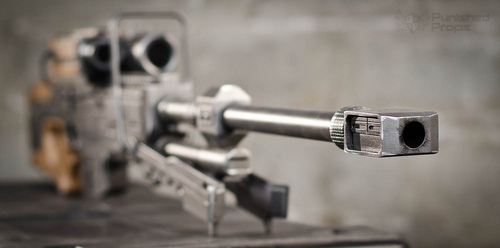
Layering of the MDF wood:
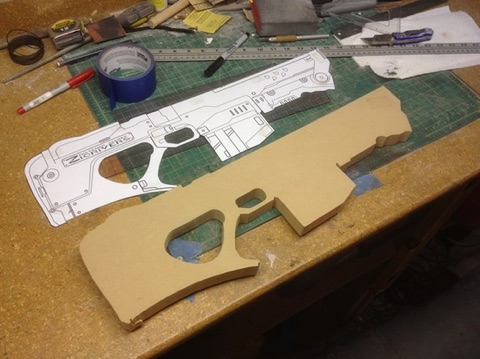
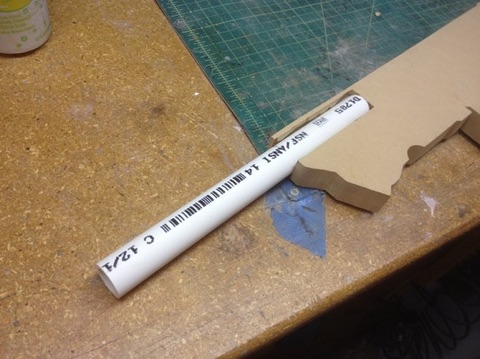
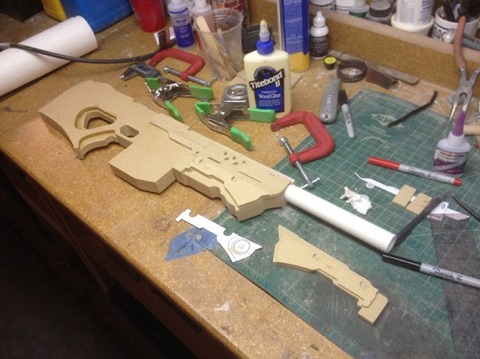
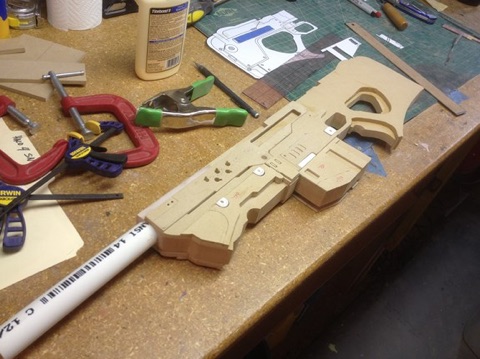
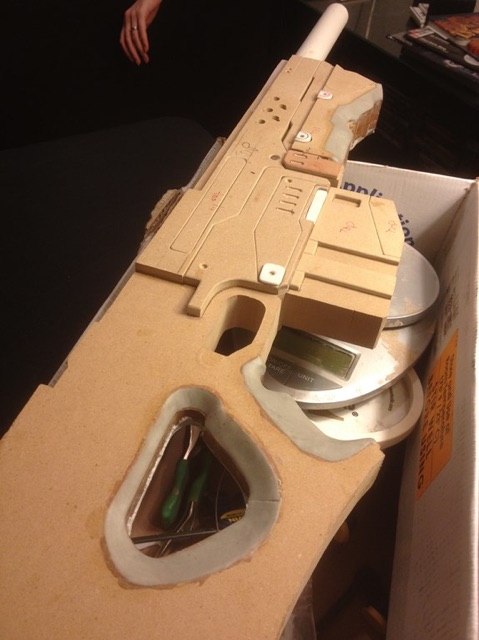
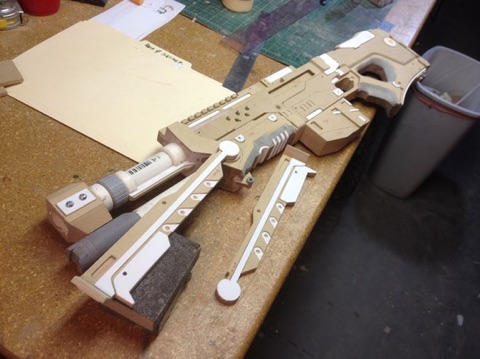
If I could be even half as good as this guy, I would be able to make an AWESOME prop. This guide became my reference for two things: what layers to do (as MDF layers similar to foam), and how the in-game look could translate to real life.
BLUEPRINTING
As with the DMR, I needed a blueprint image to reference the rifle from - I sourced a blueprint image off Google, that I could use as a template. I had to do some in-depth research, as there were many mis-labelled blueprints - many people had images of the Halo Reach sniper rifle (arguably better looking) listed as the Hal 4 variant, so I had to get the reference image straight from the Wiki, and compare it to every blueprint I could find. Eventually I settled on this image:
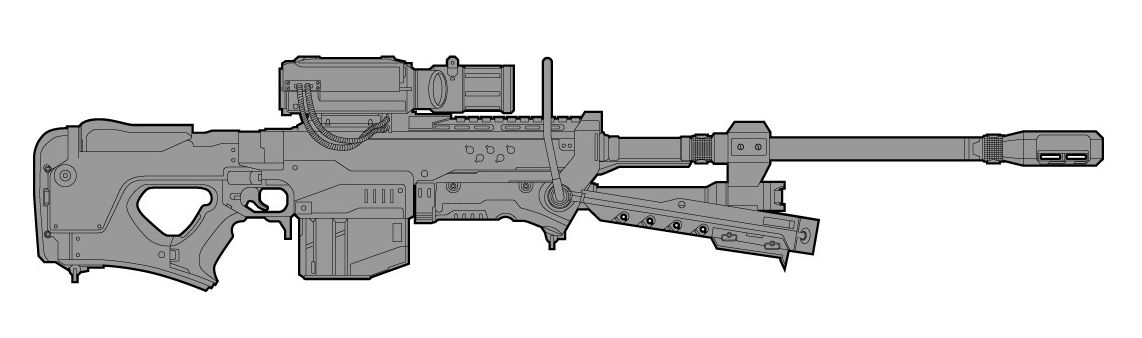
This image was the only one I found that was: black and white, a large size, the correct version and freely available (not watermarked).
I also used a few other images for reference:
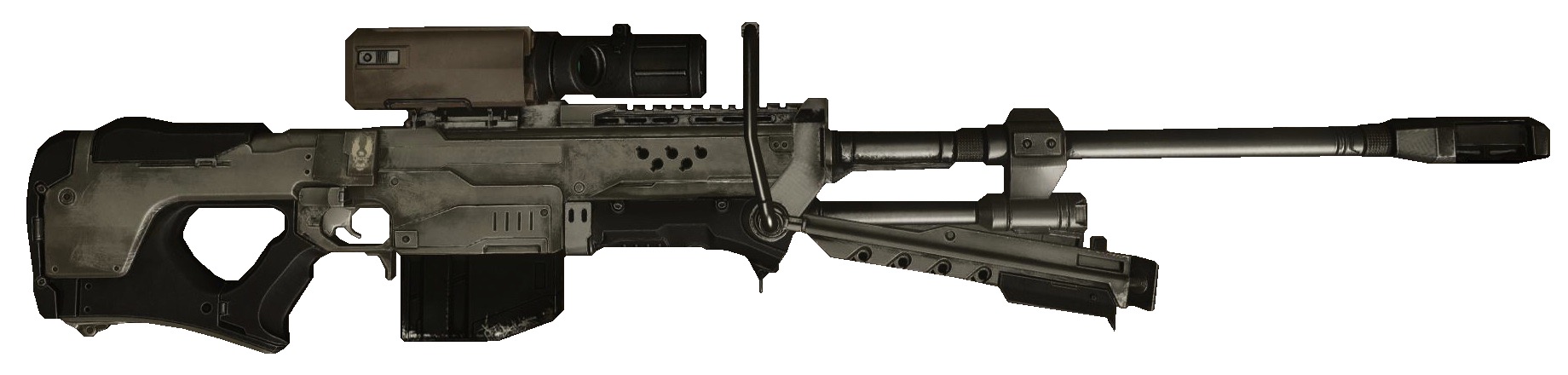
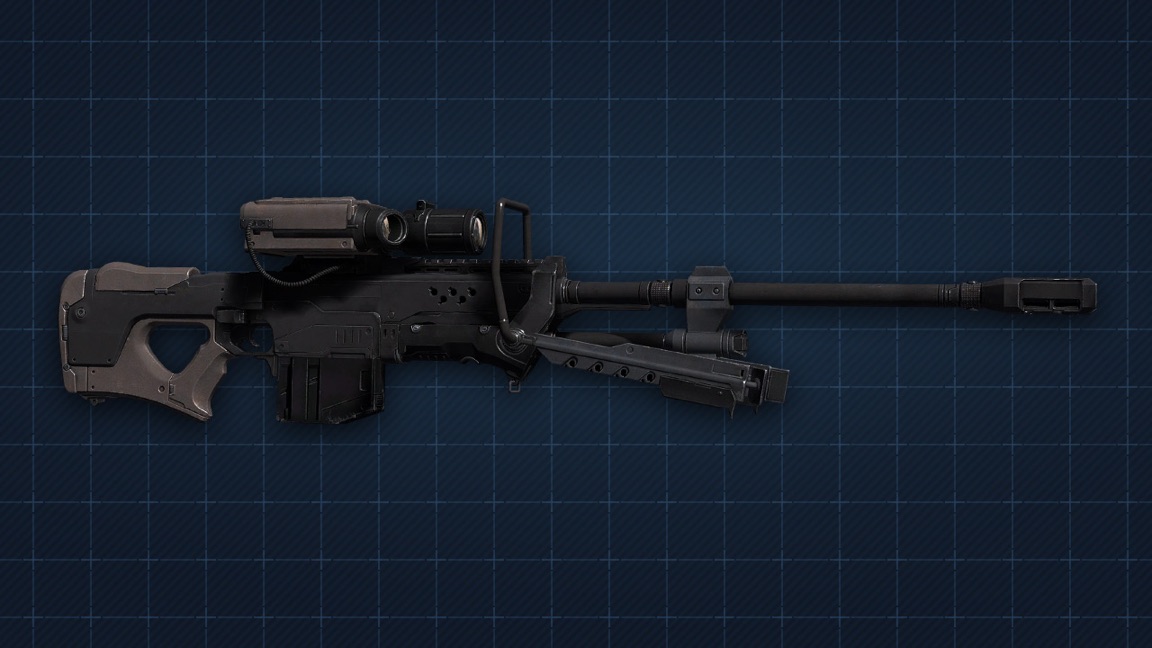
I started by loading the rifle into GIMP, to cut into equal segments. This cutting is to print onto A4 paper.
The size of the splits is dependant on your body size. Given the points above, I wanted the main body to be under a meter, so I initially split the image into 20% segments. This ended up being too small, only about 75cm long. SO, I split it into 15% segments, and it ended up a much larger size, 89cm without the barrel. Another good test was printing out just the handgrip page - once I cut it out, it was immediately clear that the 20% segments were way too small for my hand to fit into the grip. 15% segments were much more comfortable, so I went with that.
To do this, do the following:
- load the image into GIMP
- select the Square Selection tool and select an area on the image - any area, it doesn’t matter
- use the tool options to set the current selection to the following figures. Ensure to select "%" from the drop-down box next to Position and Size, to ensue the figures are correct:
Position: 0.00 , 0.00
Size: 15.00 , 100.00
-At the top, select Image -> Crop to Selection
- Go to File -> Export As... And export the image as a PNG, name it like "1" or something
- Use CTRL+Z or Apple+Z to undo until you get back to the selection with the full image.
What this does is manually edit the selection area to start at 0,0 (very top-left), and select 15% of the width, 100% of the height. Then, it crops the image to that size, and saves it.
For the next section, repeat the above steps, except use the following figures:
Position: 15.00, 0.00
Size: 15.00, 100.00
This selects the same size area, but the next 15% of the image along. Export, undo changes, repeat.
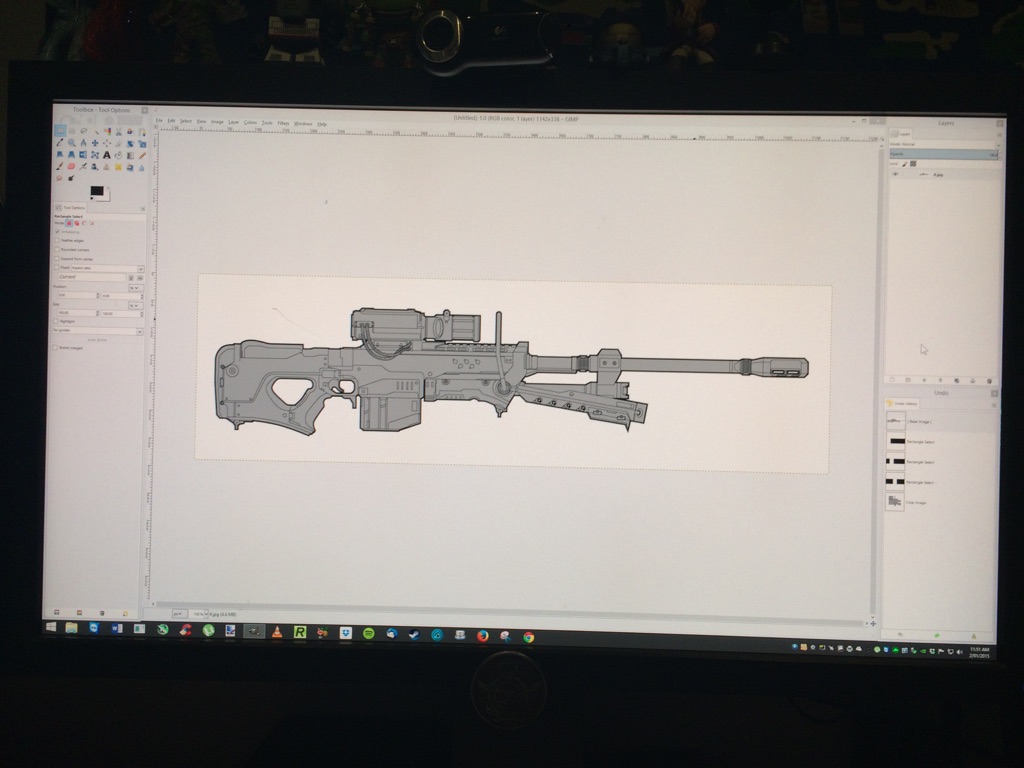
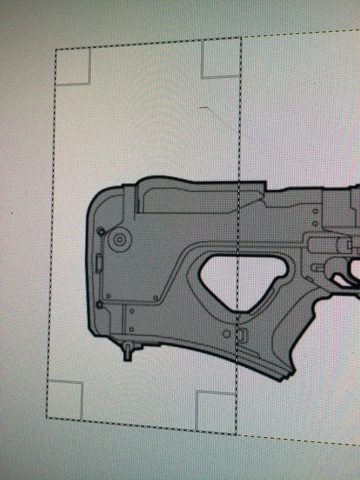

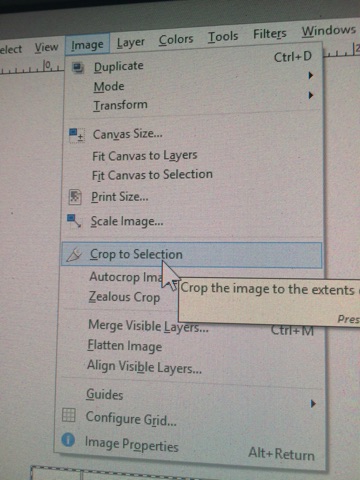
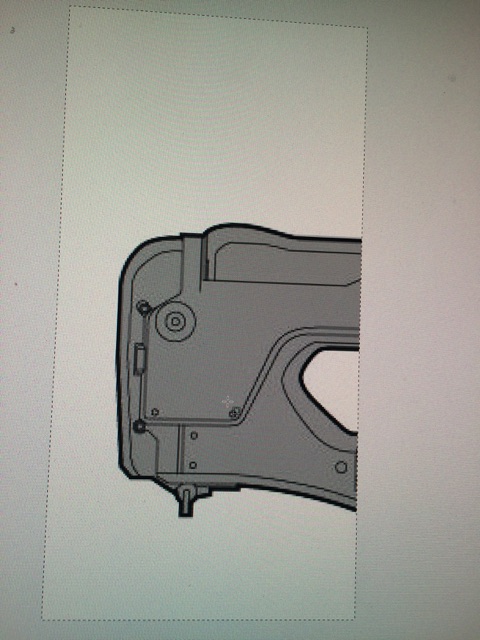
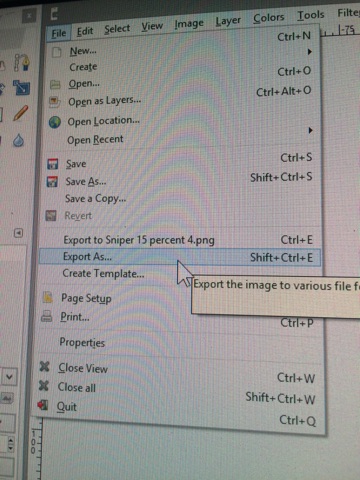
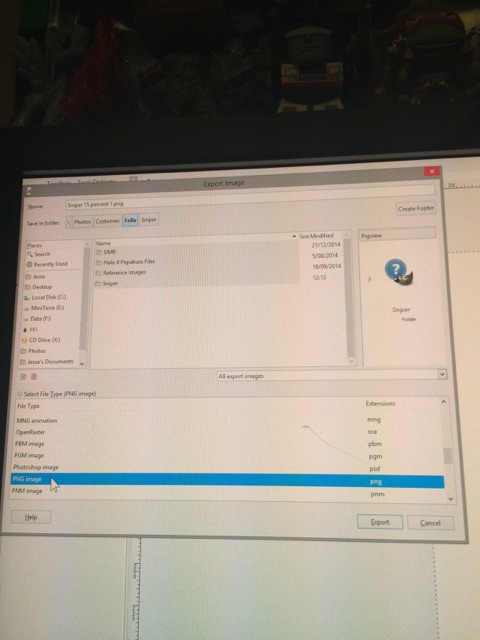
After the images had been split, I simply selected all pictures and printed each page at A4 size. As each one was the same size, they were all scaled the same and lined up with each other.
Next, I cut out every image, cutting off the barrel, trigger and scope, and cutting out the hole in the stock and trigger guard. I then taped them together, so I had a full template of one half of the body.
(pictured below with the DMR next to it for scale)
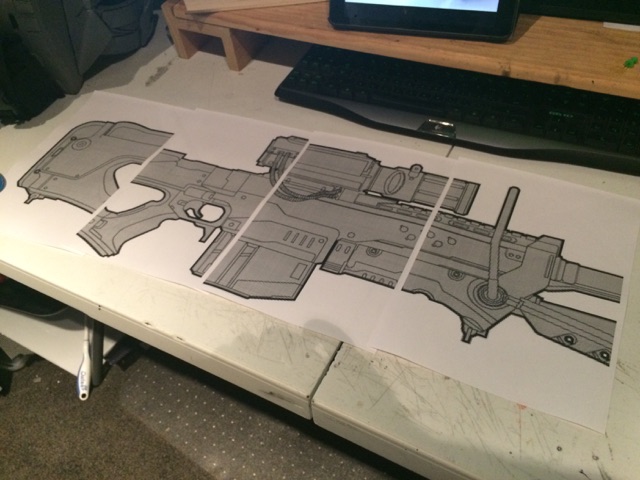
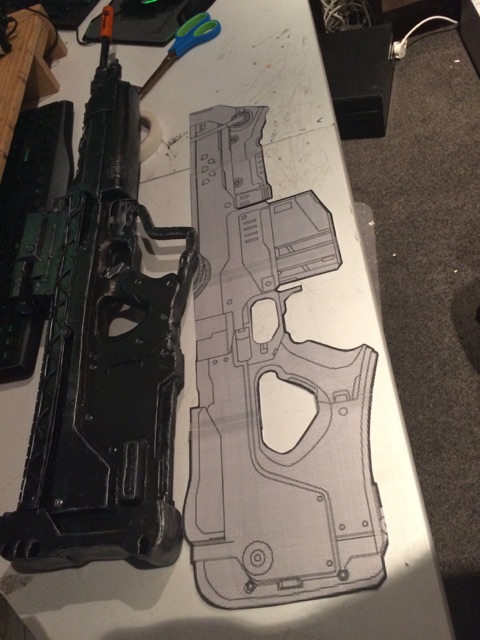
Aaaaaaaand then I repeated the entire process for the other side of the rifle - I reversed the individual images, rather than reversing the original and cropping it again*.
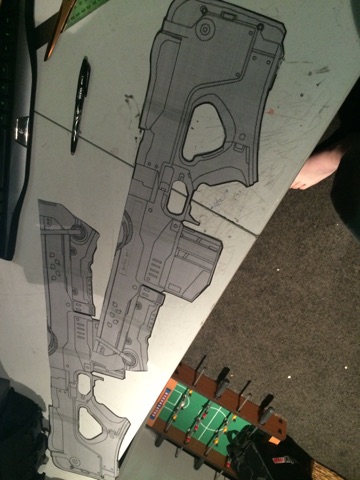
*Note: Like any rifle, both sides differ slightly - these is an opening on the left-hand side of the rifle for the cocking handle to slide forward and back, and a breach oh the right hand side (not pictured on the blueprint) for the bullet casings to eject. I added these openings after cutting the stock 'blank' out.
'BLANK' CUTTING
I traced each body template onto the EVA foam, so I had two - one for each side. I've edited these images to have high contrast, so the lines are a bit more visible.
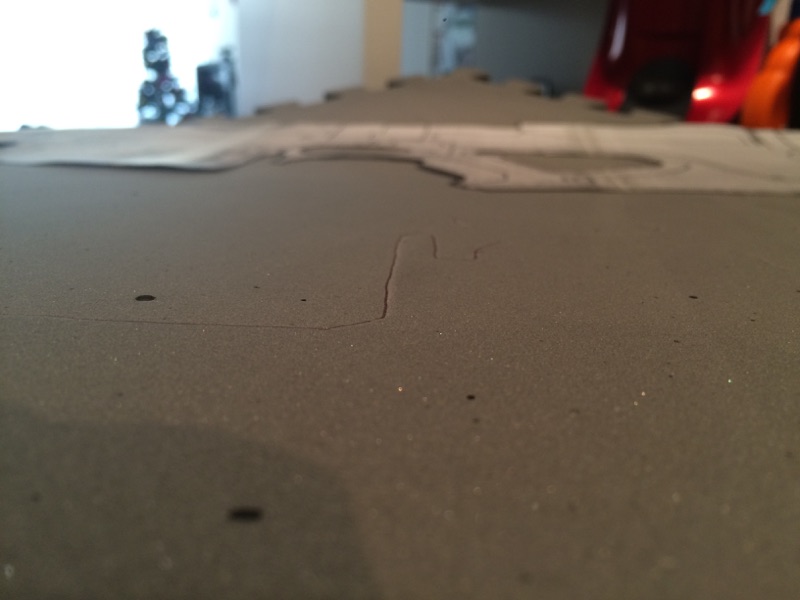
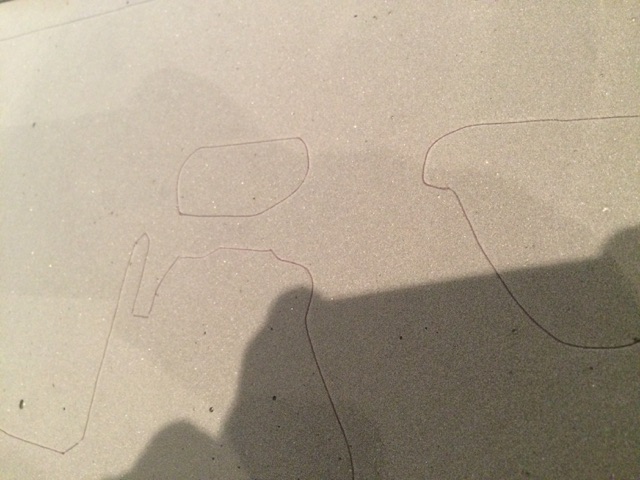
Then, I cut both sides out. Don't worry if the sides don't exactly match up, the sculpting/sanding will even them up with each other once they are joined together.
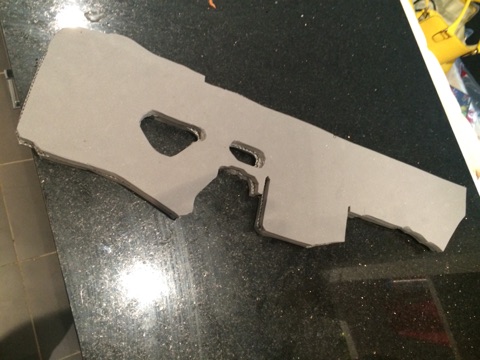
THE MAGAZINE
You may note that the magazine here is part of the body template. Something I noticed later in the process is that the magazine looked massively thick, and I realised why - I was raising the flat template to be three-dimensional over the entire thing, but not taking into account that the magazine is much thinner than the rest of the rifle. Take note of this if you do it yourself - it's easy enough to fix by removing the outer layer of foam, but better to do it in the first instance than later on. If you're following along, see if you can pick where I realised this, and thinned the magazine out ;-)
--------
More to follow in Part 2.
- - - Updated - - -
PART 2
-------------
BRACING AND REINFORCEMENT
As with any foam template, it's floppy and flexible when first cut out - not at all suitable for a prop or weapon, as it won't have the core strength to hold the rest of the rifle up. So, I use wooden dowel to stiffen the body of the rifle.
I started by drawing a line in sharpie on the underside of each side, to determine where the reinforcing dowel should go. To decide on this, you should try and make it go as long as possible along the rifle - remember, where you have gaps in the dowel, the foam will bend.
In the picture below, you will note that there is no reinforcing dowel that extends up from the handle into the rest of the body. This was a mistake I only noticed after I finished the entire thing and picked it up with one hand - when holding the rifle on the right (master) hand, when 100% of the weight of the rifle (including barrel and scope) is being held on that small bridging section between the trigger opening and the thumb hole in the centre of the body, it flexes a fair amount around that point. To fix this mistake, all that would have been required is the dowel in the handle to be extended up to meet the other one that runs down the entire length.
It's a bit of a physics puzzle, but it's only a huge issue for very heavy rifles - if you try to think about where the weight will be when it's finished, you can estimate it reasonably practical - and if it doesn't work out right, the easy solution is to always hold it in two hands or not by the flexible points!
Continuing on, once you've decided where the dowel goes, cut 45 degree cuts along the line, to leave channels for the dowel to fit. At this stage, I glue the dowel into the side of the panel, rather than try to guess where the channel should go on the other side. Once the dowel is glued in, use a paint marker, paint or other wet substance to paint the uppermost part of the dowel (the side that will touch the other side of the body blank), line up the opposite of the blank as if you were putting it together, and press down. This will leave a mark on the inside of the opposing side of foam, telling you exactly where you should cut the channel for the dowel on the opposite side.
If you want your rifle to have some "bulge" or thickness, this isn't hugely necessary to carve out channels for the dowel - but it's more necessary the thicker the dowel you use to strengthen it.
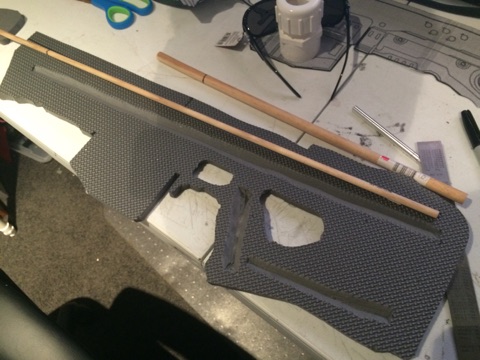
Once the grooves are cut on both sides, use liberal amounts of glue on the inside of one of the sides, and glue it to the other side, lining the dowel channels up. If the glue is decently hot, you can slide the sides against each other, finding the channels with the dowel on the other side and feeling it slide into the grooves. It's more important to gave the dowel fall into the matching groove than the edges of the entire body matching up - the adhesion between the two halves is the building block and basis of strength for the entire rifle, so it's important to ensure the dowels have good adhesion to each side.
Wow - that's a lot of effort to stick two pieces of foam together! But trust me, now comes the fun part :-D
SCULPTING THE BLANK
Now the sides were glued together, I marked the edges where the square edges need to be rounded. For this rifle, I rounded the handgrip, the thumb hole in the back of the stock, the trigger hole and basic bevelling around the edges where nothing would be glued on top (bottom of stock, magazine etc). The front hand grip had to wait until all the panels were on the front of the stock.
I used a Dremel or similar rotary tool (i'll refer to it as a Dremel here, as it's what I use and it's pretty common) to sculpt the above sections and to make each side line up with the other. Some areas were significantly out of line, so a lot of sanding was necessary.
OUTER PANEL SCULPTING
Starting from the back, I cut the blueprint up part by part into sections that needed to be added on as extra layers on top of the base two layers. For each part, I traced the paper onto the foam, cut it out, and reversed that piece onto more foam and traced/cut a reverse for the other side. The first part was the back upper stock:
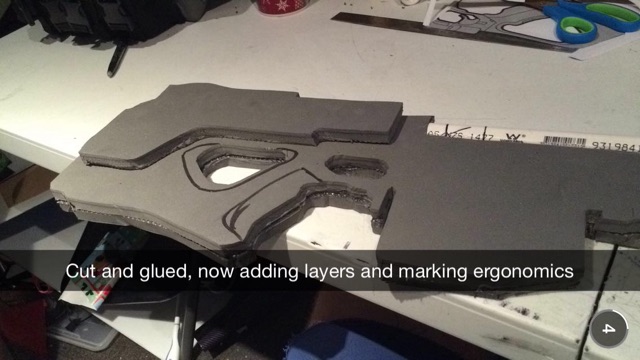
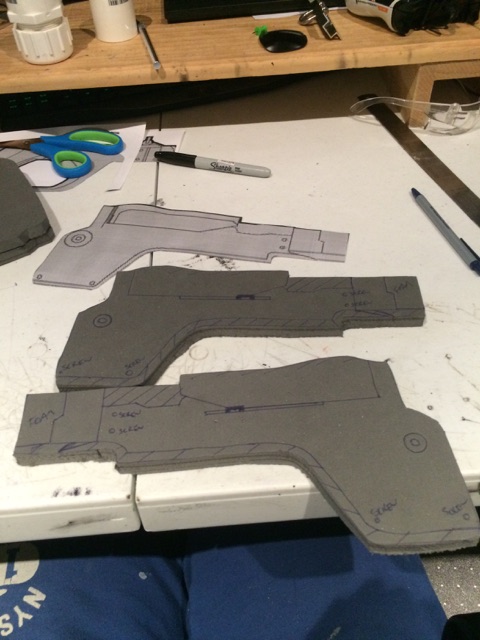
It's much easier to sculpt/bevel each piece while it's off the rifle, so I sculpted a lot of parts before they were glued to the rifle, rather than after.

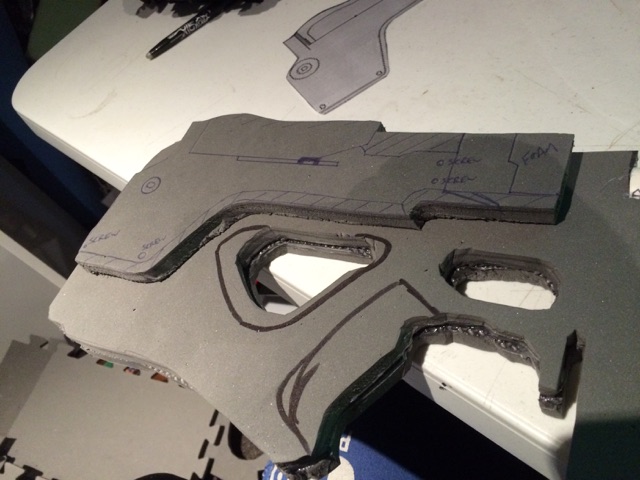
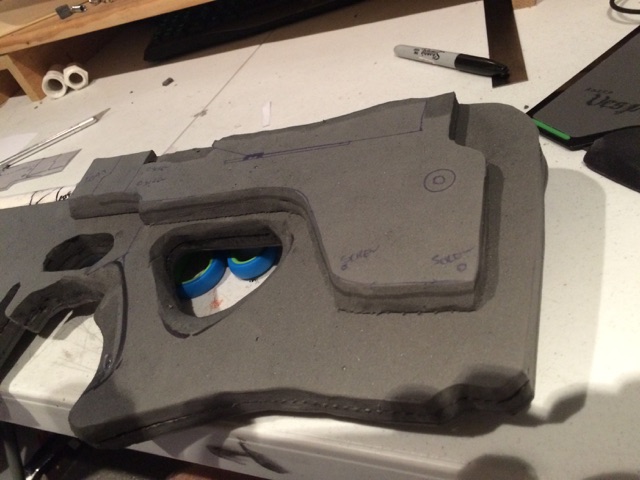
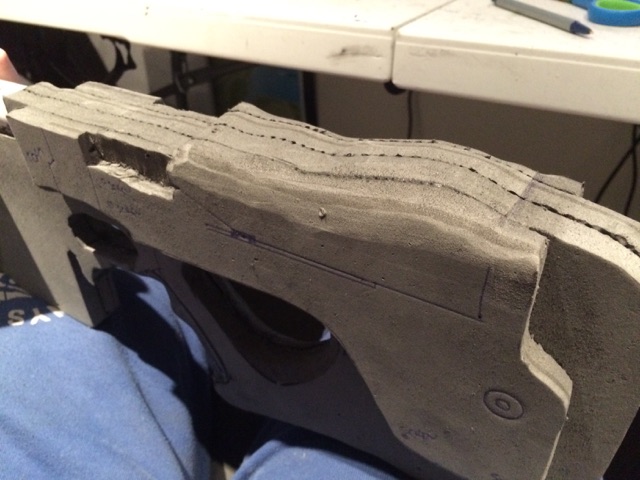
LINE DETAILING
I used a hotknife to cut the foam, but it also had another use: fine line detailing. Using the blunt side of the Xacto blade in the hotknife, I ran it over pen lines I drew onto the body to create recessed lines that weren't cuts, but fine enough to look detailed.
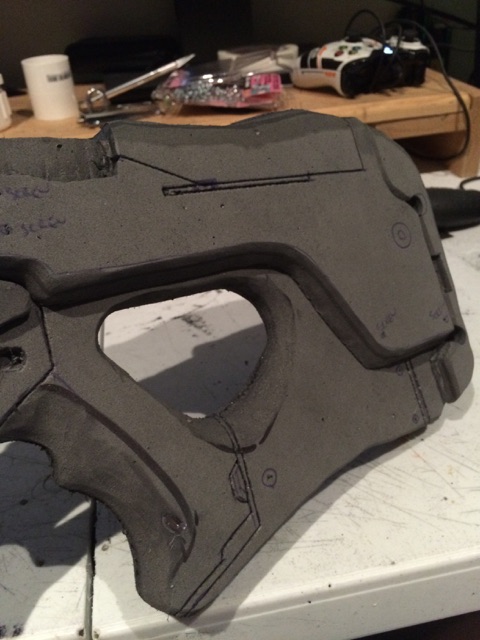

BARREL
The barrel, needed to be removable, so the easiest way was using plumbing pipes. I picked an appropriate diameter pipe of a meter length and a connector, and cut it to it was extended into the body as far as it extended out from the end (50% in, 50% out). This part needed to be extremely stable, as the barrel extends a long way and needed to have reinforcement in case of knocks and able to hold up the rest of the barrel without bowing or bending.
I decided to make the 'join' the combined section out the front of the rifle where the gas cylinder (small, extra barrel) meets the main barrel, so I cut the pipe to fit so the join was there. I then cut a large section of the body out, and glued the pipe on top with, I kid you not, two full sticks of hot glue.
I also used some dowel to make the gas cylinder, and cut a slot for that and glued it into place.
From there, I cut the outer panel for the rest of the body, and stuck it over the body centre to hide the pipe and the gas cylinder dowel.
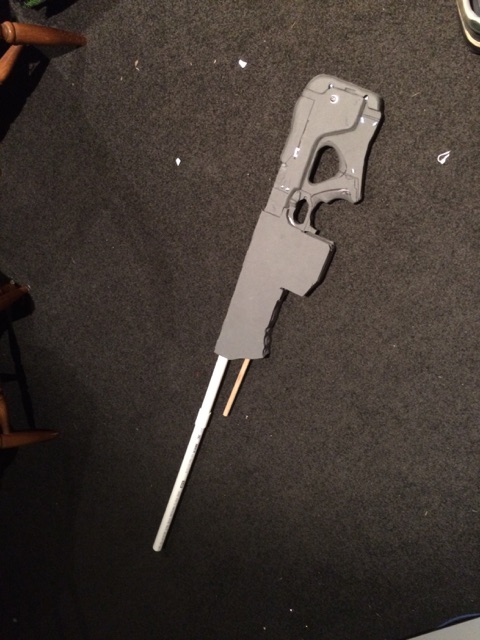
I then sculpted the front hand grip, and continued adding panels to the rest of the body:
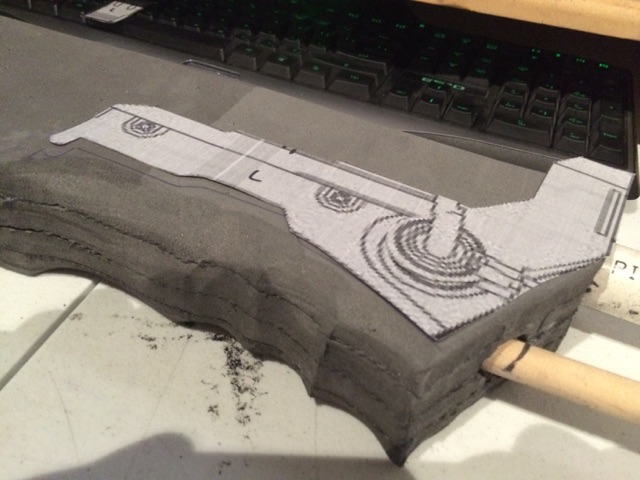
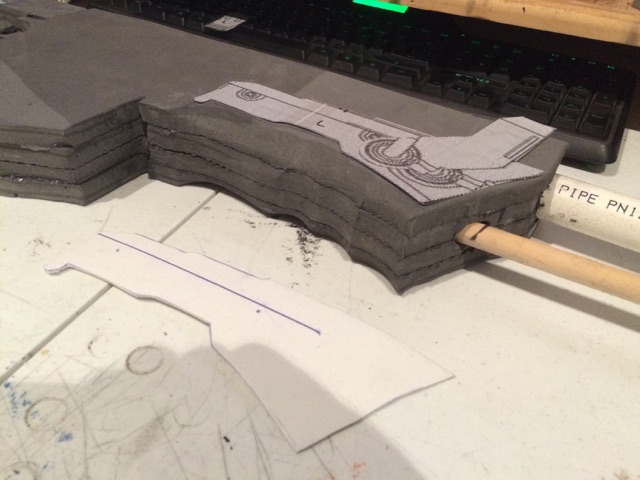
THIN PANEL DETAILING
As the larger parts were all close together and didn't need large parts for detail, I did the rest of the sculpting for the body in thin self-adhesive craft foam, with real screws for a detail or realism.
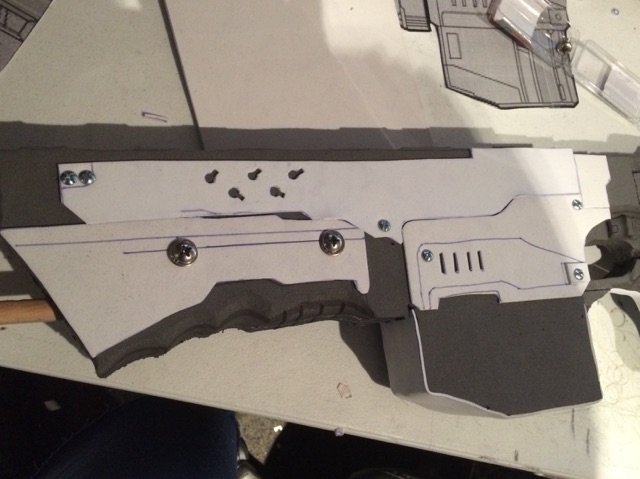
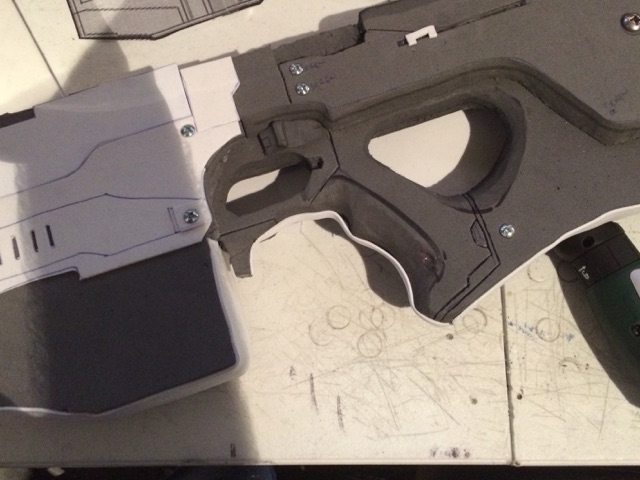
COCKING HANDLE - PART 1
For this rifle, I wanted a real, working cocking handle that actioned like a real rifle. I achieved this using a D-Bolt, a door latch and some springs.
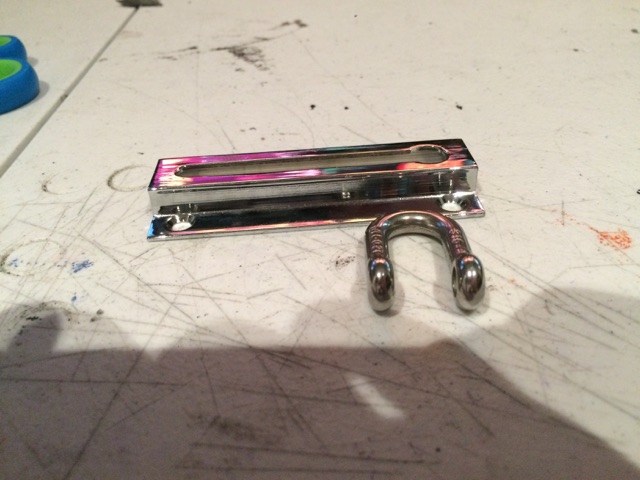
I cut a recess to match the latch in the body, and covered the back of the recess with aluminium foil tape, so the action could slide smoothly and easily.
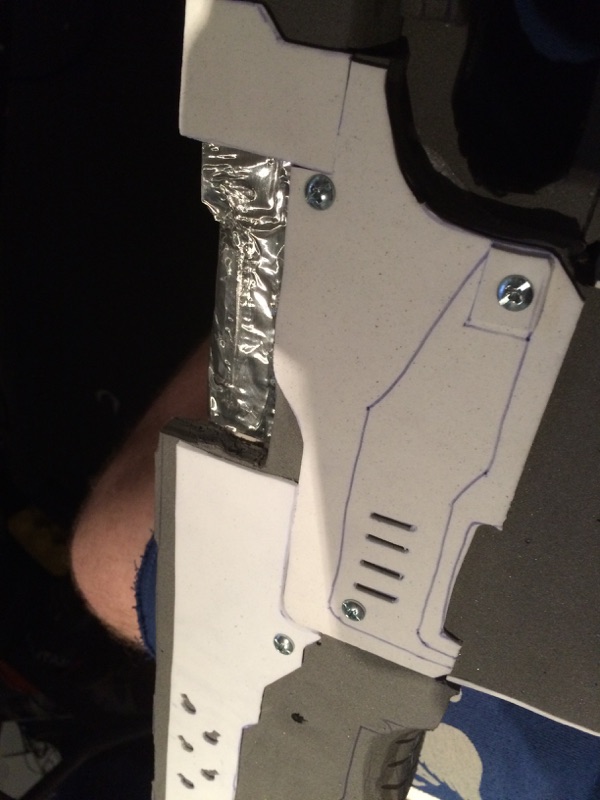
I then glued the latch into place, leaving the d-bold to slide freely. I would continue this later.
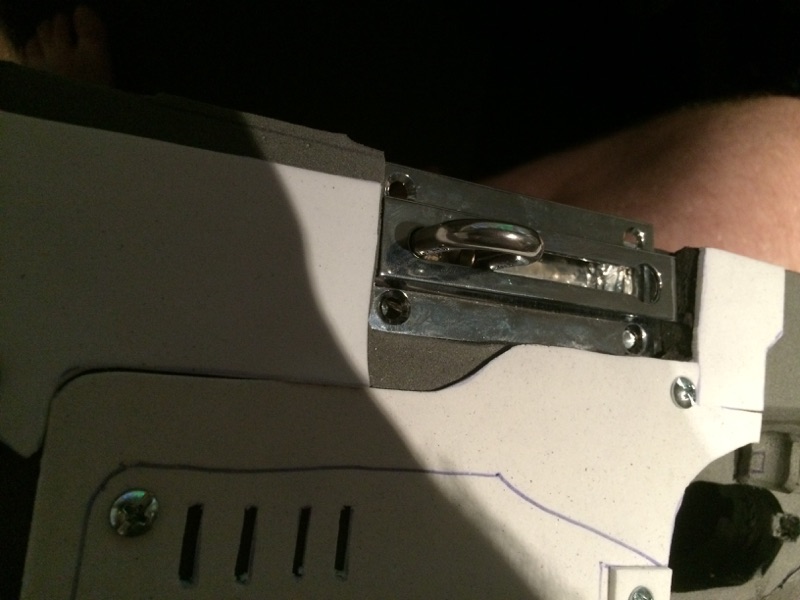
MORE FINE DETAILING
Contined with the detailing for the front. I used a pen body for the sling latch connector at the front.
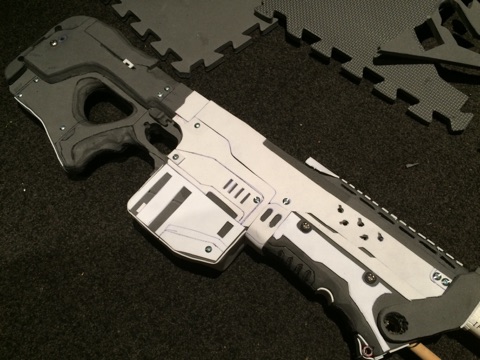
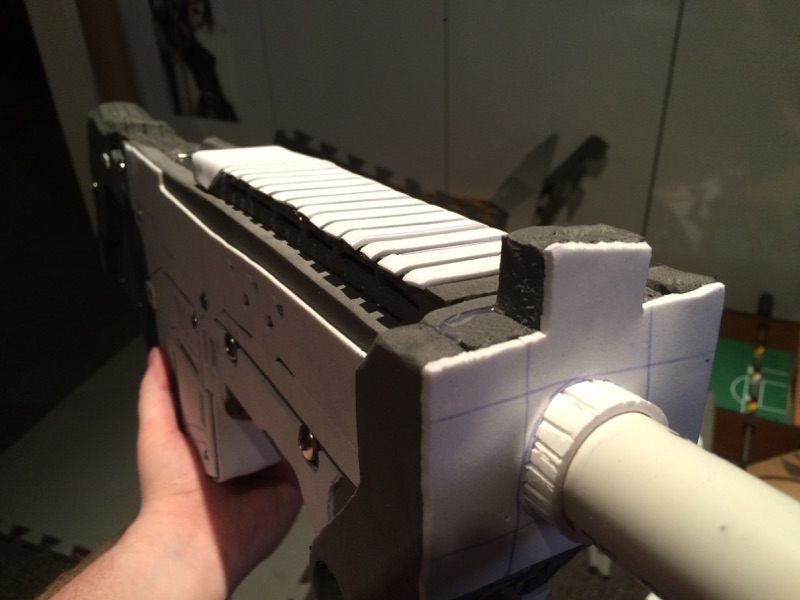
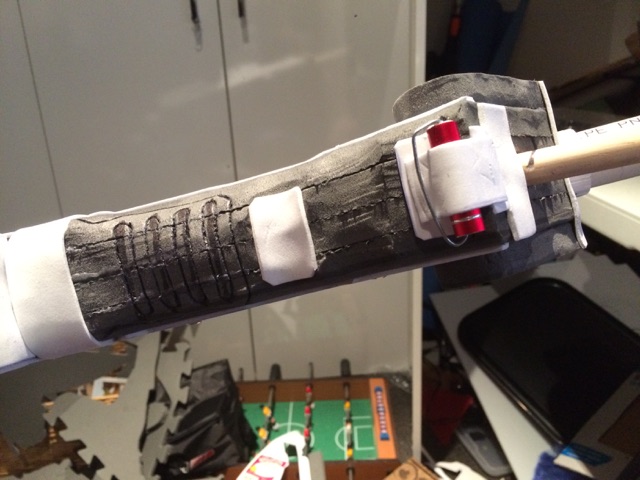
More to follow in Part 3.
- - - Updated - - -
Part 4
------------------------
GAS CYLENDER, CONNECTOR AND FRONT OF BARREL
I used a highlighter lid with some foam additions to make the end of the gas cylender.
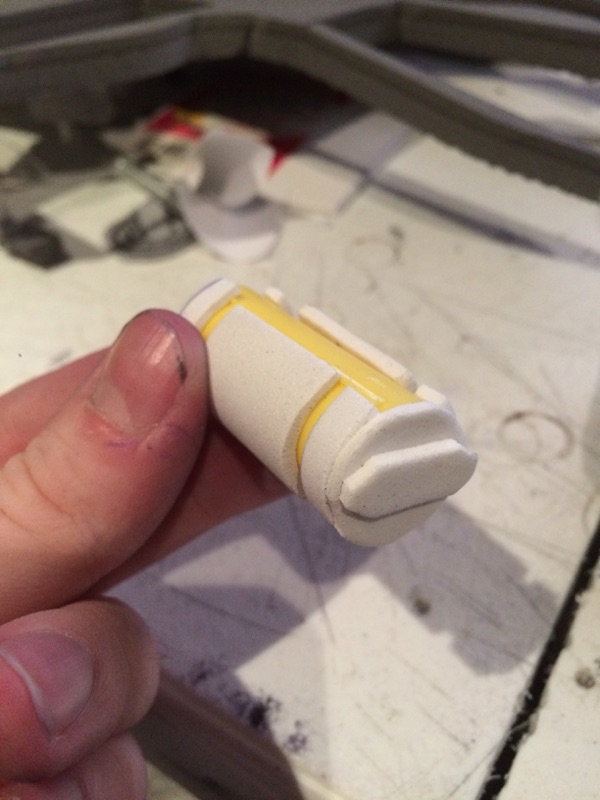
I also used some foam offcuts to make a surround for the connecting sleeve, and sculpted that to fit.
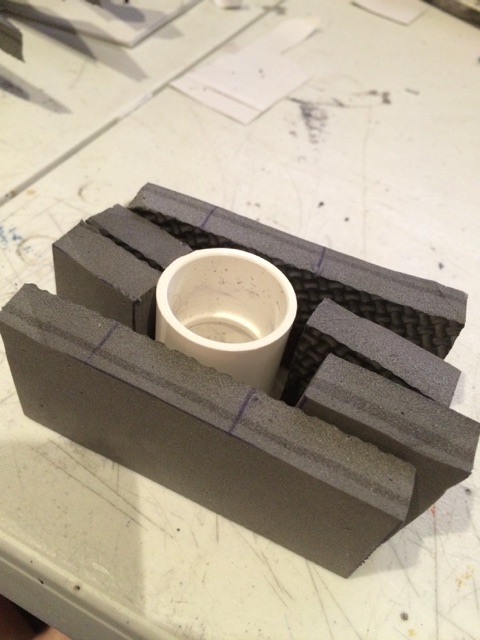
Eventually, it was all connected together - the body was pretty much done. And best of all - JUST under a meter long.
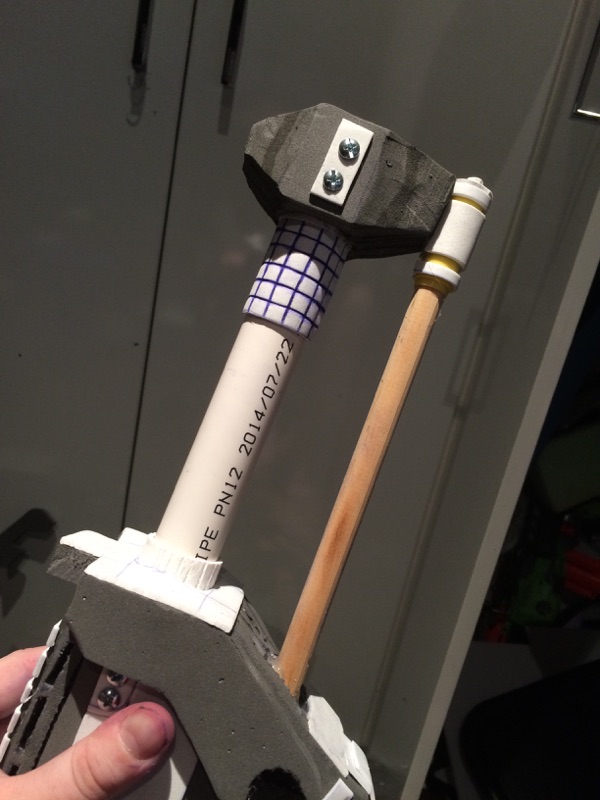
The rest of the pipe needed a flash suppressor, so I used some foam blocks cut to shape, with the plastic back of a notebook to do the top and bottom and the barrel hole.
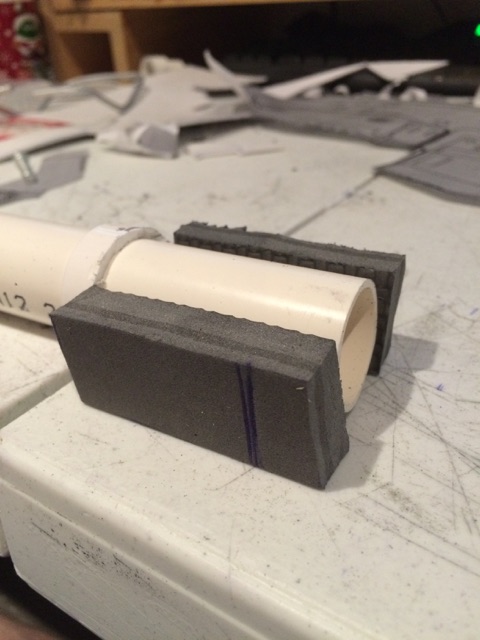
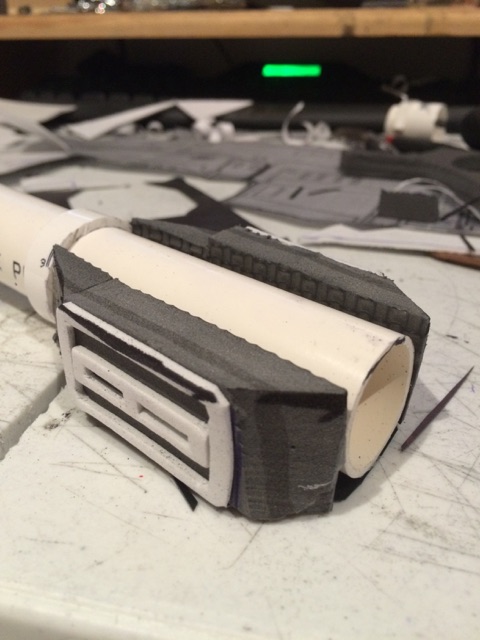
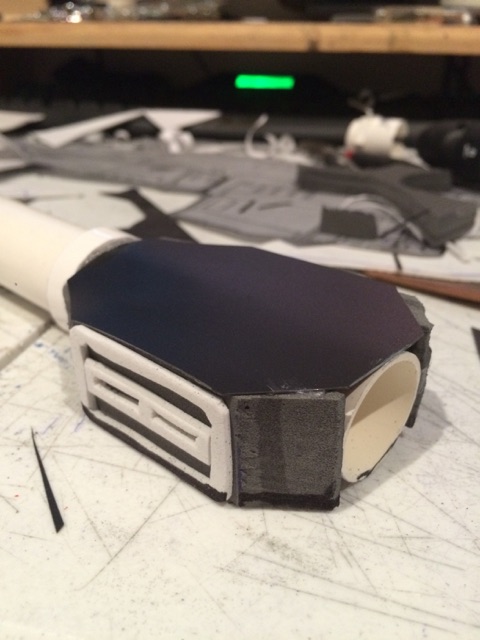
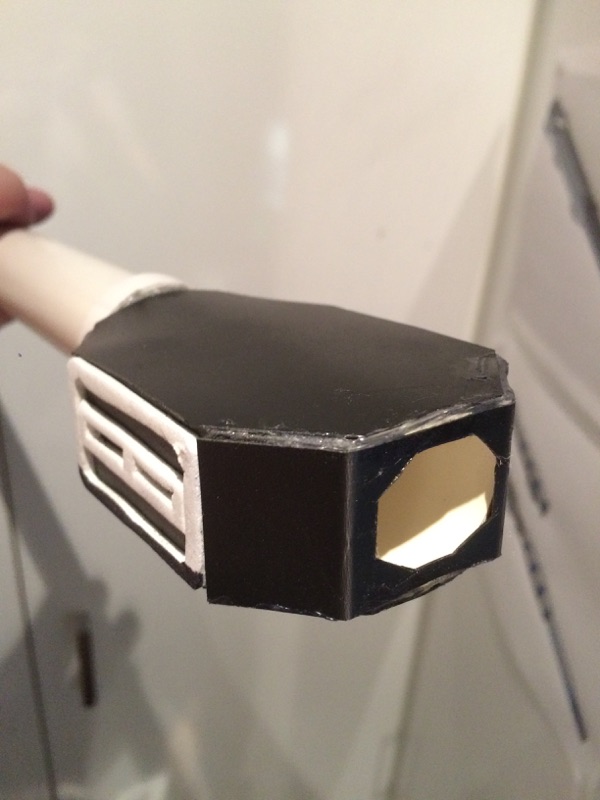
So the basic sculpting was all finished, with the assembled length totalling around 140cm:

....and it left a hell of a mess.

TRIGGER
I cut the end of a wooden spatula and sanded it to shape with the Dremel, to make a trigger.
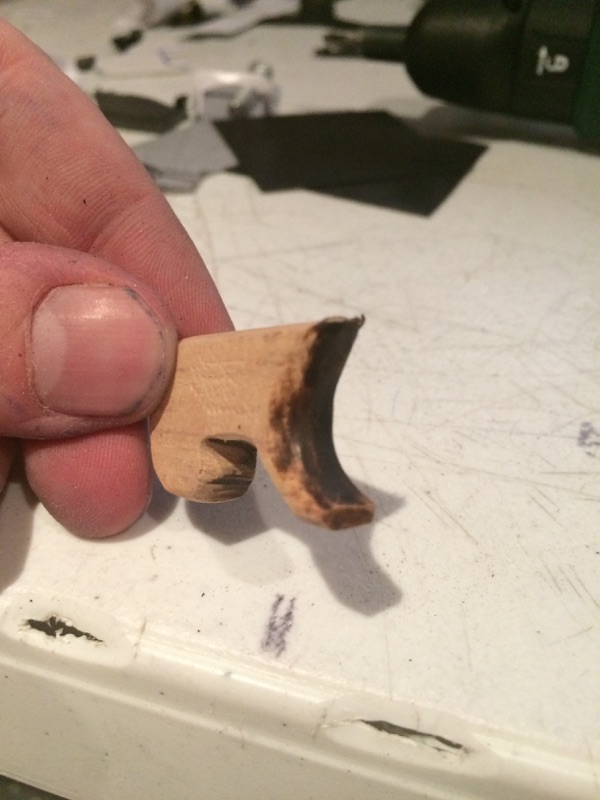
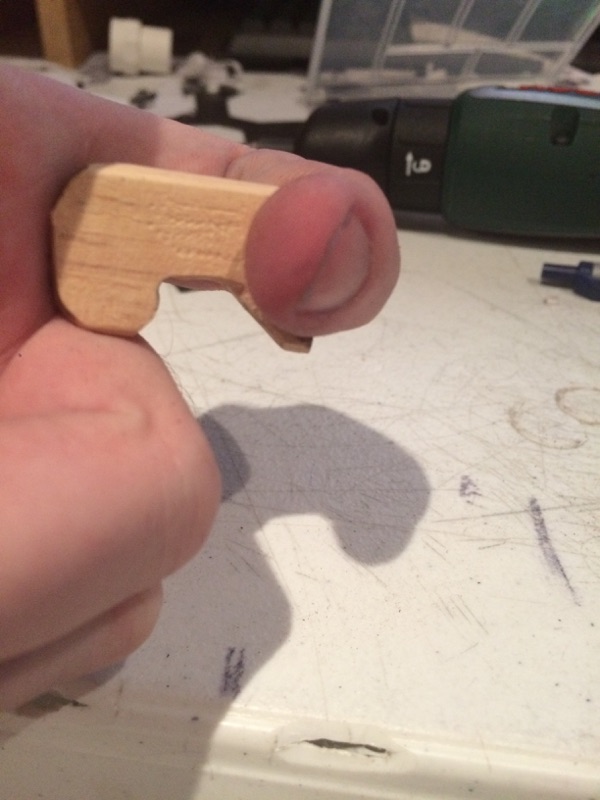
I then glued it into place:
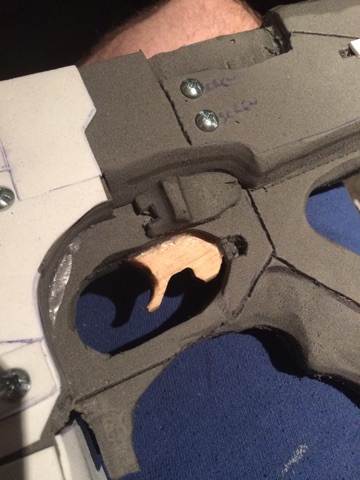
COCKING HANDLE - PART 2
I used two ends of a ruler with a bolt through the middle to connect the rest of the spatula handle to the D-Bolt, to extend the cocking handle.
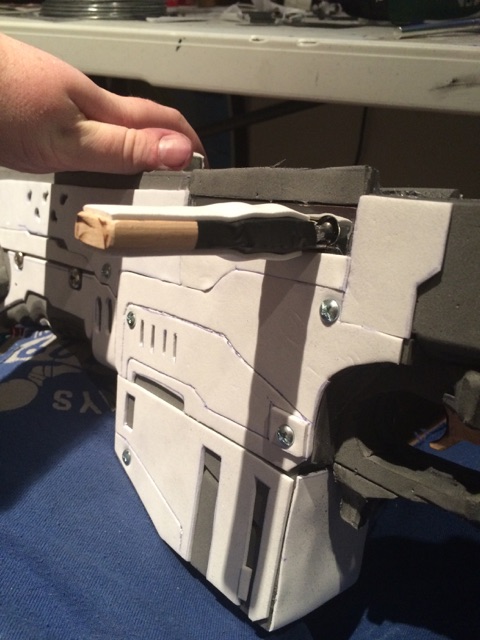
It's worth noting that I cut this down significantly later on, as, while it's the length it is in-game, it also sticks (a) into my chest with the chestplate on, and (b) into my back when wearing it over my shoulder.
More to come in Part 5.
- - - Updated - - -
Part 5
----------------------
SCOPE
The (first) scope I made was based on the idea of wanting to be able to actually look through it. So, I decided to base it around an *actual* scope, a $20 metal airsoft scope I bought online.
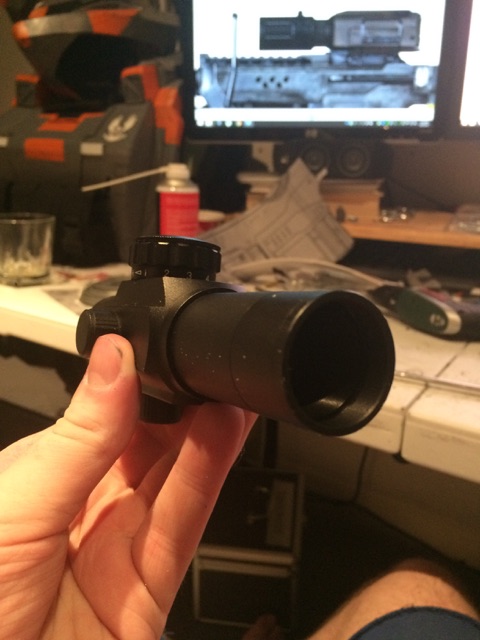
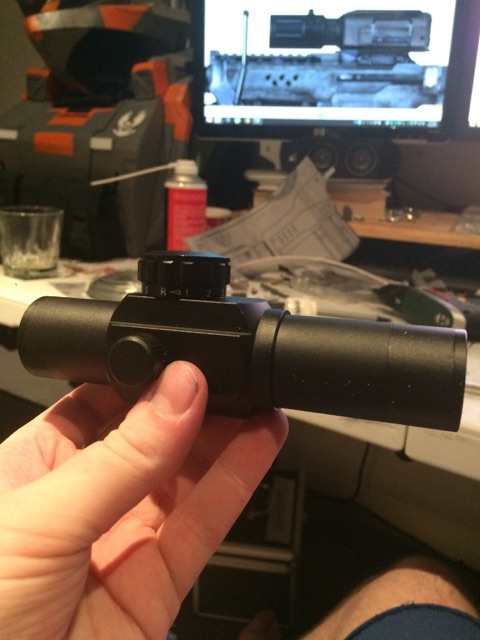
To emulate the actual scope barrel, I used some plumbing parts, with a sanded-down sunglasses lens from The Reject Shop:
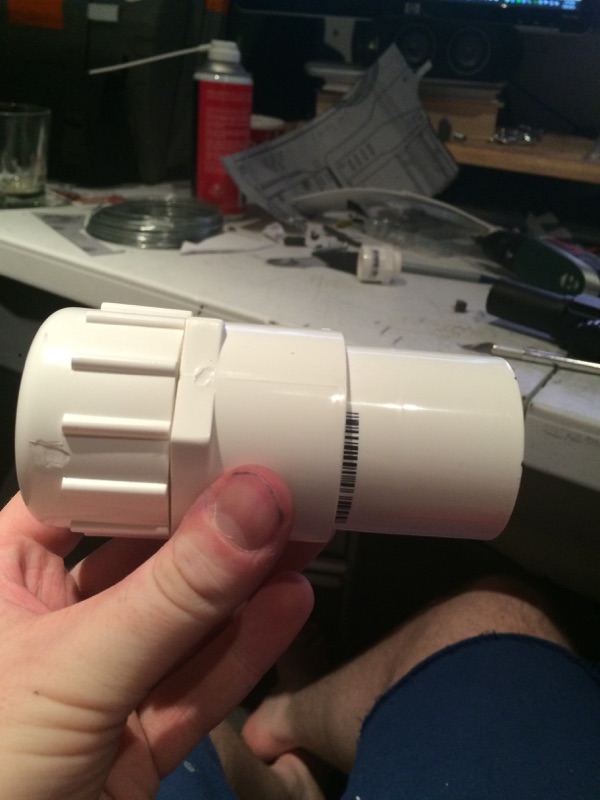
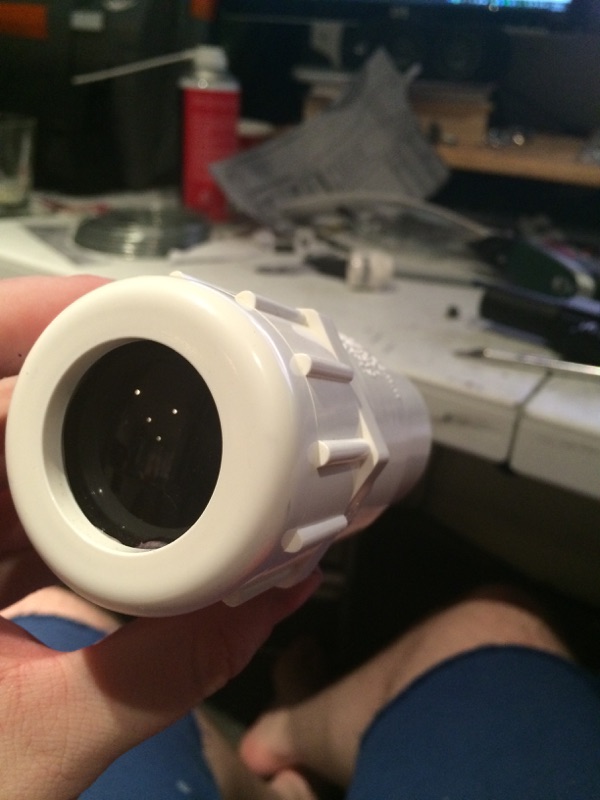
The challenge from here was the shape of the scope - it needed to have one round side, and one flat side. So, I glued the round scope front to the airsoft scope, some smaller pieces to the eyepiece, wrapped some craft foam around to make it all the same width, and heated/wrapped a piece of EVA foam around it to form the body.
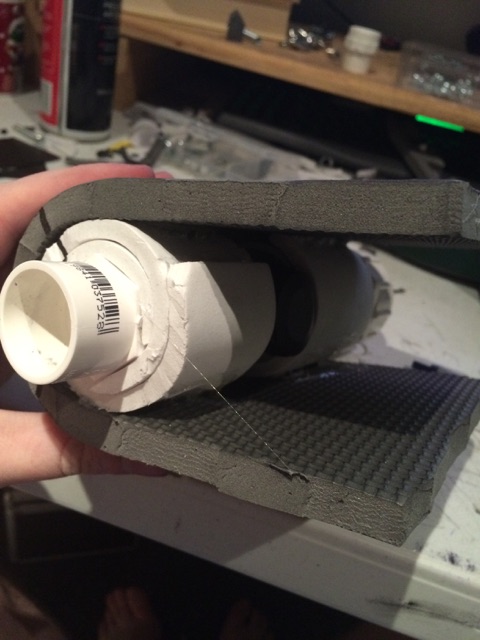
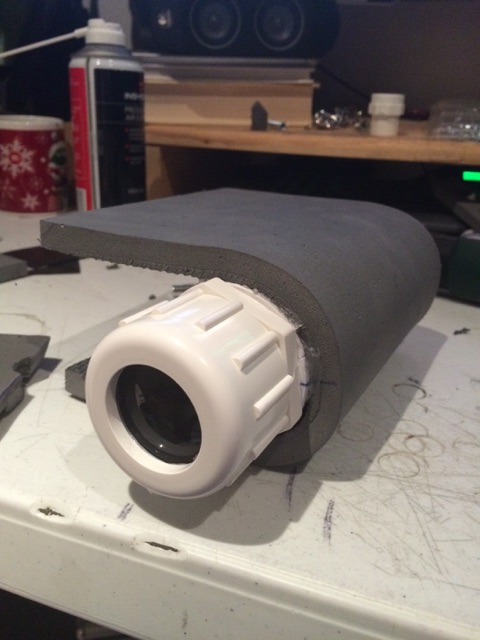
From here, I cut a rectangle of EVA and glued in some earth magnets, to make a square side that was detachable.
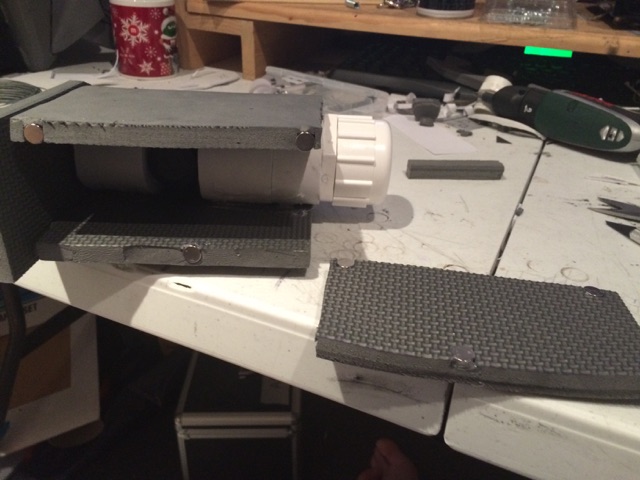
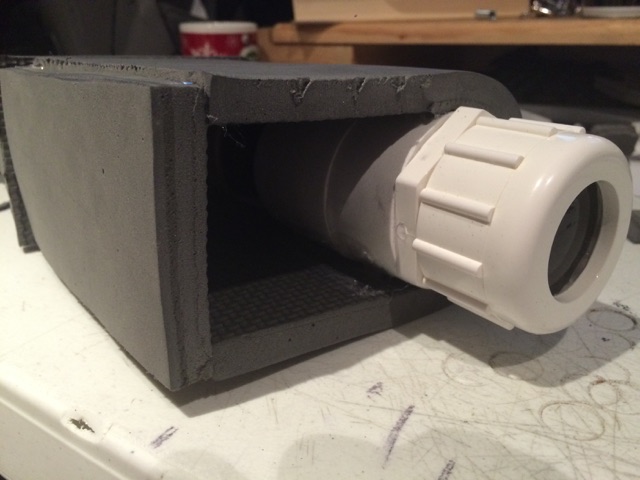
The front panel was easy, just had to leave space for the two scope lenses. The back is where the difficulty lied. I drew out the details of what I was going to craft out first, to size it up first.
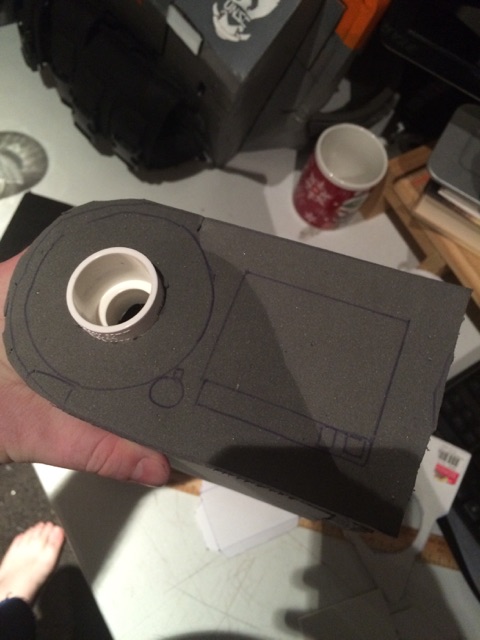
I crafted the eyepiece from layers of craft foam.
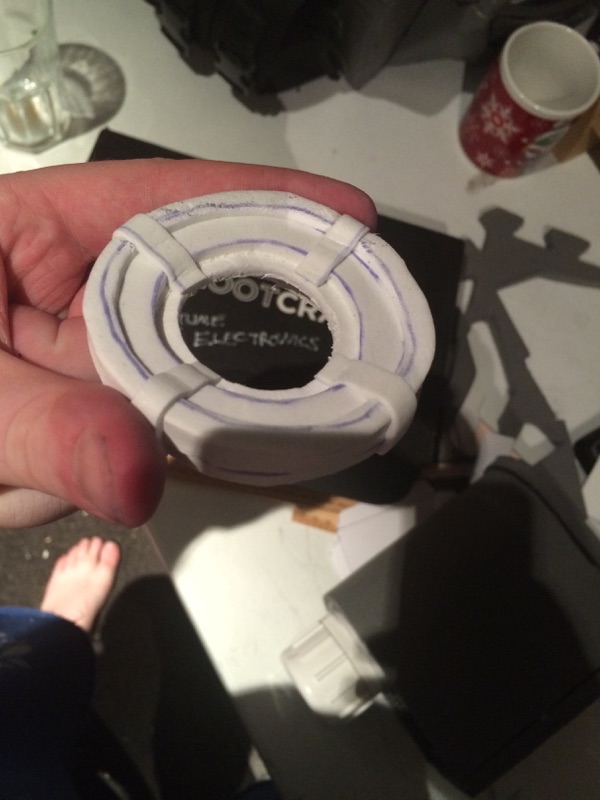
The screen was a challenge. I ended up settling on an electroluminescent panel with a black and white scope overlay over the top, so when the panel was on, it would shine through.
[NOTE: I've since changed out this scope for a better scope - update to come!]
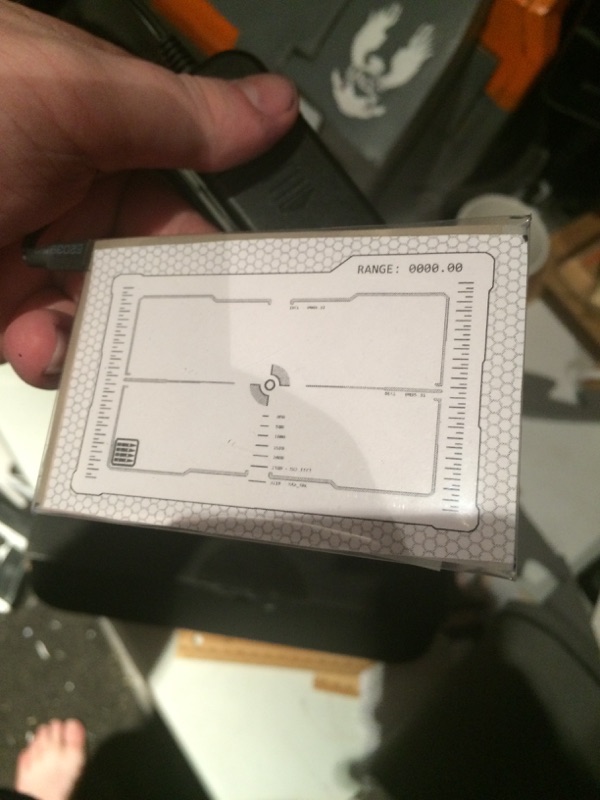
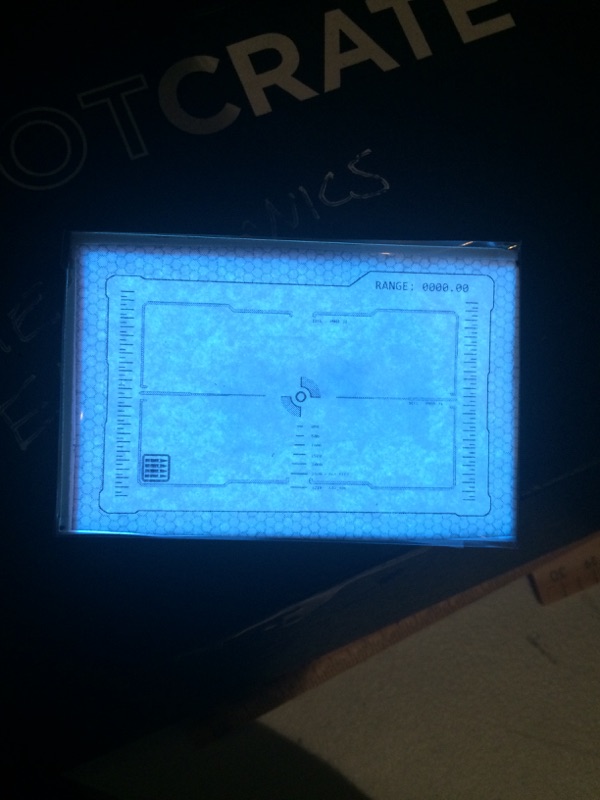
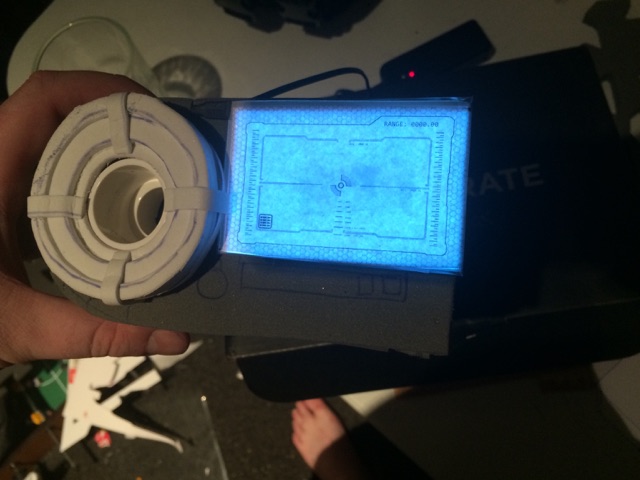
After getting the screen size correct, I then set to adding the rest of the detail in EVA, screws and craft foam, until the overall shape complete. I used a detergent bottle as the holder for the other (left) lens. Overall it turned out ok, but if I did it again, I would do a few things differently.
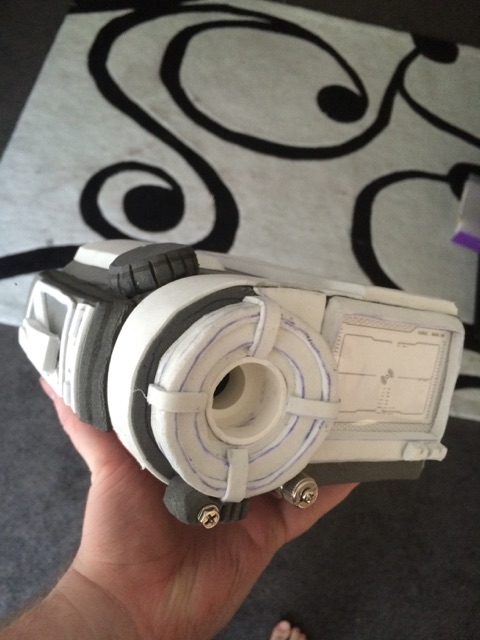

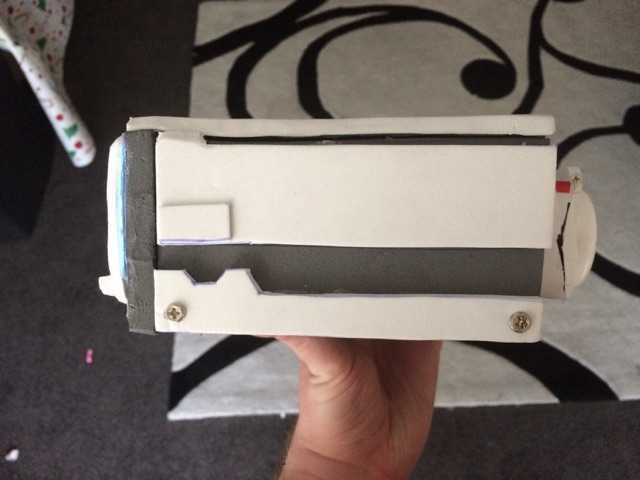
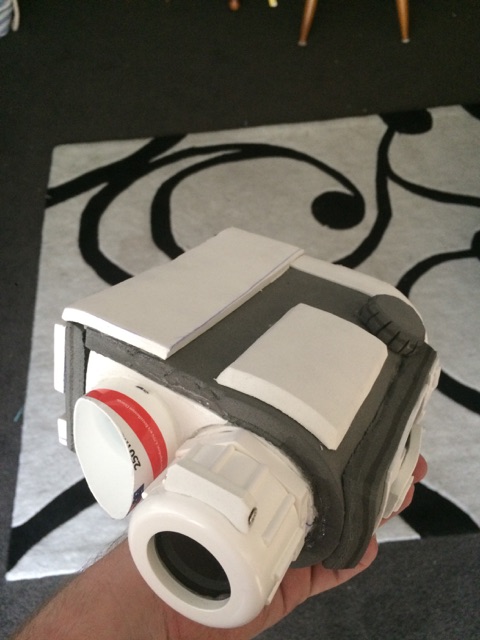
Inside the scope was the driver box for the EL panel, which could be removed to turn it off and on.
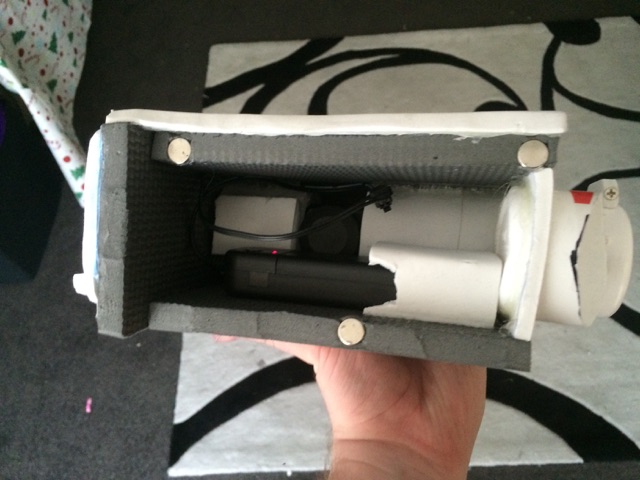
Best of all, the green dot on the scope could still be seen!
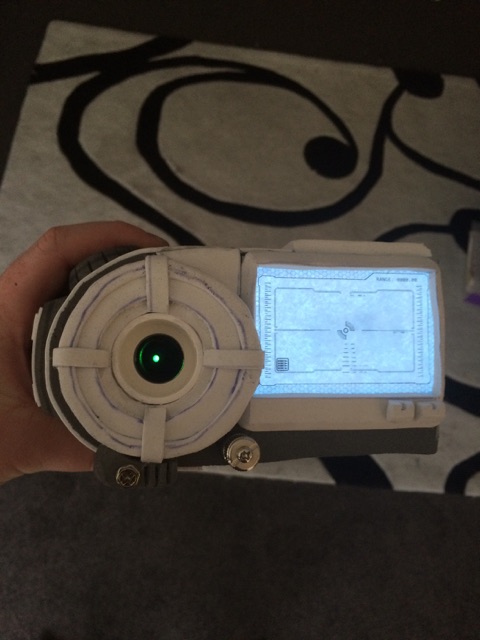
I sat the scope on the rifle to get an idea of the overall scale of the rifle. It was much heavier than I thought, but the scale looked right. I also tried it with my helmet and chest, to see the scale with my body.
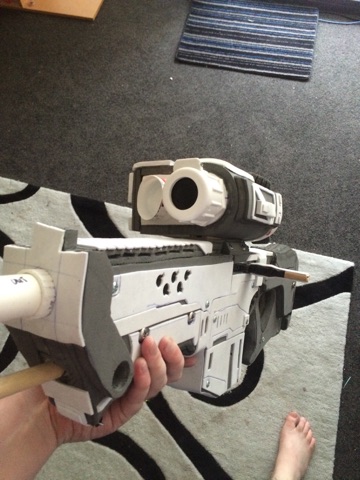
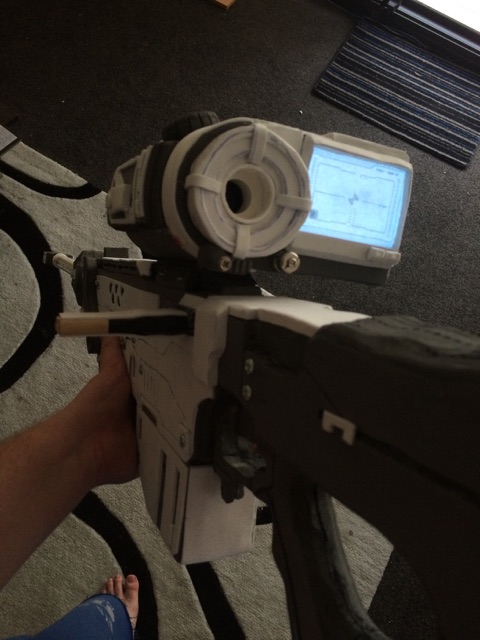
BIPOD AND CARRY BAR
I was initially thinking of making the bipod legs from plastic or foam, but they were too bendy. I went with some spare MDF, which was stiffer and I had spare. I cut them out and sanded them, added detail with craft foam and screws. I found that they wouldn't support the full weight by themselves, but by affixing a joining screw in between the end of the legs, they stood a much better chance of standing up.
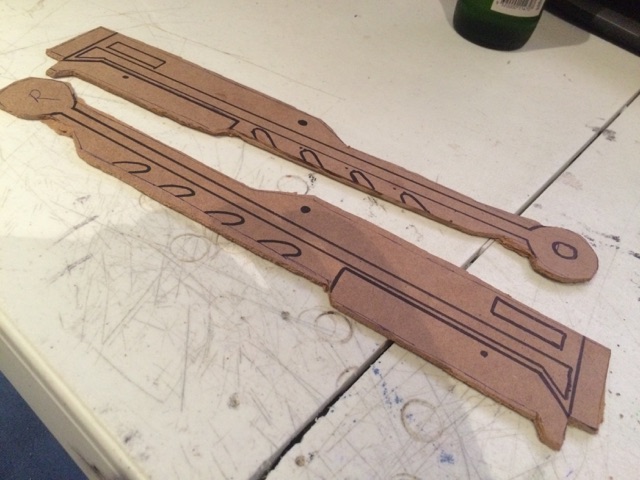
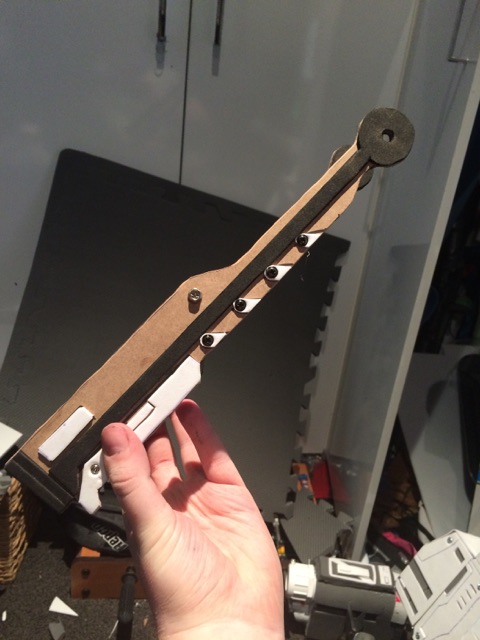
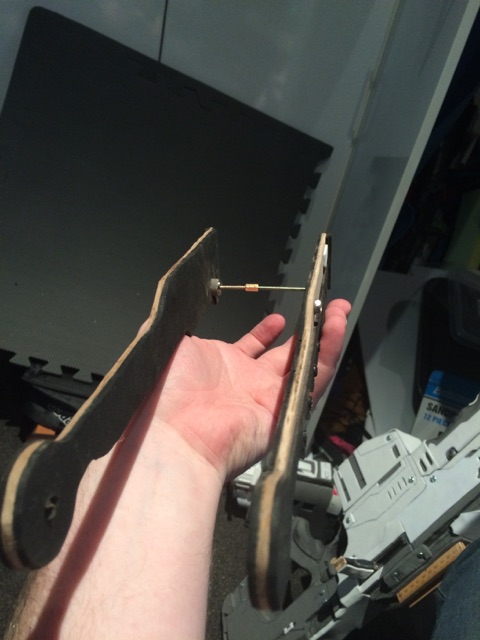
More to follow in Part 6.
- - - Updated - - -
Part 6
--------------------
I also used some thicker armature wire to make the carry bar in front of the scope.
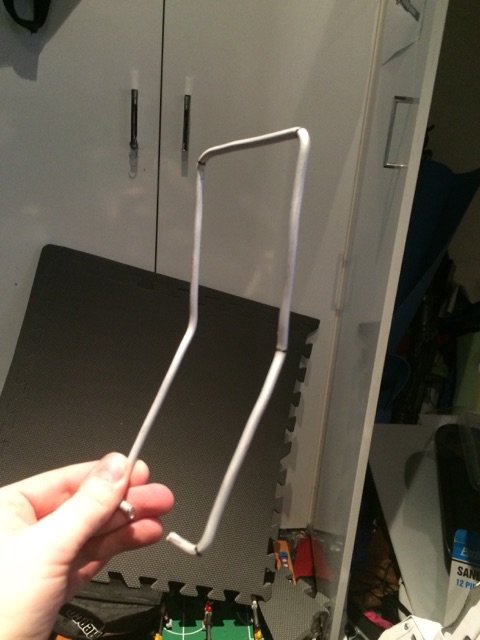
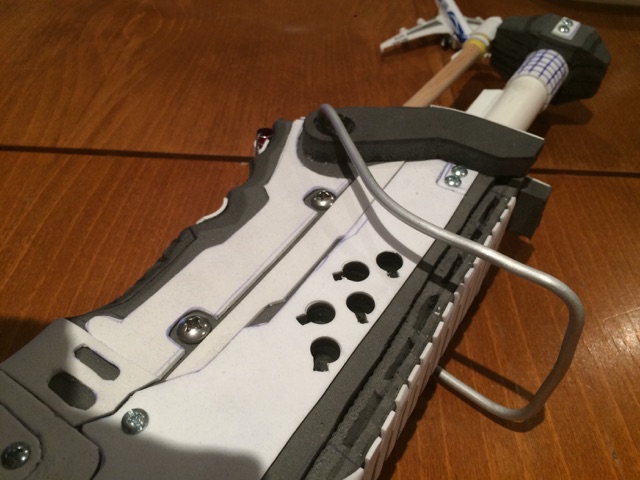
The point where the bipod legs and the bar met the body of the rifle was just foam, which I drilled out to make an area for the bar to go into. The area was under too much strain to use standard hot glue, so I filled and surrounded the area with Aryldite (2-part epoxy glue) to make it solid. Due to the natural "give" in the foam anchoring the legs, it doesn't stay upright on the legs for very long before it bends over.
LAST GEOMETRY CHANGES
No pictures, but you will notice in the final geometry pics that the magazine is a lot thinner. This is due to me, as mentioned above, thinning down the magazine to make it more realistic.
I also decided not to put an ejection port in until I got a prop round to put in the gap - give some up-close realism to the rifle. I later decided this wasn't a good idea, as this may have made the prop more difficult to take into cons. It's still an idea, but one I probably won't go into.
Lastly, I shortened the cocking handle by 3-4 cm, for comfort.
FINALISED BODY/SCOPE PICS
These pics are the final draft of the entire rifle, with the scope propped up on a paint can. I was very pleased with how it turned out, and the details looked great!
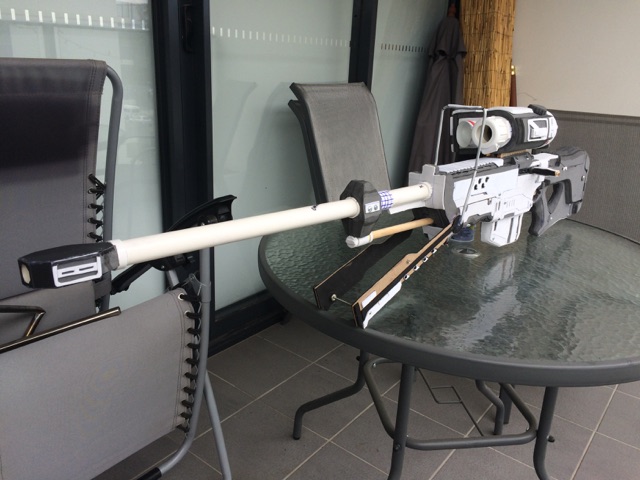
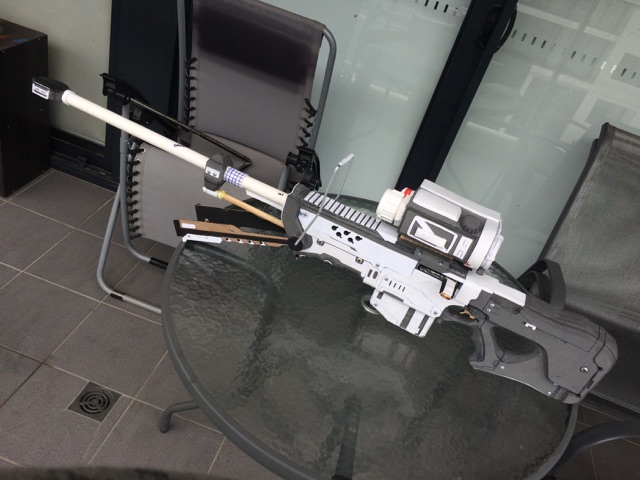
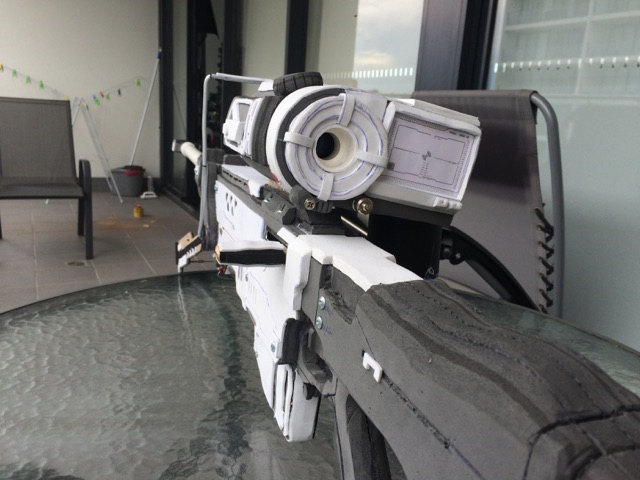
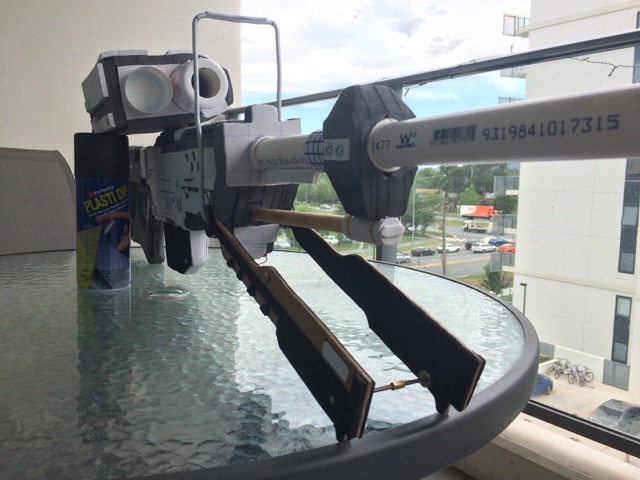
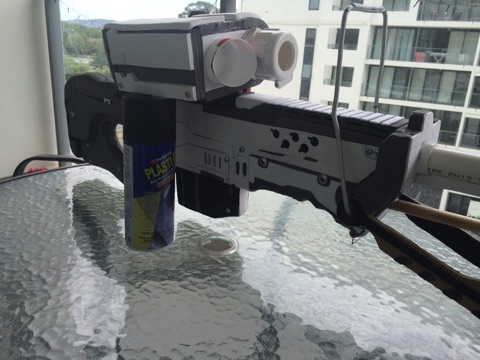
SCOPE CHANGES
While I was PVA sealing the rifle, I made two changes to the scope.
Firstly, I inserted a plumbing extended into the scope, to make it more like the actual scope. This was heavy, but necessary.

I also decided to make the cable seen in the reference pic. I got an old iPhone cable and wrapped it in some cable wrap, then covered that in shrinkwrap to make a textured, thin cable.
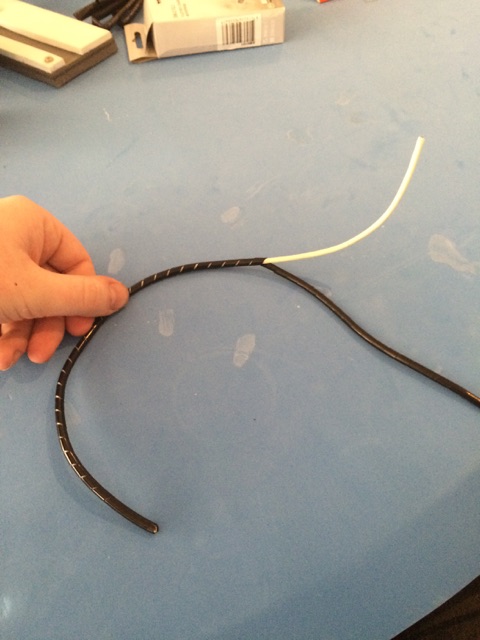
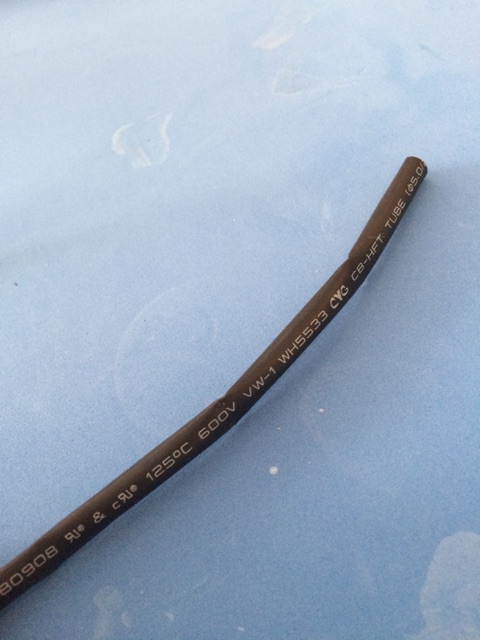
I glued some RCA connectors I got from JayCar electronics for $0.10 on each end, mostly because I liked the look of the ends.
Finally, I glued an RCA wall socket plug into the rifle at the section where I connected the scope to the body.
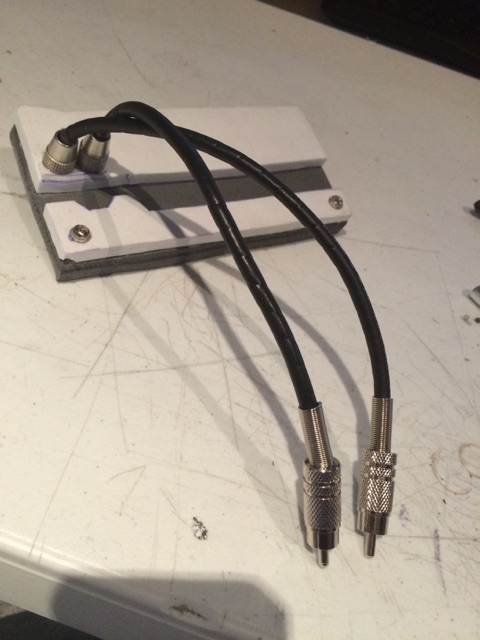
Overall, the cable effect was more pronounced in the real life than the pic, but looked cool nonetheless.
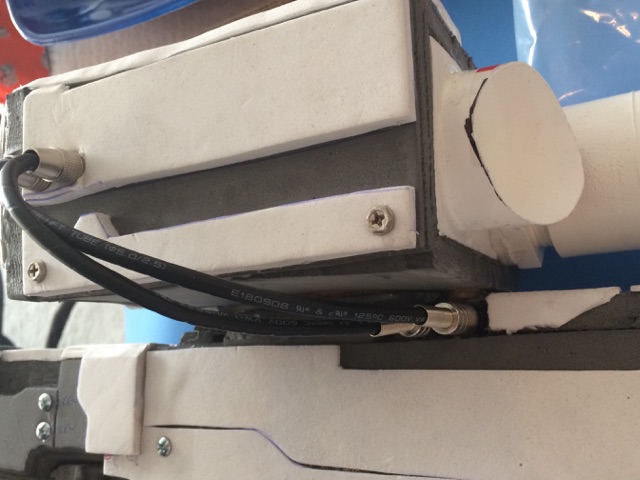
LENSES
To make the lenses, I got some $2 sunglasses from the dime store, and ground them down with the Dremel until they fit. Lots of trial and error.

PVA SEALING AND PLASTI-DIP COATING
Like an EVA project, the rifle needed dealing and coating with Plasti-Dip. I coated with PVA, let dry overnight, then did a coat of Plasti-Dip. I left the body and scope disassembled until later, so I could get into the cracks in between both of them.
PVA:
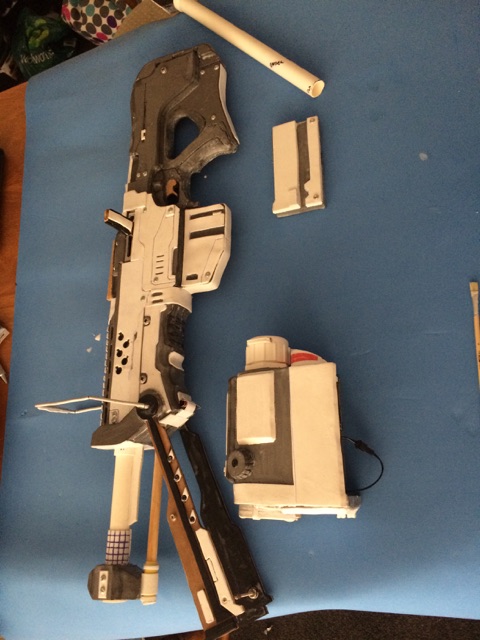
Plasti-Dip:
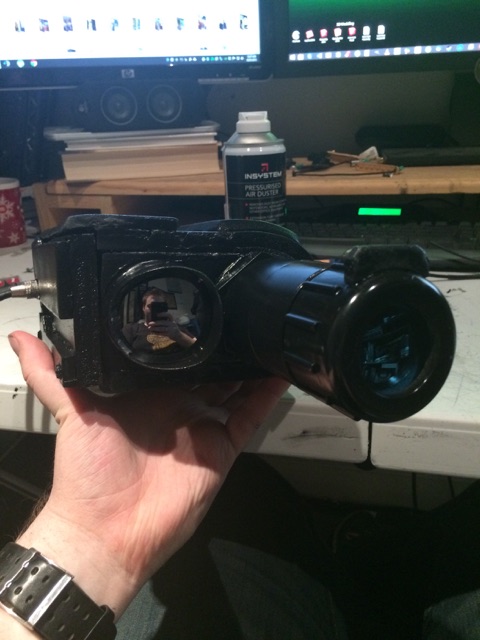
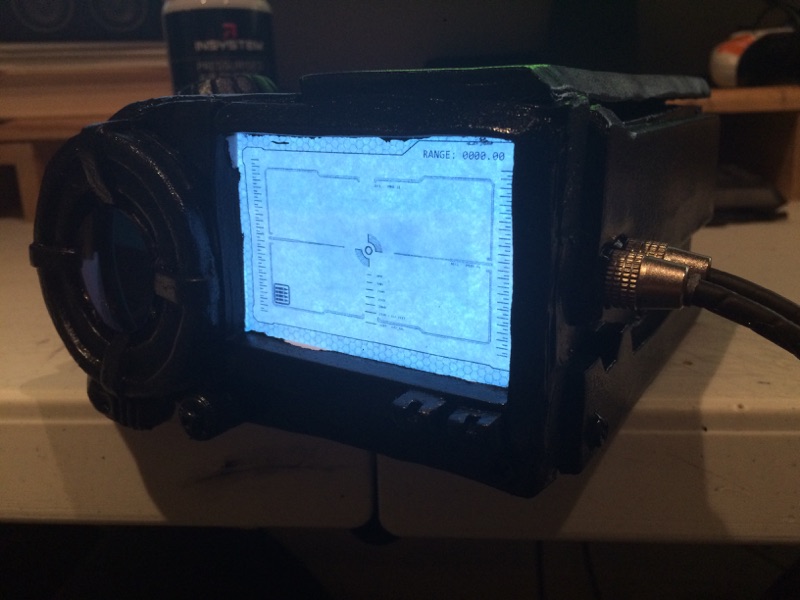
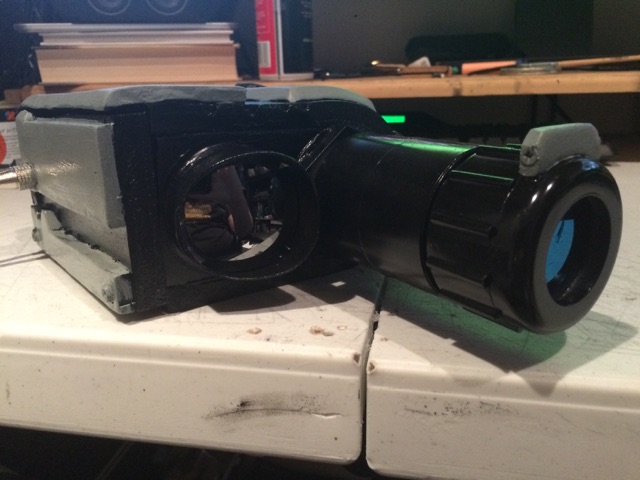
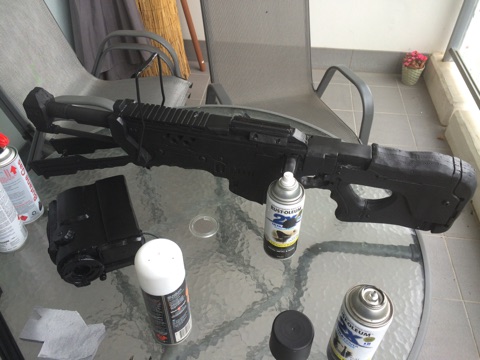
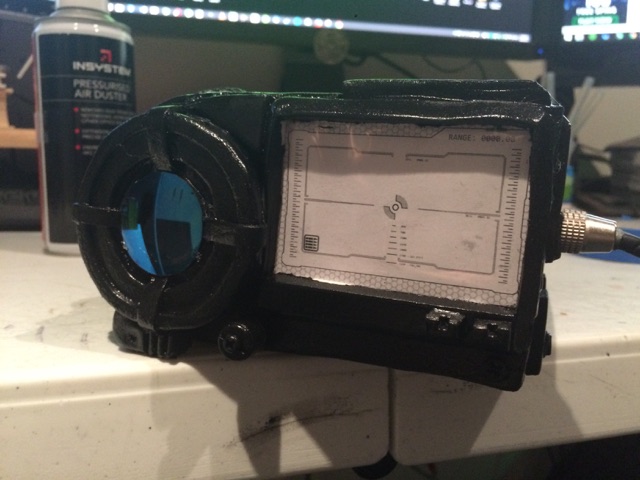
PAINTING
I gave a base coat in matte black, and detailed in grey. I also washed the grey sections in black ink, to make it a bit more weathered.
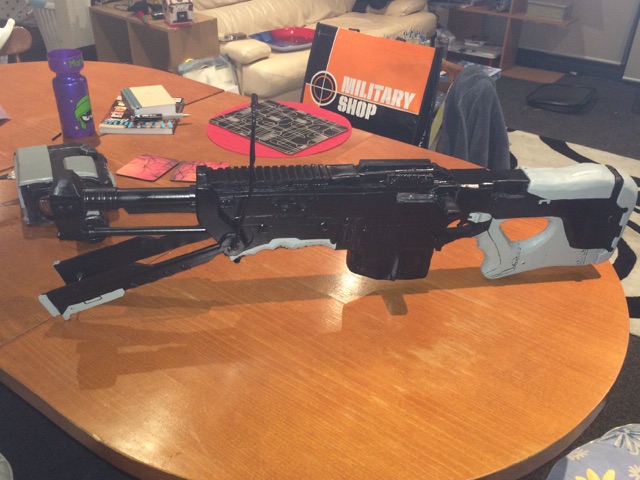
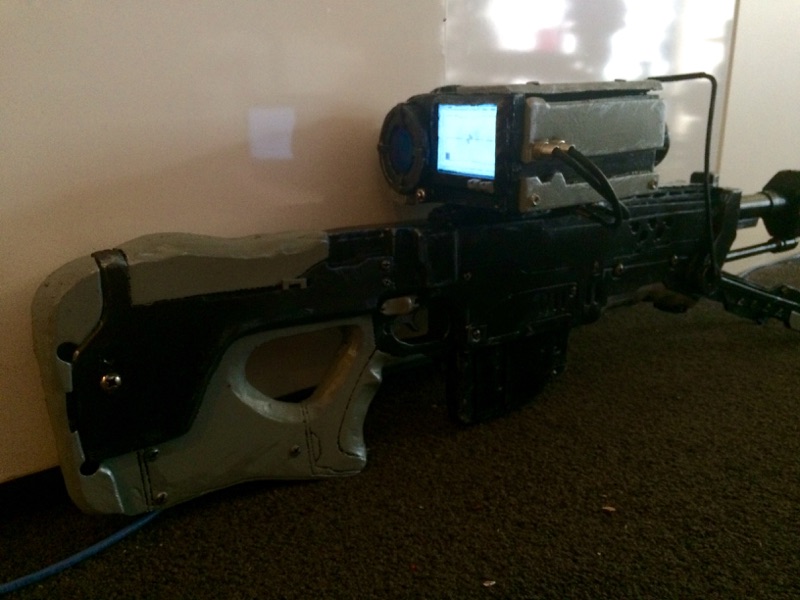
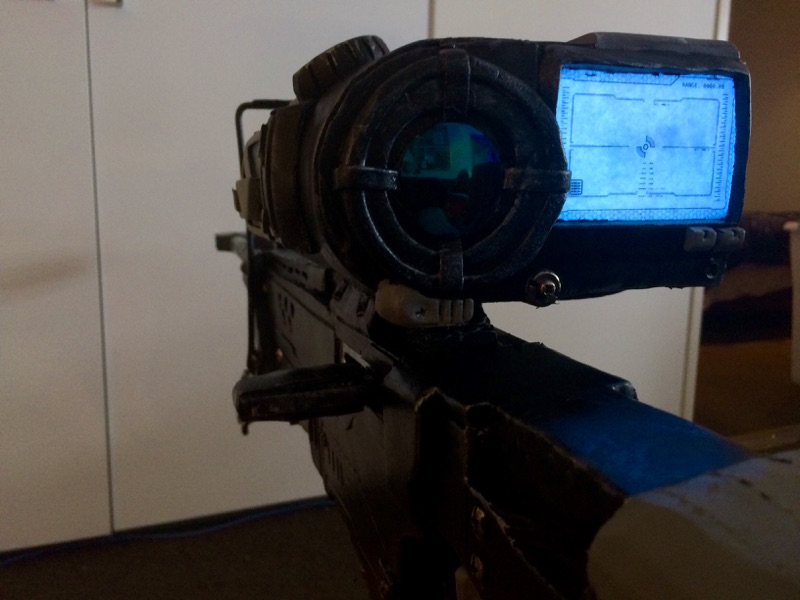
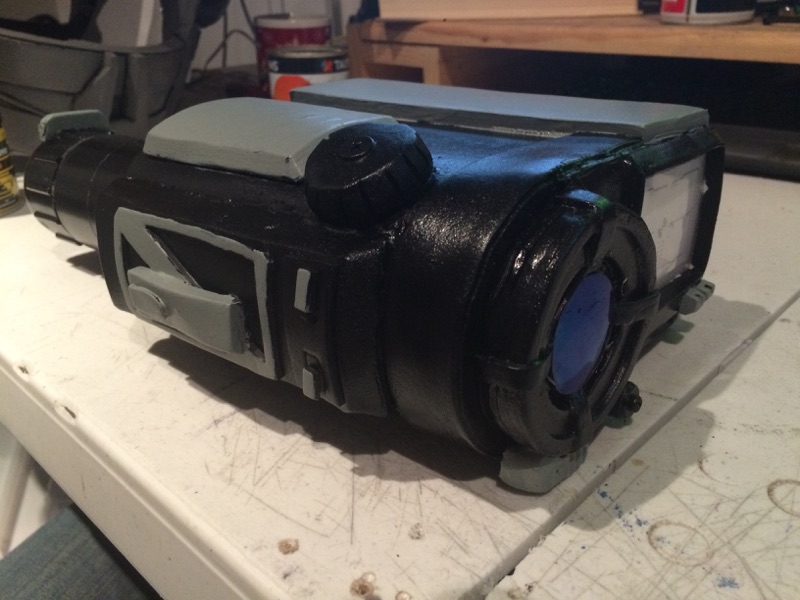

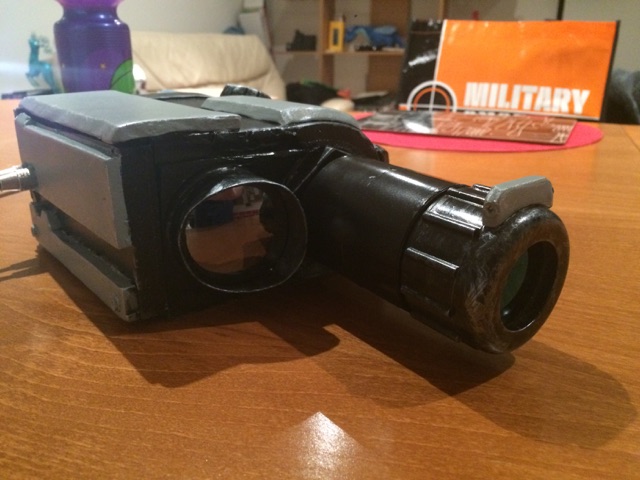
More to follow in Part 7.
- - - Updated - - -
After the base coats, I weathered using a silver paint pen and some metallic grey paint. I also used a wire brush to clean the Plasti-Dip and paint off some of the screws, for some metallic details. I inserted some springs into the cocking handle, so it would spring back. Lastly, I glued the scope onto the rifle - it was finally one piece.

FINAL RESULT
After all was said and done, here was the result.
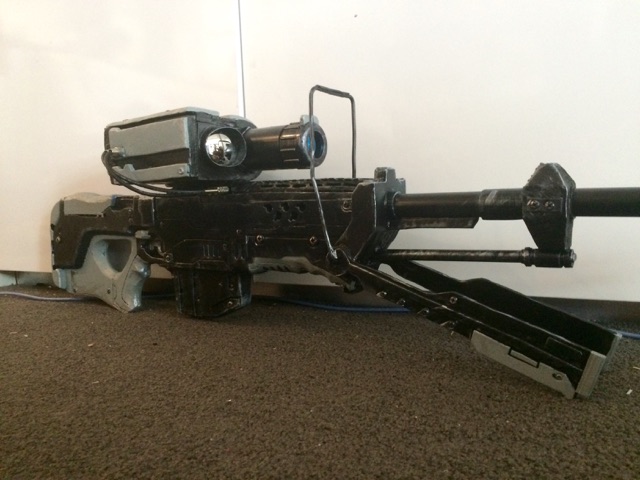

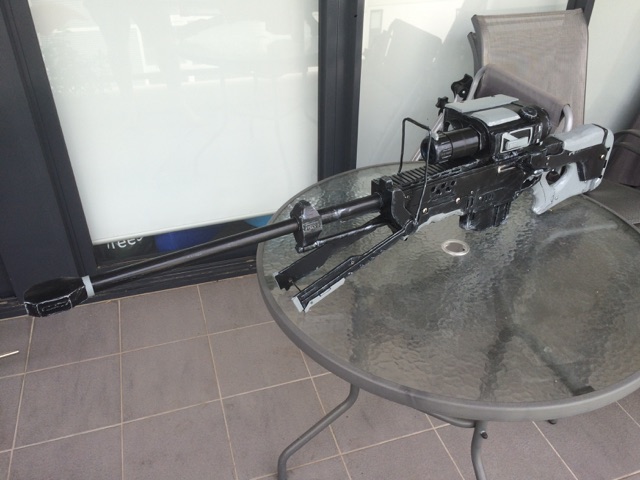
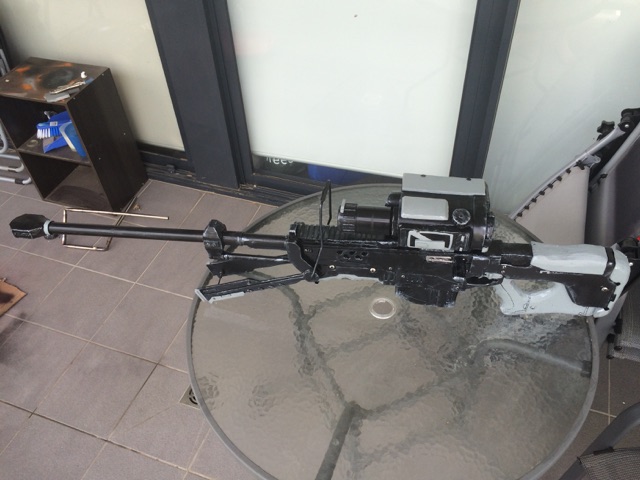
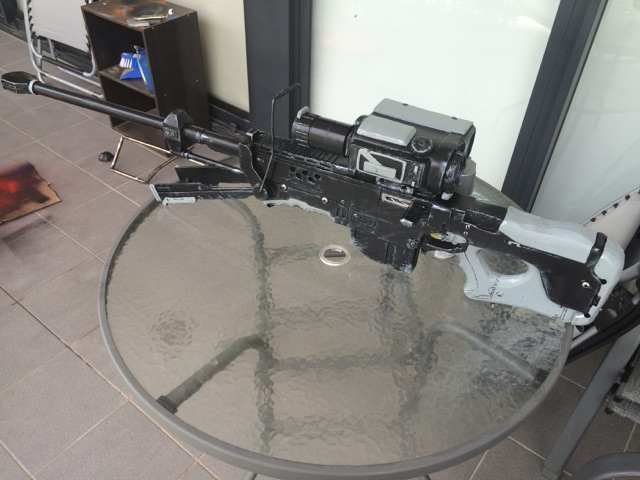
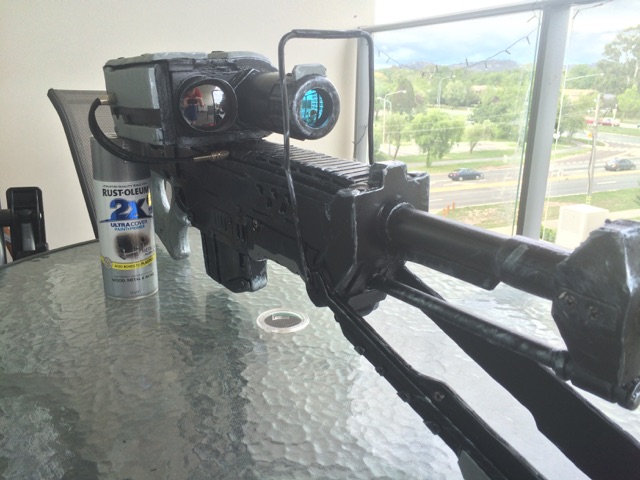
This is the scale next to the DMR:
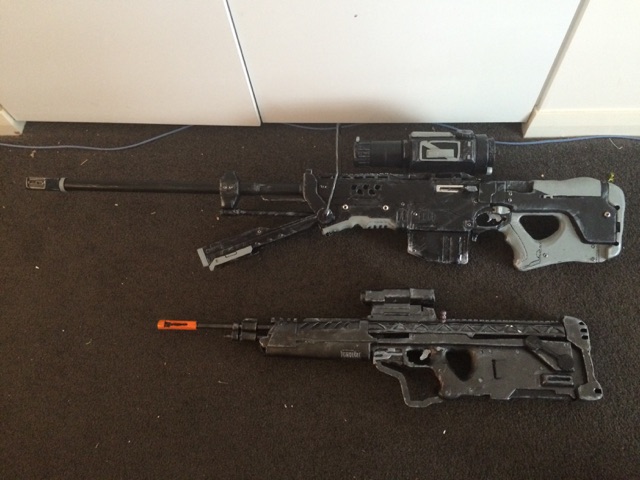
The build was commenced on January 2nd 2015, and ready by 11th January - just over a week of work.
The remaining time between then and CanCon on January 25th was just small adjustments, that could be done at any time.
MOUNTING
As per my previous build log, I mount my DMR to my back using a Jacket Bracket, a magnet mount used for attaching equipment to clothing. I have two high-strength magnets in my shoulder, and a metal plate on the DMR, which I use to attach it with one arm.
I first attempted to use the lighter, two-dot Jacket Bracket on the Sniper as well, by attaching the metal plate to the rifle with Aryldite.

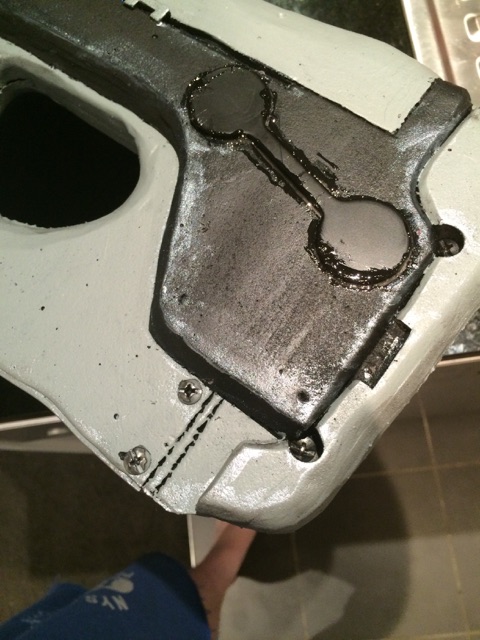
However, I found that the rifle tilted and fell off if I moved around - it was simply too heavy. So, I sought to add a second Jacket Bracket to my shoulder, and another plate to the rifle.
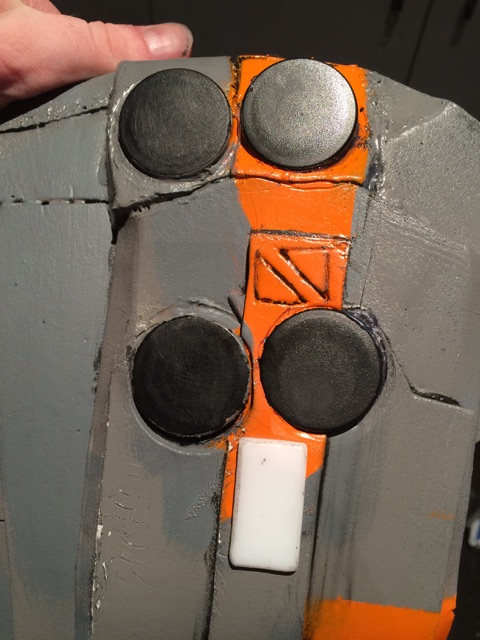
The result was great - I could, with some effort, attach the Sniper rifle to my back and walk around with it on, with no support.
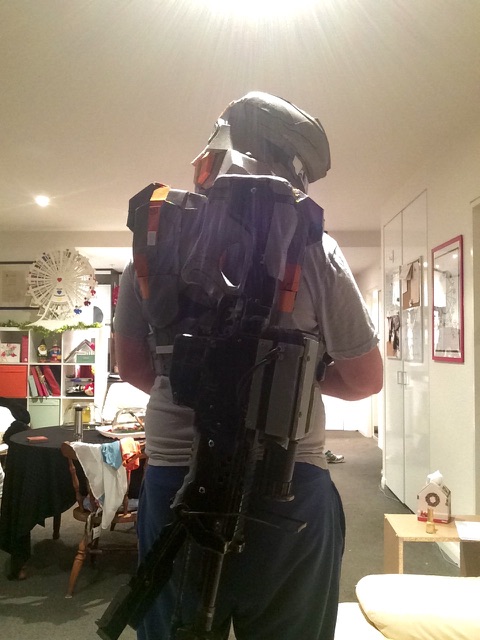


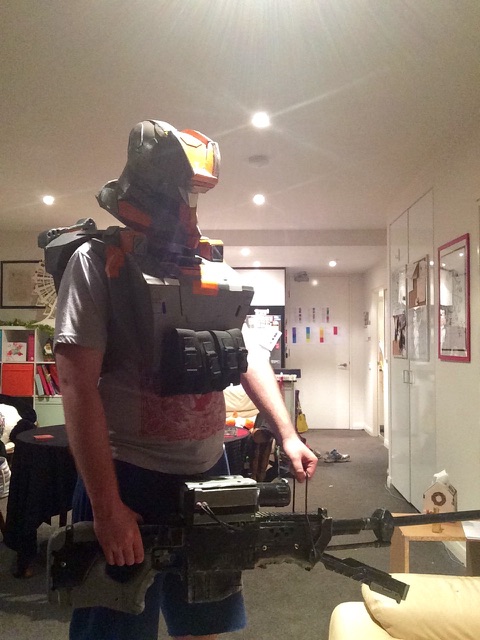
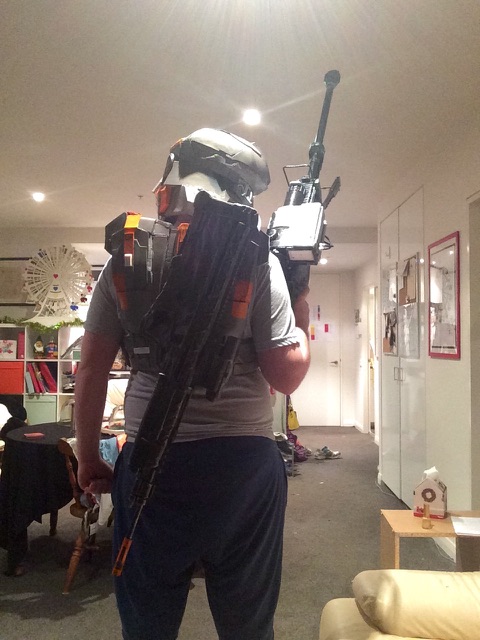
MAKING THE MAGAZINE REMOVEABLE
I cut into the foam after it was all finished, in some downtime between then and CanCon, to make the magazine removable with magnets. I glued the plastic back of a blue notebook to the sides, to make it slide easier.
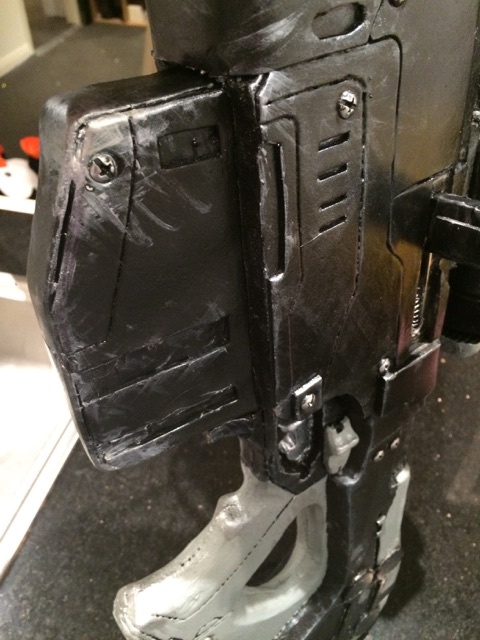
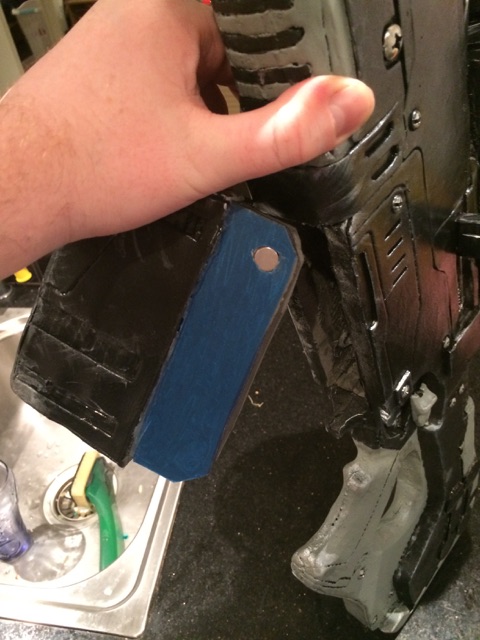
And with that, I was all done! Time to go to CanCon!
More to follow in Part 8 the final part.
- - - Updated - - -
Part 8 - Final Part
----------------------------
CANCON 2015 + FEEDBACK
The Australia Day weekend was CanCon in Canberra, ACT - a small, local convention with no costume rules and a smaller turnout. It was a great test of the rifle, and I learnt some important lessons that helped make adjustments later on.
- I learned in the first 5 minutes that the not-insignificant weight of the rifle was 90% on my left hand, which was bent back at an odd angle - my left wrist was aching after 10 minutes, dying after the first day. I settled afterwards on carrying the rifle more "up in the air" solely on my right hand - easier to get through crowds and easier to handle. I also want to put a sling clip into the front hand grip, so I can attach it to my neck for long periods.
- The barrel was longer than I thought, but once I got used to it, it was very manageable.
- With practice, I would switch the DMR and the Sniper on by back in around 30 seconds. The alignment of the magnets on the Sniper is much harder, but practice helps.
- The EL panel helped significantly, and lasted 3 entire days.
- With the reflective eyepiece on the scope and my reflective visor, I couldn't see through it at all. Oh well, at least it was a cool idea and something notable for people to see if they held it.
- Having a second weapon was a kick for kids wanting photos - I often let one kid hold the Sniper, one the DMR and I held the knife. Great times.
- The DMR also needed a new flash suppressor, the cardboard one wasn't cutting it.
- The main 'wow' factor came from the simple action of removing and replacing the magazine and cocking the handle - these simple physical movements on the rifle made it seem all too real.
- Many people commented on how realistic it looked from afar, and how soft it was when they held it.
- An admirer suggested that instead of an orange barrel (which I was just going to paint for Supanova), I could make an orange EVA foam plug for the end that I could insert and remove like a cork - no permanent colouring of the barrel, and a soft pad I can rest the rifle on when upside-down.
- Lastly, the rifle with the barrel removed (at under a meter) could be easily taken for a complete rifle (i.e., it didn't obviously look incomplete) meaning it could be brought into a con with a 1-Meter rule inspection and assembled afterwards pretty easily.
These are some pics from the day:
Test Pics at home before the Con:
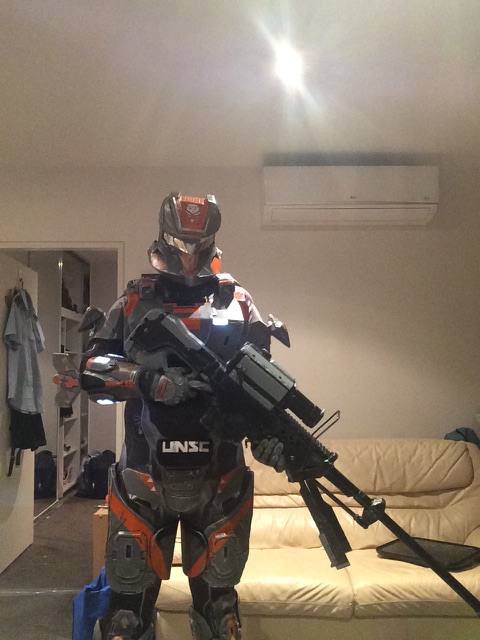
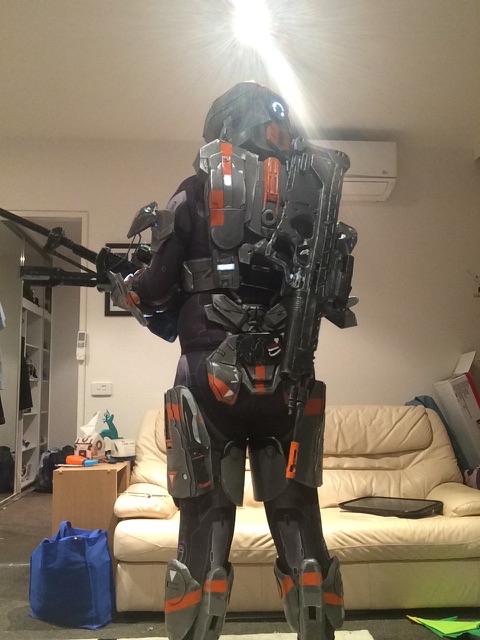
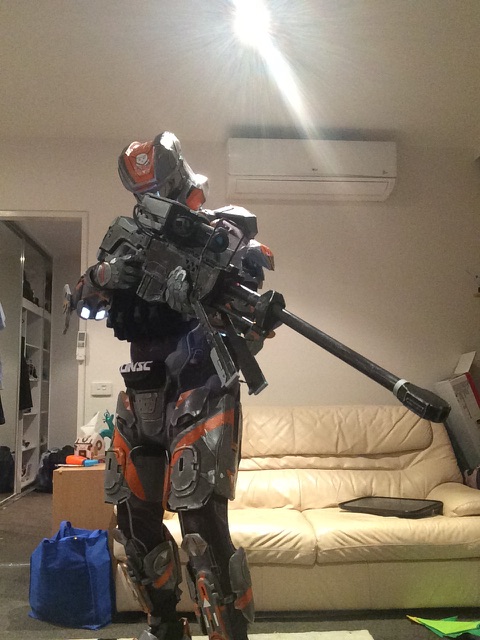
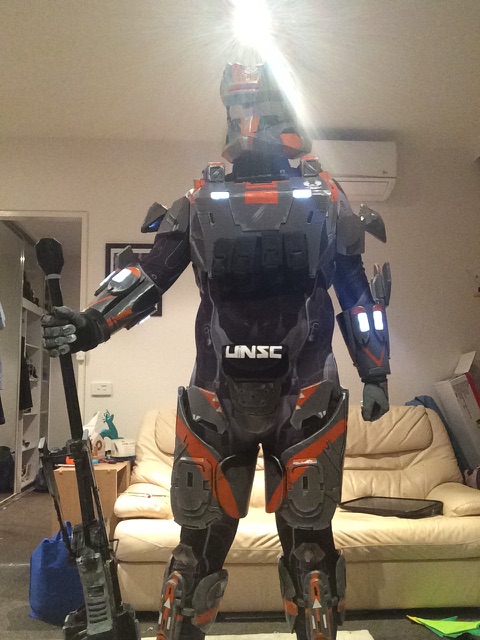
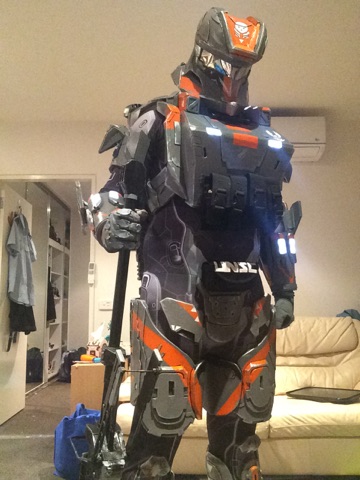
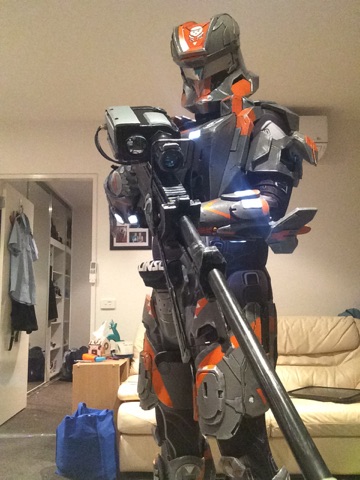
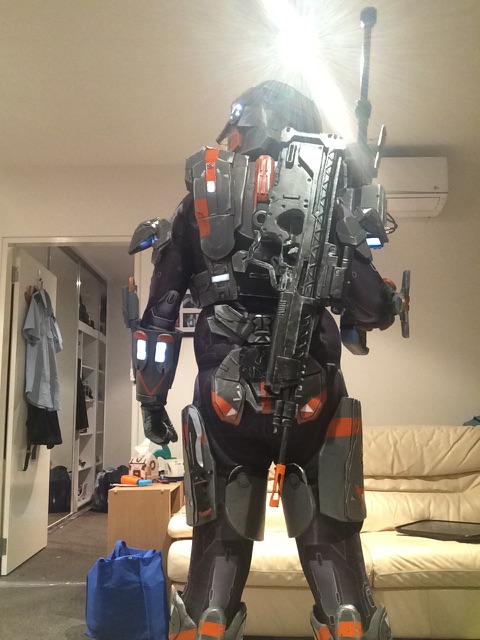
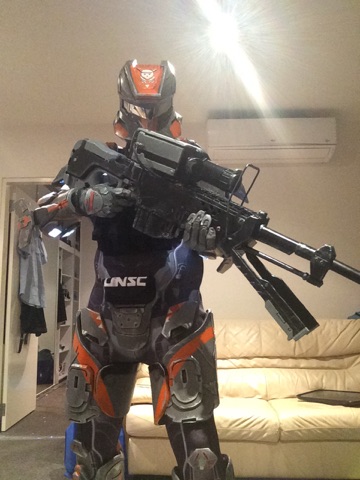
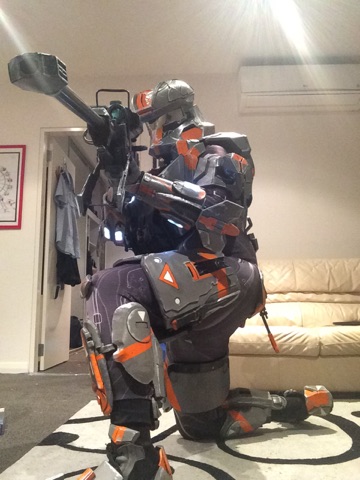

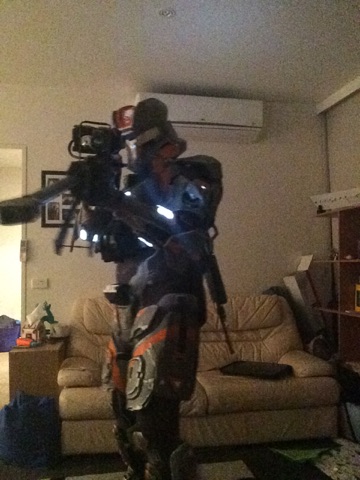

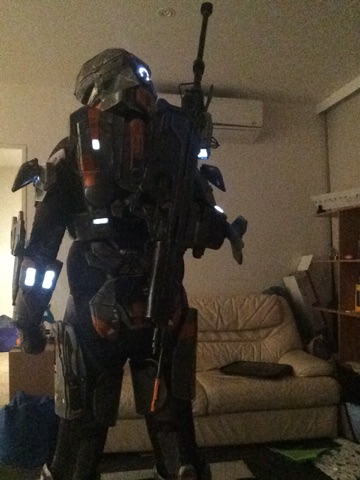
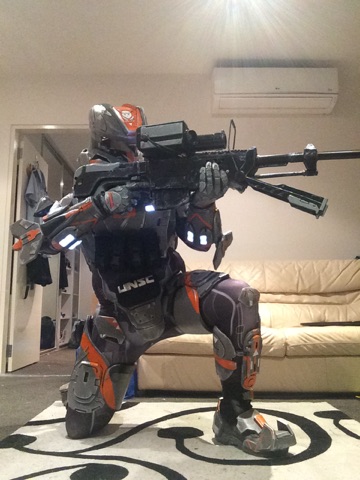
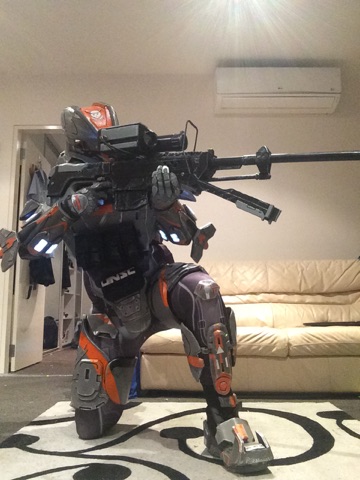
Pics at CanCon:
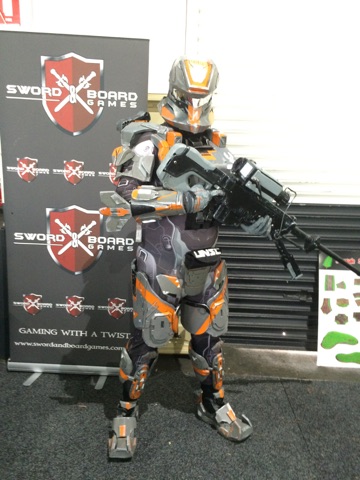
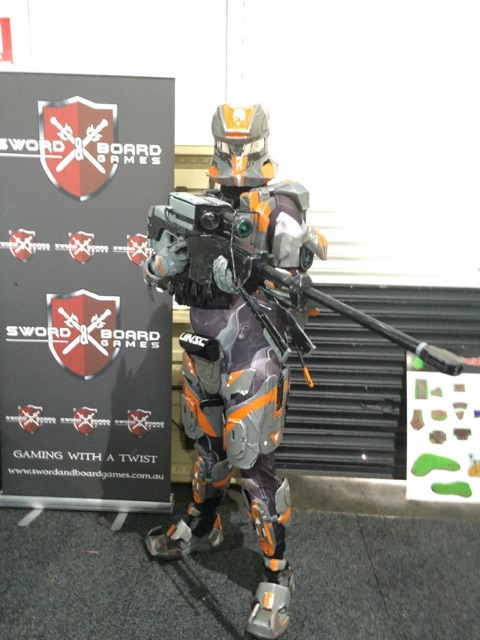
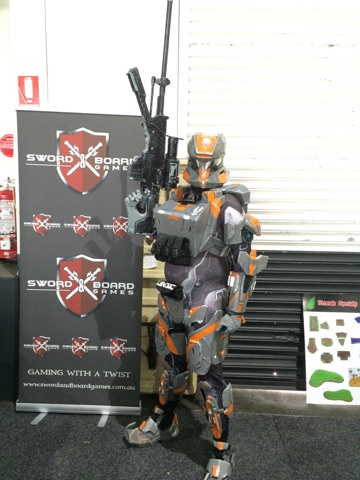
Yay!
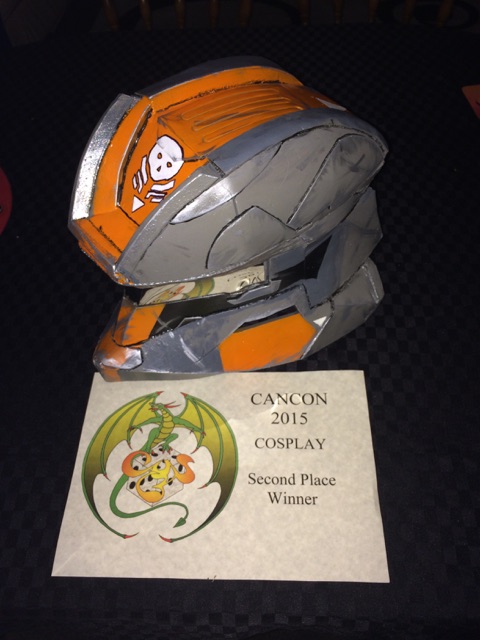
Got featured on ABC News too!
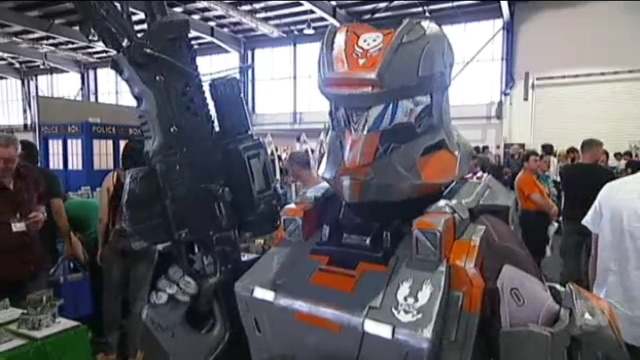
Got some professional photos too:
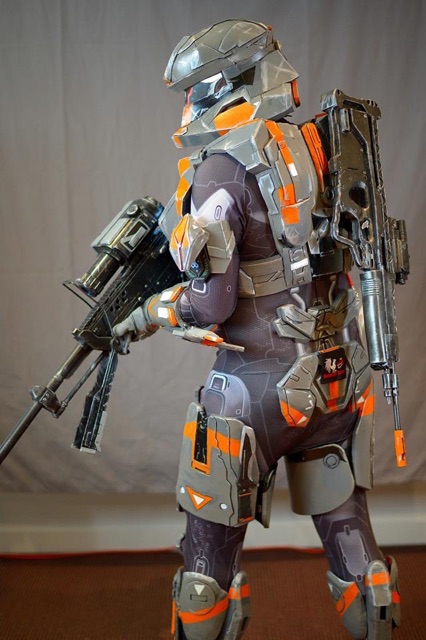
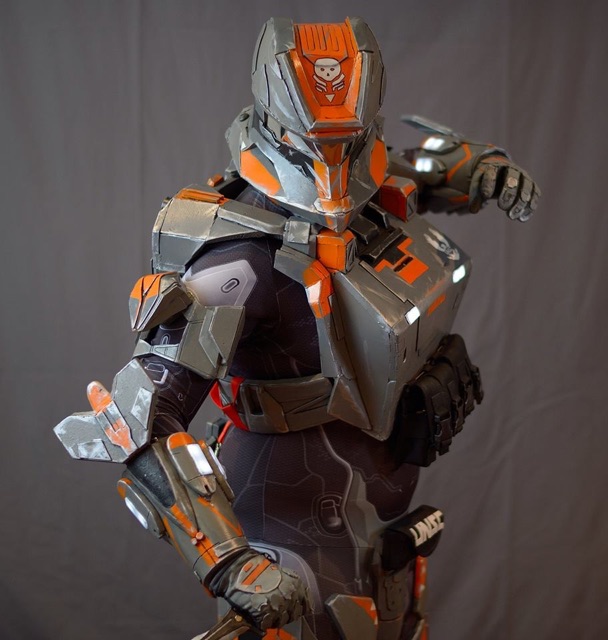
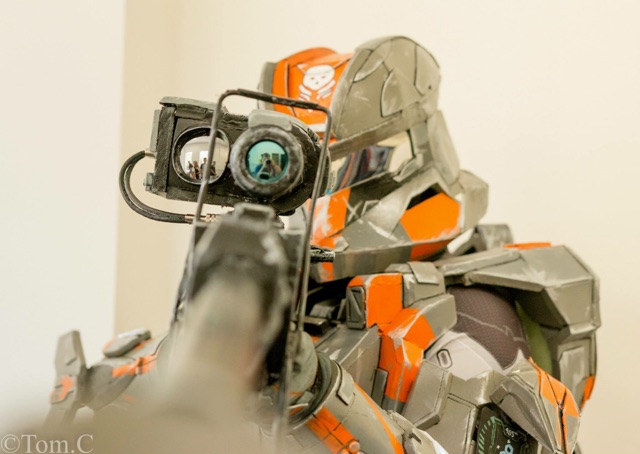
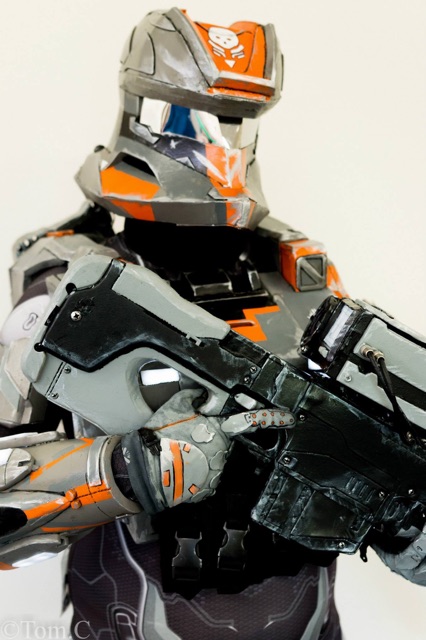
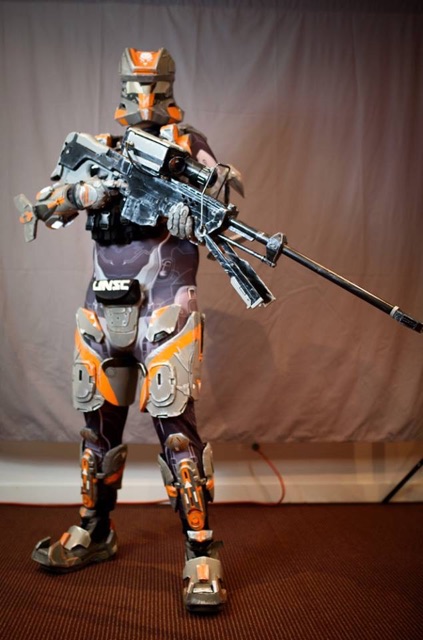
CONCLUSION
The build was commenced on January 2nd 2015, and ready by 11th January 2015 - just over a week of work. Compared to the DMR, which was 2 days, it seemed like an ordeal - but in hindsight it came together pretty quickly! I have some future ideas of what additions to make, but i'll cover those in a future post.
As only my second foam Halo weapon, I learned a lot, but at the same time, it was reasonably straight forward - with this same, or similar, methods, it's a simple way for anyone to make their own replica of a movie/game prop.
Let me know your feedback and comments below, I'll update soon with any further progress or changes!
Due to the 405th.com limit of 25 images per post, this will be posted in multiple parts, as I migrate all the pictures across.
-----------------------------------------------------------------------------------------------------------------------------------------------------------------------------
This project is a follow-up to the Halo 4 Spartan armour I made a few months back from EVA foam, to make Felix from Red vs Blue Seasons 11 and 12. I made it in two months, for PAX AUS '14.
To match the armour, I made a Halo 4 DMR to match, also in EVA foam. A little small, but light and only took a day. I made it back-mounted, with high-strength magnets, which turned out to be a hit at PAX, especially with the other Spartans!
To prepare for CanCon here in Canberra on Jan 25/26, I made a Halo 4 Sniper Rifle as another weapon to match the character.
The whole project took just over a week, start to finish. I'll explain my process and show my progress here, to demonstrate how I did it.
GOALS
I started with a few goals in mind:
- the barrel had to be removable for transport
- the without-barrel length had to be under a meter
- the whole thing had to be durable enough to take to a con
These extra goals were a nicety, if things worked out ok:
- as far as possible, it had to be made from EVA Foam
- it had to have a sliding bolt-action
- the magazine had to be removable
- the scope had to be able to be looked through
Initial research was on what the rifle looked like, in comparison with the Halo 1/2/3/Reach versions, and starting to think about layers.
INSPIRATION
During research, I found this guy, who made a H4 Sniper from MDF / wood - and it was badass:
props.punishedpixels.com/2013/05/24/halo-4-sniper-rifl...
Layering of the MDF wood:
If I could be even half as good as this guy, I would be able to make an AWESOME prop. This guide became my reference for two things: what layers to do (as MDF layers similar to foam), and how the in-game look could translate to real life.
BLUEPRINTING
As with the DMR, I needed a blueprint image to reference the rifle from - I sourced a blueprint image off Google, that I could use as a template. I had to do some in-depth research, as there were many mis-labelled blueprints - many people had images of the Halo Reach sniper rifle (arguably better looking) listed as the Hal 4 variant, so I had to get the reference image straight from the Wiki, and compare it to every blueprint I could find. Eventually I settled on this image:
This image was the only one I found that was: black and white, a large size, the correct version and freely available (not watermarked).
I also used a few other images for reference:
I started by loading the rifle into GIMP, to cut into equal segments. This cutting is to print onto A4 paper.
The size of the splits is dependant on your body size. Given the points above, I wanted the main body to be under a meter, so I initially split the image into 20% segments. This ended up being too small, only about 75cm long. SO, I split it into 15% segments, and it ended up a much larger size, 89cm without the barrel. Another good test was printing out just the handgrip page - once I cut it out, it was immediately clear that the 20% segments were way too small for my hand to fit into the grip. 15% segments were much more comfortable, so I went with that.
To do this, do the following:
- load the image into GIMP
- select the Square Selection tool and select an area on the image - any area, it doesn’t matter
- use the tool options to set the current selection to the following figures. Ensure to select "%" from the drop-down box next to Position and Size, to ensue the figures are correct:
Position: 0.00 , 0.00
Size: 15.00 , 100.00
-At the top, select Image -> Crop to Selection
- Go to File -> Export As... And export the image as a PNG, name it like "1" or something
- Use CTRL+Z or Apple+Z to undo until you get back to the selection with the full image.
What this does is manually edit the selection area to start at 0,0 (very top-left), and select 15% of the width, 100% of the height. Then, it crops the image to that size, and saves it.
For the next section, repeat the above steps, except use the following figures:
Position: 15.00, 0.00
Size: 15.00, 100.00
This selects the same size area, but the next 15% of the image along. Export, undo changes, repeat.
After the images had been split, I simply selected all pictures and printed each page at A4 size. As each one was the same size, they were all scaled the same and lined up with each other.
Next, I cut out every image, cutting off the barrel, trigger and scope, and cutting out the hole in the stock and trigger guard. I then taped them together, so I had a full template of one half of the body.
(pictured below with the DMR next to it for scale)
Aaaaaaaand then I repeated the entire process for the other side of the rifle - I reversed the individual images, rather than reversing the original and cropping it again*.
*Note: Like any rifle, both sides differ slightly - these is an opening on the left-hand side of the rifle for the cocking handle to slide forward and back, and a breach oh the right hand side (not pictured on the blueprint) for the bullet casings to eject. I added these openings after cutting the stock 'blank' out.
'BLANK' CUTTING
I traced each body template onto the EVA foam, so I had two - one for each side. I've edited these images to have high contrast, so the lines are a bit more visible.
Then, I cut both sides out. Don't worry if the sides don't exactly match up, the sculpting/sanding will even them up with each other once they are joined together.
THE MAGAZINE
You may note that the magazine here is part of the body template. Something I noticed later in the process is that the magazine looked massively thick, and I realised why - I was raising the flat template to be three-dimensional over the entire thing, but not taking into account that the magazine is much thinner than the rest of the rifle. Take note of this if you do it yourself - it's easy enough to fix by removing the outer layer of foam, but better to do it in the first instance than later on. If you're following along, see if you can pick where I realised this, and thinned the magazine out ;-)
--------
More to follow in Part 2.
- - - Updated - - -
PART 2
-------------
BRACING AND REINFORCEMENT
As with any foam template, it's floppy and flexible when first cut out - not at all suitable for a prop or weapon, as it won't have the core strength to hold the rest of the rifle up. So, I use wooden dowel to stiffen the body of the rifle.
I started by drawing a line in sharpie on the underside of each side, to determine where the reinforcing dowel should go. To decide on this, you should try and make it go as long as possible along the rifle - remember, where you have gaps in the dowel, the foam will bend.
In the picture below, you will note that there is no reinforcing dowel that extends up from the handle into the rest of the body. This was a mistake I only noticed after I finished the entire thing and picked it up with one hand - when holding the rifle on the right (master) hand, when 100% of the weight of the rifle (including barrel and scope) is being held on that small bridging section between the trigger opening and the thumb hole in the centre of the body, it flexes a fair amount around that point. To fix this mistake, all that would have been required is the dowel in the handle to be extended up to meet the other one that runs down the entire length.
It's a bit of a physics puzzle, but it's only a huge issue for very heavy rifles - if you try to think about where the weight will be when it's finished, you can estimate it reasonably practical - and if it doesn't work out right, the easy solution is to always hold it in two hands or not by the flexible points!
Continuing on, once you've decided where the dowel goes, cut 45 degree cuts along the line, to leave channels for the dowel to fit. At this stage, I glue the dowel into the side of the panel, rather than try to guess where the channel should go on the other side. Once the dowel is glued in, use a paint marker, paint or other wet substance to paint the uppermost part of the dowel (the side that will touch the other side of the body blank), line up the opposite of the blank as if you were putting it together, and press down. This will leave a mark on the inside of the opposing side of foam, telling you exactly where you should cut the channel for the dowel on the opposite side.
If you want your rifle to have some "bulge" or thickness, this isn't hugely necessary to carve out channels for the dowel - but it's more necessary the thicker the dowel you use to strengthen it.
Once the grooves are cut on both sides, use liberal amounts of glue on the inside of one of the sides, and glue it to the other side, lining the dowel channels up. If the glue is decently hot, you can slide the sides against each other, finding the channels with the dowel on the other side and feeling it slide into the grooves. It's more important to gave the dowel fall into the matching groove than the edges of the entire body matching up - the adhesion between the two halves is the building block and basis of strength for the entire rifle, so it's important to ensure the dowels have good adhesion to each side.
Wow - that's a lot of effort to stick two pieces of foam together! But trust me, now comes the fun part :-D
SCULPTING THE BLANK
Now the sides were glued together, I marked the edges where the square edges need to be rounded. For this rifle, I rounded the handgrip, the thumb hole in the back of the stock, the trigger hole and basic bevelling around the edges where nothing would be glued on top (bottom of stock, magazine etc). The front hand grip had to wait until all the panels were on the front of the stock.
I used a Dremel or similar rotary tool (i'll refer to it as a Dremel here, as it's what I use and it's pretty common) to sculpt the above sections and to make each side line up with the other. Some areas were significantly out of line, so a lot of sanding was necessary.
OUTER PANEL SCULPTING
Starting from the back, I cut the blueprint up part by part into sections that needed to be added on as extra layers on top of the base two layers. For each part, I traced the paper onto the foam, cut it out, and reversed that piece onto more foam and traced/cut a reverse for the other side. The first part was the back upper stock:
It's much easier to sculpt/bevel each piece while it's off the rifle, so I sculpted a lot of parts before they were glued to the rifle, rather than after.
LINE DETAILING
I used a hotknife to cut the foam, but it also had another use: fine line detailing. Using the blunt side of the Xacto blade in the hotknife, I ran it over pen lines I drew onto the body to create recessed lines that weren't cuts, but fine enough to look detailed.
BARREL
The barrel, needed to be removable, so the easiest way was using plumbing pipes. I picked an appropriate diameter pipe of a meter length and a connector, and cut it to it was extended into the body as far as it extended out from the end (50% in, 50% out). This part needed to be extremely stable, as the barrel extends a long way and needed to have reinforcement in case of knocks and able to hold up the rest of the barrel without bowing or bending.
I decided to make the 'join' the combined section out the front of the rifle where the gas cylinder (small, extra barrel) meets the main barrel, so I cut the pipe to fit so the join was there. I then cut a large section of the body out, and glued the pipe on top with, I kid you not, two full sticks of hot glue.
I also used some dowel to make the gas cylinder, and cut a slot for that and glued it into place.
From there, I cut the outer panel for the rest of the body, and stuck it over the body centre to hide the pipe and the gas cylinder dowel.
I then sculpted the front hand grip, and continued adding panels to the rest of the body:
THIN PANEL DETAILING
As the larger parts were all close together and didn't need large parts for detail, I did the rest of the sculpting for the body in thin self-adhesive craft foam, with real screws for a detail or realism.
COCKING HANDLE - PART 1
For this rifle, I wanted a real, working cocking handle that actioned like a real rifle. I achieved this using a D-Bolt, a door latch and some springs.
I cut a recess to match the latch in the body, and covered the back of the recess with aluminium foil tape, so the action could slide smoothly and easily.
I then glued the latch into place, leaving the d-bold to slide freely. I would continue this later.
MORE FINE DETAILING
Contined with the detailing for the front. I used a pen body for the sling latch connector at the front.
More to follow in Part 3.
- - - Updated - - -
Part 4
------------------------
GAS CYLENDER, CONNECTOR AND FRONT OF BARREL
I used a highlighter lid with some foam additions to make the end of the gas cylender.
I also used some foam offcuts to make a surround for the connecting sleeve, and sculpted that to fit.
Eventually, it was all connected together - the body was pretty much done. And best of all - JUST under a meter long.
The rest of the pipe needed a flash suppressor, so I used some foam blocks cut to shape, with the plastic back of a notebook to do the top and bottom and the barrel hole.
So the basic sculpting was all finished, with the assembled length totalling around 140cm:
....and it left a hell of a mess.
TRIGGER
I cut the end of a wooden spatula and sanded it to shape with the Dremel, to make a trigger.
I then glued it into place:
COCKING HANDLE - PART 2
I used two ends of a ruler with a bolt through the middle to connect the rest of the spatula handle to the D-Bolt, to extend the cocking handle.
It's worth noting that I cut this down significantly later on, as, while it's the length it is in-game, it also sticks (a) into my chest with the chestplate on, and (b) into my back when wearing it over my shoulder.
More to come in Part 5.
- - - Updated - - -
Part 5
----------------------
SCOPE
The (first) scope I made was based on the idea of wanting to be able to actually look through it. So, I decided to base it around an *actual* scope, a $20 metal airsoft scope I bought online.
To emulate the actual scope barrel, I used some plumbing parts, with a sanded-down sunglasses lens from The Reject Shop:
The challenge from here was the shape of the scope - it needed to have one round side, and one flat side. So, I glued the round scope front to the airsoft scope, some smaller pieces to the eyepiece, wrapped some craft foam around to make it all the same width, and heated/wrapped a piece of EVA foam around it to form the body.
From here, I cut a rectangle of EVA and glued in some earth magnets, to make a square side that was detachable.
The front panel was easy, just had to leave space for the two scope lenses. The back is where the difficulty lied. I drew out the details of what I was going to craft out first, to size it up first.
I crafted the eyepiece from layers of craft foam.
The screen was a challenge. I ended up settling on an electroluminescent panel with a black and white scope overlay over the top, so when the panel was on, it would shine through.
[NOTE: I've since changed out this scope for a better scope - update to come!]
After getting the screen size correct, I then set to adding the rest of the detail in EVA, screws and craft foam, until the overall shape complete. I used a detergent bottle as the holder for the other (left) lens. Overall it turned out ok, but if I did it again, I would do a few things differently.
Inside the scope was the driver box for the EL panel, which could be removed to turn it off and on.
Best of all, the green dot on the scope could still be seen!
I sat the scope on the rifle to get an idea of the overall scale of the rifle. It was much heavier than I thought, but the scale looked right. I also tried it with my helmet and chest, to see the scale with my body.
BIPOD AND CARRY BAR
I was initially thinking of making the bipod legs from plastic or foam, but they were too bendy. I went with some spare MDF, which was stiffer and I had spare. I cut them out and sanded them, added detail with craft foam and screws. I found that they wouldn't support the full weight by themselves, but by affixing a joining screw in between the end of the legs, they stood a much better chance of standing up.
More to follow in Part 6.
- - - Updated - - -
Part 6
--------------------
I also used some thicker armature wire to make the carry bar in front of the scope.
The point where the bipod legs and the bar met the body of the rifle was just foam, which I drilled out to make an area for the bar to go into. The area was under too much strain to use standard hot glue, so I filled and surrounded the area with Aryldite (2-part epoxy glue) to make it solid. Due to the natural "give" in the foam anchoring the legs, it doesn't stay upright on the legs for very long before it bends over.
LAST GEOMETRY CHANGES
No pictures, but you will notice in the final geometry pics that the magazine is a lot thinner. This is due to me, as mentioned above, thinning down the magazine to make it more realistic.
I also decided not to put an ejection port in until I got a prop round to put in the gap - give some up-close realism to the rifle. I later decided this wasn't a good idea, as this may have made the prop more difficult to take into cons. It's still an idea, but one I probably won't go into.
Lastly, I shortened the cocking handle by 3-4 cm, for comfort.
FINALISED BODY/SCOPE PICS
These pics are the final draft of the entire rifle, with the scope propped up on a paint can. I was very pleased with how it turned out, and the details looked great!
SCOPE CHANGES
While I was PVA sealing the rifle, I made two changes to the scope.
Firstly, I inserted a plumbing extended into the scope, to make it more like the actual scope. This was heavy, but necessary.
I also decided to make the cable seen in the reference pic. I got an old iPhone cable and wrapped it in some cable wrap, then covered that in shrinkwrap to make a textured, thin cable.
I glued some RCA connectors I got from JayCar electronics for $0.10 on each end, mostly because I liked the look of the ends.
Finally, I glued an RCA wall socket plug into the rifle at the section where I connected the scope to the body.
Overall, the cable effect was more pronounced in the real life than the pic, but looked cool nonetheless.
LENSES
To make the lenses, I got some $2 sunglasses from the dime store, and ground them down with the Dremel until they fit. Lots of trial and error.
PVA SEALING AND PLASTI-DIP COATING
Like an EVA project, the rifle needed dealing and coating with Plasti-Dip. I coated with PVA, let dry overnight, then did a coat of Plasti-Dip. I left the body and scope disassembled until later, so I could get into the cracks in between both of them.
PVA:
Plasti-Dip:
PAINTING
I gave a base coat in matte black, and detailed in grey. I also washed the grey sections in black ink, to make it a bit more weathered.
More to follow in Part 7.
- - - Updated - - -
After the base coats, I weathered using a silver paint pen and some metallic grey paint. I also used a wire brush to clean the Plasti-Dip and paint off some of the screws, for some metallic details. I inserted some springs into the cocking handle, so it would spring back. Lastly, I glued the scope onto the rifle - it was finally one piece.
FINAL RESULT
After all was said and done, here was the result.
This is the scale next to the DMR:
The build was commenced on January 2nd 2015, and ready by 11th January - just over a week of work.
The remaining time between then and CanCon on January 25th was just small adjustments, that could be done at any time.
MOUNTING
As per my previous build log, I mount my DMR to my back using a Jacket Bracket, a magnet mount used for attaching equipment to clothing. I have two high-strength magnets in my shoulder, and a metal plate on the DMR, which I use to attach it with one arm.
I first attempted to use the lighter, two-dot Jacket Bracket on the Sniper as well, by attaching the metal plate to the rifle with Aryldite.
However, I found that the rifle tilted and fell off if I moved around - it was simply too heavy. So, I sought to add a second Jacket Bracket to my shoulder, and another plate to the rifle.
The result was great - I could, with some effort, attach the Sniper rifle to my back and walk around with it on, with no support.
MAKING THE MAGAZINE REMOVEABLE
I cut into the foam after it was all finished, in some downtime between then and CanCon, to make the magazine removable with magnets. I glued the plastic back of a blue notebook to the sides, to make it slide easier.
And with that, I was all done! Time to go to CanCon!
More to follow in Part 8 the final part.
- - - Updated - - -
Part 8 - Final Part
----------------------------
CANCON 2015 + FEEDBACK
The Australia Day weekend was CanCon in Canberra, ACT - a small, local convention with no costume rules and a smaller turnout. It was a great test of the rifle, and I learnt some important lessons that helped make adjustments later on.
- I learned in the first 5 minutes that the not-insignificant weight of the rifle was 90% on my left hand, which was bent back at an odd angle - my left wrist was aching after 10 minutes, dying after the first day. I settled afterwards on carrying the rifle more "up in the air" solely on my right hand - easier to get through crowds and easier to handle. I also want to put a sling clip into the front hand grip, so I can attach it to my neck for long periods.
- The barrel was longer than I thought, but once I got used to it, it was very manageable.
- With practice, I would switch the DMR and the Sniper on by back in around 30 seconds. The alignment of the magnets on the Sniper is much harder, but practice helps.
- The EL panel helped significantly, and lasted 3 entire days.
- With the reflective eyepiece on the scope and my reflective visor, I couldn't see through it at all. Oh well, at least it was a cool idea and something notable for people to see if they held it.
- Having a second weapon was a kick for kids wanting photos - I often let one kid hold the Sniper, one the DMR and I held the knife. Great times.
- The DMR also needed a new flash suppressor, the cardboard one wasn't cutting it.
- The main 'wow' factor came from the simple action of removing and replacing the magazine and cocking the handle - these simple physical movements on the rifle made it seem all too real.
- Many people commented on how realistic it looked from afar, and how soft it was when they held it.
- An admirer suggested that instead of an orange barrel (which I was just going to paint for Supanova), I could make an orange EVA foam plug for the end that I could insert and remove like a cork - no permanent colouring of the barrel, and a soft pad I can rest the rifle on when upside-down.
- Lastly, the rifle with the barrel removed (at under a meter) could be easily taken for a complete rifle (i.e., it didn't obviously look incomplete) meaning it could be brought into a con with a 1-Meter rule inspection and assembled afterwards pretty easily.
These are some pics from the day:
Test Pics at home before the Con:
Pics at CanCon:
Yay!
Got featured on ABC News too!
Got some professional photos too:
CONCLUSION
The build was commenced on January 2nd 2015, and ready by 11th January 2015 - just over a week of work. Compared to the DMR, which was 2 days, it seemed like an ordeal - but in hindsight it came together pretty quickly! I have some future ideas of what additions to make, but i'll cover those in a future post.
As only my second foam Halo weapon, I learned a lot, but at the same time, it was reasonably straight forward - with this same, or similar, methods, it's a simple way for anyone to make their own replica of a movie/game prop.
Let me know your feedback and comments below, I'll update soon with any further progress or changes!
Last edited by a moderator: