- Member DIN
- S068
So over the course of finishing off a free keg at a local art show conversation steered to the desire for the gallery owner to have a cosplay props and armour showcase at some point in the not so distant future. Long story short I decided that a year and a half of building would give myself and some other local cosplayers ample time to fill up a gallery with displays.
Not all of the props are based on Halo, in fact very few are. I'm doing this more as a way to log my builds and track my growth in the various skills required for making props. Many of the listed props are from popular franchises but are either personal favourites or things I've never seen made into a real world version and I want to change that. All of the schematics and .stl/.obj files for these props will be hosted in a linked Dropbox folder as they are finished because if someone sees something cool and they want to try it, I want them to learn from my mistakes and make something even cooler.
So here we are in March (month three of my challenge) where I've just finished my first Halo prop on the list which is an old favourite of mine, the Type-33 Light Anti-Armour Weapon (Fuel Rod Cannon) from Halo 3. The timing of the build was to match up with a local gaming convention which was hosting a cosplay contest and the Fuel Rod Cannon was to replace the Battle Rifle that had previously been banned from several other events for having too similar a profile to active military service weapons even though it follows prop and replica weapons to a T. So big space gun that looks absolutely ridiculous.
It all started simply enough with waiting around in a Tim Horton's with a sketchbook, my tablet and about three hours to burn. After playing around with NifeGun for a bit to figure out a scale from a Halo 3 Spartan to a 1.75m ODST (out of armour) the pattern was completed in SketchUp and scaled in Inkscape
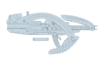
Since the finished gun was scaled to be almost five feet long, two feet tall and six inches thick I needed it to be crafted from as lightweight a material as possible while still being durable. C-200 XPS foam was the champion here coming in at about $17 Canadian for an 8'x2' sheet and I needed roughly two and a half of them. The benefit of this stuff is that it's simple to carve with a knife and sands smooth with very little effort, so I ended up going overkill because this is a large prop and nobody has time to whittle away at 48sqft of foam. A jigsaw to rip out rough shapes from the sheets, a scroll saw to refine shapes, a plunge router to adjust depths of foam at various areas and my favourite toy and MVP in this project a handheld 1.5" belt sander to carve and shape.
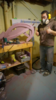
The basic setup was that everything was to be completed in five layers of foam, with the two outermost layers being the sweeping arches and hand guards, the second and fourth layers being detail for the side panels at the depth between the arches and the core, layer three, being primarily structural and having the handle/grip. Between layers 2-3 and 3-4 tracks for electronics were laid to have light shining through control panels and various indicators and ports. In total there was 6 LEDs (3.3V 20mA Super Bright White) inside in pairs with a ~150ohm resistor powered by a 9V battery which is accessible through the Fuel Rod magazine trench and a switch at the grip. Proper wiring is important since a 9V powering so few LEDs will heat the 9V up and possibly melt paint/glue/foam and let some ungodly fumes to the convention hall so do that right, whenever in doubt or if you're just lazy use a circuit solver to make sure you're not going to burn out any electronics. Because of the internal nature of the lights, they're never going to be accessible again once the pieces of the Fuel Rod Cannon Body are glued together, 2mm acrylic sheet painted transparent green was installed in the openings and the track was sealed with acrylic gesso as a layer of protection as well as to hide the pink of the foam when looking into the prop through the acrylic.
Everything was then pieced together with 3M Super77 for a stronger and quicker bond than with PVA wood glue. In a past build (Halo 4 Needler) PVA took about a day to set and that was only the outermost sections that had access to air to assist in drying. When drilling in support rods between the main body and the stock internal sections still had wet glue after 3 days, so I wasn't having any of that. The barrel itself is a 2"OD acrylic tube which is also the size of the fuel rods, which is oddly convenient. Detail was built up with 2mm EVA foam and 10mm EVA floor mats for the rails. A threaded rod was drilled through the barrel and the weird front panel was attached.
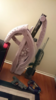
As mentioned, the fuel rods were 2"OD acrylic pipe. The three rods were painted with the same transparent green as the interior windows[?] and the end caps were modelled in SketchUp. Packing foam sheets were used as light diffusers and LED light sticks were placed inside. To turn the rods glow on and off the end caps are pressure fit in place and just need to be slightly twisted to pop free and hit the on switch.
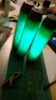
For paint the majority of it was done with the Canadian Tire special of whatever was cheapest at the time. For a primer coat I used three coats of brush on acrylic Gesso (get it at Michaels for $30/gallon or $15 on the weekend with the weekly 50% off coupon) and then a two layers of Krylon ColourMaster flat black primer. The silver was Rustoleum Aluminum finish, the brass was Krylon Hammered Gold and then highlights were finished with a handful of colours from the Valejo Model Air line for airbrushes, I believe I used gunmetal, iridescent silver, shining gold and then a grey. Everything was coated with a satin clear finish and some light weathering was done with acrylic brush on paints and a handy toothbrush.
I think it turned out alright. If I do end up making another one, I'll be using a worbla or other thermoplastic coating layer for the whole thing. I carried it around for a weekend and was constantly trying to be careful not to turn quickly and hit something or have it crushed in transport with everything else. Even with five layers of paint and three of Gesso the surface likes to scratch and dent. The good news is that I came second in the cosplay contest and had a great time over the weekend while meeting a bunch of talented cosplayers. Look at the top 3, they're amazing.
I learned a lot over the course of this build and I'm going to keep on pushing forward. I don't post as frequent updates here as I do on Facebook so if you want to derp around and talk about stupid large builds or weird costuming techniques, hit me up at Skookum Props and Armour.
Sorry about the novel, hopefully the pictures helped ease the pain, I'll have another of these big updates in this thread sometime next month.
Not all of the props are based on Halo, in fact very few are. I'm doing this more as a way to log my builds and track my growth in the various skills required for making props. Many of the listed props are from popular franchises but are either personal favourites or things I've never seen made into a real world version and I want to change that. All of the schematics and .stl/.obj files for these props will be hosted in a linked Dropbox folder as they are finished because if someone sees something cool and they want to try it, I want them to learn from my mistakes and make something even cooler.
So here we are in March (month three of my challenge) where I've just finished my first Halo prop on the list which is an old favourite of mine, the Type-33 Light Anti-Armour Weapon (Fuel Rod Cannon) from Halo 3. The timing of the build was to match up with a local gaming convention which was hosting a cosplay contest and the Fuel Rod Cannon was to replace the Battle Rifle that had previously been banned from several other events for having too similar a profile to active military service weapons even though it follows prop and replica weapons to a T. So big space gun that looks absolutely ridiculous.
It all started simply enough with waiting around in a Tim Horton's with a sketchbook, my tablet and about three hours to burn. After playing around with NifeGun for a bit to figure out a scale from a Halo 3 Spartan to a 1.75m ODST (out of armour) the pattern was completed in SketchUp and scaled in Inkscape
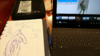
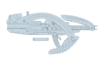
Since the finished gun was scaled to be almost five feet long, two feet tall and six inches thick I needed it to be crafted from as lightweight a material as possible while still being durable. C-200 XPS foam was the champion here coming in at about $17 Canadian for an 8'x2' sheet and I needed roughly two and a half of them. The benefit of this stuff is that it's simple to carve with a knife and sands smooth with very little effort, so I ended up going overkill because this is a large prop and nobody has time to whittle away at 48sqft of foam. A jigsaw to rip out rough shapes from the sheets, a scroll saw to refine shapes, a plunge router to adjust depths of foam at various areas and my favourite toy and MVP in this project a handheld 1.5" belt sander to carve and shape.
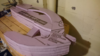
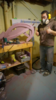
The basic setup was that everything was to be completed in five layers of foam, with the two outermost layers being the sweeping arches and hand guards, the second and fourth layers being detail for the side panels at the depth between the arches and the core, layer three, being primarily structural and having the handle/grip. Between layers 2-3 and 3-4 tracks for electronics were laid to have light shining through control panels and various indicators and ports. In total there was 6 LEDs (3.3V 20mA Super Bright White) inside in pairs with a ~150ohm resistor powered by a 9V battery which is accessible through the Fuel Rod magazine trench and a switch at the grip. Proper wiring is important since a 9V powering so few LEDs will heat the 9V up and possibly melt paint/glue/foam and let some ungodly fumes to the convention hall so do that right, whenever in doubt or if you're just lazy use a circuit solver to make sure you're not going to burn out any electronics. Because of the internal nature of the lights, they're never going to be accessible again once the pieces of the Fuel Rod Cannon Body are glued together, 2mm acrylic sheet painted transparent green was installed in the openings and the track was sealed with acrylic gesso as a layer of protection as well as to hide the pink of the foam when looking into the prop through the acrylic.
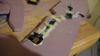
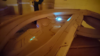
Everything was then pieced together with 3M Super77 for a stronger and quicker bond than with PVA wood glue. In a past build (Halo 4 Needler) PVA took about a day to set and that was only the outermost sections that had access to air to assist in drying. When drilling in support rods between the main body and the stock internal sections still had wet glue after 3 days, so I wasn't having any of that. The barrel itself is a 2"OD acrylic tube which is also the size of the fuel rods, which is oddly convenient. Detail was built up with 2mm EVA foam and 10mm EVA floor mats for the rails. A threaded rod was drilled through the barrel and the weird front panel was attached.
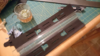
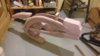
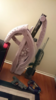
As mentioned, the fuel rods were 2"OD acrylic pipe. The three rods were painted with the same transparent green as the interior windows[?] and the end caps were modelled in SketchUp. Packing foam sheets were used as light diffusers and LED light sticks were placed inside. To turn the rods glow on and off the end caps are pressure fit in place and just need to be slightly twisted to pop free and hit the on switch.
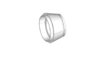
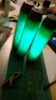
For paint the majority of it was done with the Canadian Tire special of whatever was cheapest at the time. For a primer coat I used three coats of brush on acrylic Gesso (get it at Michaels for $30/gallon or $15 on the weekend with the weekly 50% off coupon) and then a two layers of Krylon ColourMaster flat black primer. The silver was Rustoleum Aluminum finish, the brass was Krylon Hammered Gold and then highlights were finished with a handful of colours from the Valejo Model Air line for airbrushes, I believe I used gunmetal, iridescent silver, shining gold and then a grey. Everything was coated with a satin clear finish and some light weathering was done with acrylic brush on paints and a handy toothbrush.
I think it turned out alright. If I do end up making another one, I'll be using a worbla or other thermoplastic coating layer for the whole thing. I carried it around for a weekend and was constantly trying to be careful not to turn quickly and hit something or have it crushed in transport with everything else. Even with five layers of paint and three of Gesso the surface likes to scratch and dent. The good news is that I came second in the cosplay contest and had a great time over the weekend while meeting a bunch of talented cosplayers. Look at the top 3, they're amazing.
I learned a lot over the course of this build and I'm going to keep on pushing forward. I don't post as frequent updates here as I do on Facebook so if you want to derp around and talk about stupid large builds or weird costuming techniques, hit me up at Skookum Props and Armour.
Sorry about the novel, hopefully the pictures helped ease the pain, I'll have another of these big updates in this thread sometime next month.