This is a continuation of the construction tutorials of files available for Foam Reach armor. The files are in dire need of detailed instructions, so I am going to attempt to do just that. Just like the previous build (forearm), I am going to break this down into several steps.
FIRST AND FOREMOST, due credit must be given. Model by ForgedReclaimer and Foam Unfold by L3x Blu3r1v3r
This bicep file can be found in the 405th 4Shared database in Foam Templates/Reach/Base/Male/Shoulder and is the "Foam Bicep L.PDO" file.
Tools required:
EVA foam - This build utilizes approx. 1 - 2'X2' sheet of EVA Foam for both left and right shoulders
*Scalpel handle with #11 blades (I used just one blade and sharpened it between each piece at a minimum)
Ball point pen
Printed templates. I used the default size of H:180mm W:168mm D:134mm
*Box Cutter blade - I use the small, rectangle, single edge ones (the kind you put in a cheap box-cutter)
*Cutting mat (or other surface to protect your table or whatever is under your foam!)
Hot glue gun
*High temp glue sticks (I ONLY use hot temp and not low or multi-temp ones... they make a difference!)
Heat gun
*Dremel with barrel sander bit (120 grit) and a small cone shaped stone bit (for small detail holes)
* indicates optional or personal preference. I have found that using these items generally yield superior builds if used correctly.
Ok, now for the pep file template.
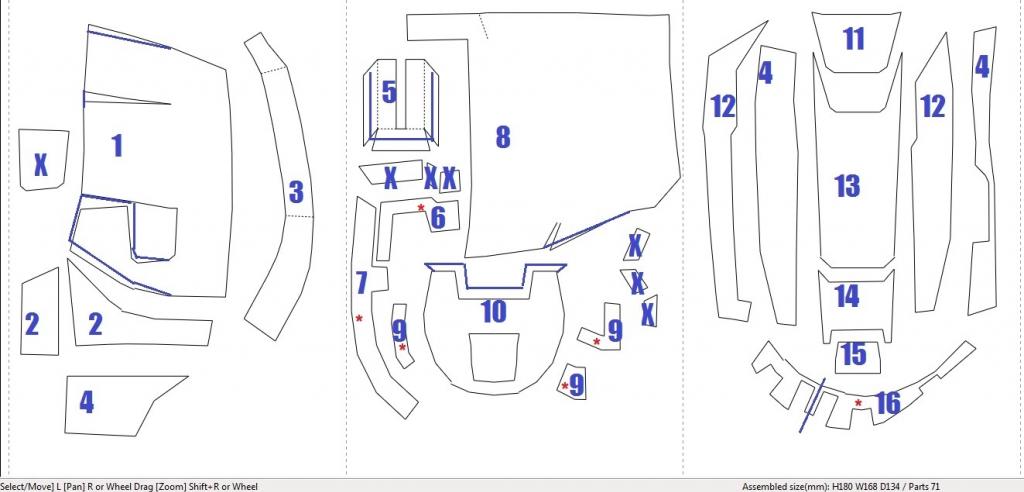
And my cut-outs
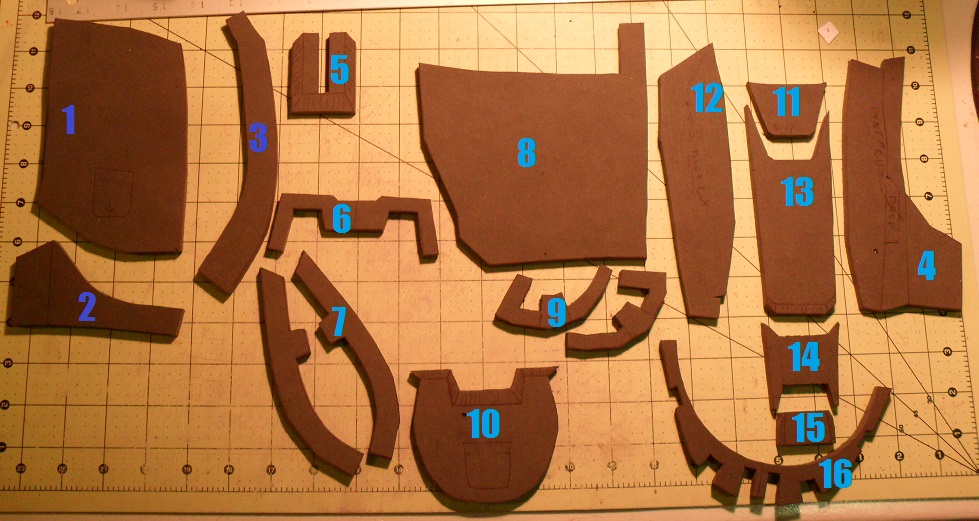
These pictures only show the LEFT SHOULDER, you will need to flip each piece over and duplicate a mirror image for the RIGHT SHOULDER.
KEY
Pieces with a "X" are not used
Duplicate numbers (2, 4, 9, & 12) have been combined with the other corresponding numbers to make a single piece. Keep in mind, when parts are combined, sometimes the template pieces do not line up perfectly. This is okay, and they will "come out in the wash" as the build progresses.
Parts with a red "*" need to be mirrored.
There are plenty of parts that need to be altered, so I suggest making those alterations on your printed cardstock before attempting to transfer to foam.
1. This may look tricky, but try not to overthink it. Since I prefer not to make visible cuts whenever possible, I chose to eliminate these open seams and will rely on the EVA's incredible ability to heat form. Instead, save your altered template after you have transferred it to the foam because we will be using it later. To figure out where these new lines go, all I do is "shift" the same distance that the gap was. In the case with the top alteration, the start of the new line on the right is proportionate in distance from the gap below. The alteration below took a bit more figuring because there was a whole shape to move, but the diagram and end result should be fairly self-explanatory. DO NOT CUT THE INSIDE BOX OUT OF THE EVA. Leave the top line connected. This is because this "box" merely tips down at the bottom and requires a cut on the back-side of the EVA to do this. Now, flip this over and cut in your contour lines like this:

2. This is one of the parts that I have combined with another. Also, with the curved piece, simply round out the curve. Then, after this piece has been cut out in EVA, flip it over and cut out a contour line using one of the two templates as a guide for your line.
3. Simple trace and cut-out. Then, flip it over and cut out contour lines where indicated on the template piece.
4. This is a combination of 3 pieces. On this one, go ahead and cut out the lone piece in the center of the combined pieces (the piece that looks like a small boat on its end). Again, flip this piece over and use your template pieces to draw and cut your contour lines. Since the two longer pieces' intersection is a valley, you only need cut a slit for the contour line as a pose to the traditional "V" cut.
5. This piece is yet another tricky one. In order to eliminate these crazy corner seams, I am going to use the thickness of the EVA to my advantage and simply cut the angles in from the top. The only tricky part is to find out where the new edge is. The blue line I have drawn shows the approximate new line you will need to make. Once this is done, and the outline has been transferred from the template to the EVA, you will need to make cuts in your template to get all interior lines transferred. The pictures below demonstrate the point after the outline has been transferred and the template re-cut for the internal lines to be drawn.

And this is what it should look like after all the lines have been drawn. All the little lines represent that this will be an angled cut, and the squiggly line is the section that gets cut out. (This is where you will add 6mm craft foam later... alternately, you can use an accurately cut piece of EVA to fill this in as well)
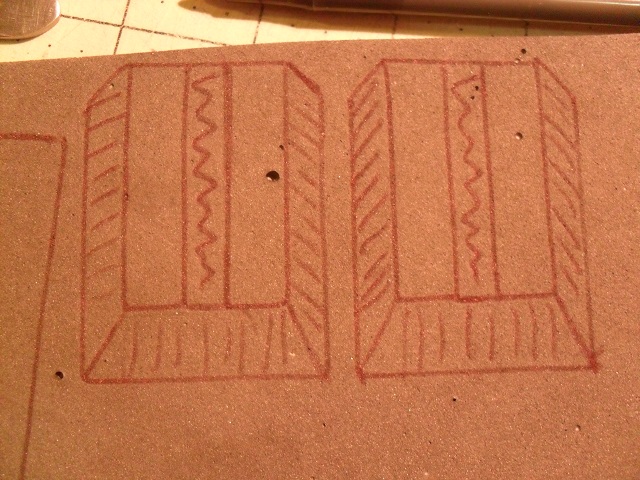
6. A fairly straightforward piece. Mirror this one. Refer to my EVA photo for reference on which side is your base if needed.
7. This also is another straightforward piece. You will need to cut this as a non-joined mirrored piece. Refer to my EVA cut-out photo for reference if needed.
8. Similar to part #1, follow the blue line on the diagram that I drew in, and then flip over to make the contour cuts where shown on the template. (On the template, the "V" shaped cut out is not joined. Simply use a ruler to continue them until they intersect. This will now be your cut for your contour line on the back of the EVA)
9. Another three part combination. Refer to my EVA cut-out photo for assembly reference if needed. Also, this is a non-connected mirror piece as well. Flip and duplicate.
10. This is another tricky part. Since I deleted the tiny angled detail pieces at the top, I need to compensate. The blue lines I drew in the template photo show approximately where the new line will go. After this piece is cut out, the 45 degree outward angle can be cut, thus eliminating those finicky small pieces. Also, the "box" area only gets the sides and bottom cut all the way through. After the piece main piece has been cut out, and the three sides cut through, cut out the box on the template piece and flip the EVA piece over. Using the three sides you cut as reference, draw a line where the top of the box is, and also another line parallel to that about 1/4" down. If you look carefully at the template piece, you can see where the line angles... that is about 1/4" down. Now that those two lines are drawn on the back of your EVA cut out piece, cut a "V" contour line on the top line, and a slit contour line on the lower line. It should look like this when you are done:
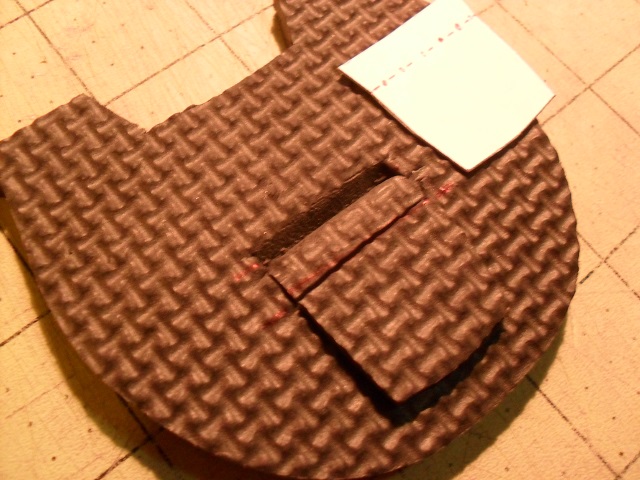
11. Simple cut! YAY!
12. Combine the two pieces to make one. There will be a slight miss-alignment, but that is okay. Also, there will be a small "V" at the bottom; this will need to be cut out. Flip over and use one of the two templates to draw your line for your contour cut. This one too will be a single slit as a pose to the "V" contour cut. Then, using either the 3D model, or the picture below, make the three contour cuts where indicated. The top and bottom will be slits, and the middle a "V" cut.
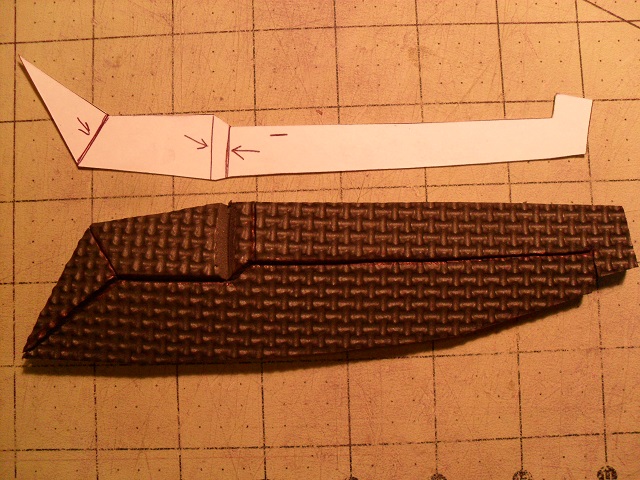
13. Even though it is not shown in the template photo, and a bit hard to make out in the EVA cut out photo, the bottom of this piece has 1/4" added to it for a detail angle that will be cut in later. Other than that, it is a straight forward cut out.
14. Cut this one out just as it is, then follow the examples in the photo below. First, cut the 45 degree angle on the two sides, then cut the "V" contour lines as shown.
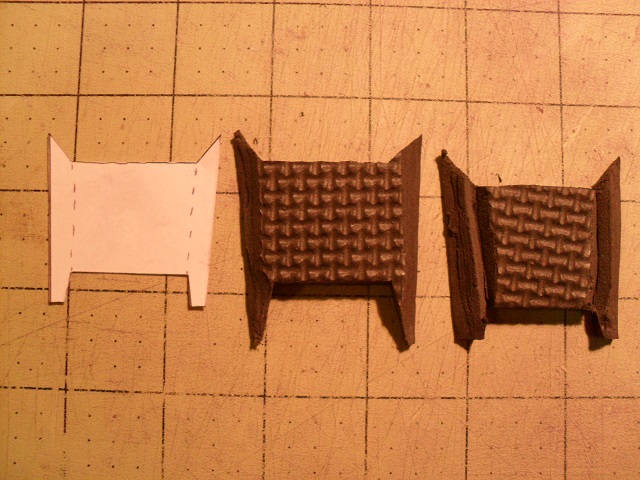
15. Fairly simple on this one too. Not shown in the template and barely visible on the EVA cut-out photo, but I added 1/8" to the sides of this piece to have an angle cut in later.
16. Final piece! Referencing the template photo, this piece will need to be mirrored... BUT, the base of the mirror needs to be where I drew the blue line. The photo below was taken before the pieces were cut out, but show what the template will look like. NOTE: Only one per piece of armor needed. The other one in this photo is for the right bicep.
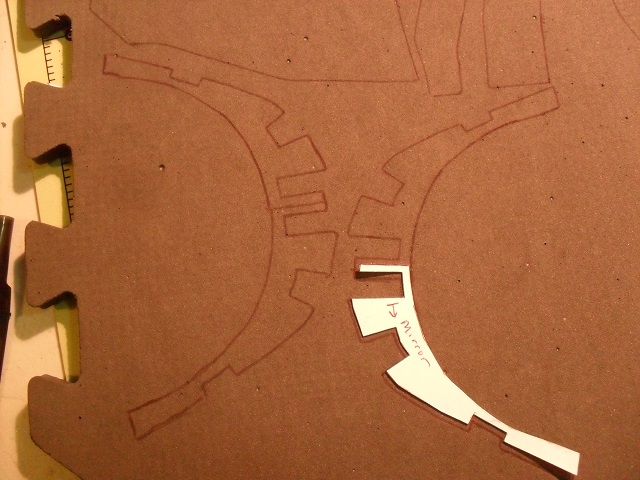
The next update will be heat shaping, cutting angled pieces, and assembling.
FIRST AND FOREMOST, due credit must be given. Model by ForgedReclaimer and Foam Unfold by L3x Blu3r1v3r
This bicep file can be found in the 405th 4Shared database in Foam Templates/Reach/Base/Male/Shoulder and is the "Foam Bicep L.PDO" file.
Tools required:
EVA foam - This build utilizes approx. 1 - 2'X2' sheet of EVA Foam for both left and right shoulders
*Scalpel handle with #11 blades (I used just one blade and sharpened it between each piece at a minimum)
Ball point pen
Printed templates. I used the default size of H:180mm W:168mm D:134mm
*Box Cutter blade - I use the small, rectangle, single edge ones (the kind you put in a cheap box-cutter)
*Cutting mat (or other surface to protect your table or whatever is under your foam!)
Hot glue gun
*High temp glue sticks (I ONLY use hot temp and not low or multi-temp ones... they make a difference!)
Heat gun
*Dremel with barrel sander bit (120 grit) and a small cone shaped stone bit (for small detail holes)
* indicates optional or personal preference. I have found that using these items generally yield superior builds if used correctly.
Ok, now for the pep file template.
And my cut-outs
These pictures only show the LEFT SHOULDER, you will need to flip each piece over and duplicate a mirror image for the RIGHT SHOULDER.
KEY
Pieces with a "X" are not used
Duplicate numbers (2, 4, 9, & 12) have been combined with the other corresponding numbers to make a single piece. Keep in mind, when parts are combined, sometimes the template pieces do not line up perfectly. This is okay, and they will "come out in the wash" as the build progresses.
Parts with a red "*" need to be mirrored.
There are plenty of parts that need to be altered, so I suggest making those alterations on your printed cardstock before attempting to transfer to foam.
1. This may look tricky, but try not to overthink it. Since I prefer not to make visible cuts whenever possible, I chose to eliminate these open seams and will rely on the EVA's incredible ability to heat form. Instead, save your altered template after you have transferred it to the foam because we will be using it later. To figure out where these new lines go, all I do is "shift" the same distance that the gap was. In the case with the top alteration, the start of the new line on the right is proportionate in distance from the gap below. The alteration below took a bit more figuring because there was a whole shape to move, but the diagram and end result should be fairly self-explanatory. DO NOT CUT THE INSIDE BOX OUT OF THE EVA. Leave the top line connected. This is because this "box" merely tips down at the bottom and requires a cut on the back-side of the EVA to do this. Now, flip this over and cut in your contour lines like this:
2. This is one of the parts that I have combined with another. Also, with the curved piece, simply round out the curve. Then, after this piece has been cut out in EVA, flip it over and cut out a contour line using one of the two templates as a guide for your line.
3. Simple trace and cut-out. Then, flip it over and cut out contour lines where indicated on the template piece.
4. This is a combination of 3 pieces. On this one, go ahead and cut out the lone piece in the center of the combined pieces (the piece that looks like a small boat on its end). Again, flip this piece over and use your template pieces to draw and cut your contour lines. Since the two longer pieces' intersection is a valley, you only need cut a slit for the contour line as a pose to the traditional "V" cut.
5. This piece is yet another tricky one. In order to eliminate these crazy corner seams, I am going to use the thickness of the EVA to my advantage and simply cut the angles in from the top. The only tricky part is to find out where the new edge is. The blue line I have drawn shows the approximate new line you will need to make. Once this is done, and the outline has been transferred from the template to the EVA, you will need to make cuts in your template to get all interior lines transferred. The pictures below demonstrate the point after the outline has been transferred and the template re-cut for the internal lines to be drawn.
And this is what it should look like after all the lines have been drawn. All the little lines represent that this will be an angled cut, and the squiggly line is the section that gets cut out. (This is where you will add 6mm craft foam later... alternately, you can use an accurately cut piece of EVA to fill this in as well)
6. A fairly straightforward piece. Mirror this one. Refer to my EVA photo for reference on which side is your base if needed.
7. This also is another straightforward piece. You will need to cut this as a non-joined mirrored piece. Refer to my EVA cut-out photo for reference if needed.
8. Similar to part #1, follow the blue line on the diagram that I drew in, and then flip over to make the contour cuts where shown on the template. (On the template, the "V" shaped cut out is not joined. Simply use a ruler to continue them until they intersect. This will now be your cut for your contour line on the back of the EVA)
9. Another three part combination. Refer to my EVA cut-out photo for assembly reference if needed. Also, this is a non-connected mirror piece as well. Flip and duplicate.
10. This is another tricky part. Since I deleted the tiny angled detail pieces at the top, I need to compensate. The blue lines I drew in the template photo show approximately where the new line will go. After this piece is cut out, the 45 degree outward angle can be cut, thus eliminating those finicky small pieces. Also, the "box" area only gets the sides and bottom cut all the way through. After the piece main piece has been cut out, and the three sides cut through, cut out the box on the template piece and flip the EVA piece over. Using the three sides you cut as reference, draw a line where the top of the box is, and also another line parallel to that about 1/4" down. If you look carefully at the template piece, you can see where the line angles... that is about 1/4" down. Now that those two lines are drawn on the back of your EVA cut out piece, cut a "V" contour line on the top line, and a slit contour line on the lower line. It should look like this when you are done:
11. Simple cut! YAY!
12. Combine the two pieces to make one. There will be a slight miss-alignment, but that is okay. Also, there will be a small "V" at the bottom; this will need to be cut out. Flip over and use one of the two templates to draw your line for your contour cut. This one too will be a single slit as a pose to the "V" contour cut. Then, using either the 3D model, or the picture below, make the three contour cuts where indicated. The top and bottom will be slits, and the middle a "V" cut.
13. Even though it is not shown in the template photo, and a bit hard to make out in the EVA cut out photo, the bottom of this piece has 1/4" added to it for a detail angle that will be cut in later. Other than that, it is a straight forward cut out.
14. Cut this one out just as it is, then follow the examples in the photo below. First, cut the 45 degree angle on the two sides, then cut the "V" contour lines as shown.
15. Fairly simple on this one too. Not shown in the template and barely visible on the EVA cut-out photo, but I added 1/8" to the sides of this piece to have an angle cut in later.
16. Final piece! Referencing the template photo, this piece will need to be mirrored... BUT, the base of the mirror needs to be where I drew the blue line. The photo below was taken before the pieces were cut out, but show what the template will look like. NOTE: Only one per piece of armor needed. The other one in this photo is for the right bicep.
The next update will be heat shaping, cutting angled pieces, and assembling.