SI3RRA 117 Thanks. This leather is about 3-4 times thicker than what I remember mitts being. Mitts have a combo of thin leather and padding. I would estimate years of inconstant use for this this long to brake in. But it was shaped to his body. He finds it quite comfortable. The only thing he doesn't like right now is how hot his face gets from the mask.
Update:
Feeling rather frustrated at the moment. The orbital sander snagged the bow and broke it in two.
Sean Anwalt the extra hardener did help cure the lower layer. I put in about 3x the normal amount.
So instead of calling it quits I thought I would revamp myself by showing you guys more of what I've been up to.
Gloves:
I bought knuckleless gloves online. Cut 15mm squares of leather out. Butchered my belt. Installed the studs to leather and epoxies the leather over the rubber finger vents.
Chest:
I used Evakura's technique on 3d print finishing to clean up these accent pieces then painted with Black automotive Enamel. Epoxied them to leather that had snaps set in already.
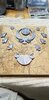
The part that holds the Crest also holds the weight of the cape so I had to make sure it was strong. First I sewed the straps in. These middle four are functional, keeping the center held to the sides.
If I were to then sew the cover on in between these straps then you would see the exposed thread. Instead I had to punch holes and stitch through a spacer. (I'm sure there's a technical name for that.) It can be pretty hard to line up three sets of holes like that.
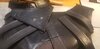
It's very strong now.
Arms:
This took a lot longer than expected.
The plan was to mummy wrap his arms from wrist to armpit. I bought Upholstery fabric because I liked the texture.
I knew if we just cut strips then there would be a high chance they'd fray and unravel. So I opted to make them twice as wide and fold the over. Essentially making a tube. Little did I know this is no easy task for a novice sew-er person. And we needed 50 feet!
First we cut at a diagonal. Apparently most cloth only has give in one direction like grain in wood. So cutting diagonally gives us the most versatility in our goal to wrap it around an arm and it will naturally want to curve up the arm.
Then we used a Serger because we had one. Basically it's a single use sew machine that puts thread everywhere! And cuts the fabric as you go!
The next part is a nightmare without this tool called a Fast Turner. To get the seam on the inside of the tube we have to turn the fabric. Using this metal tube and a wire with a hook on it the process takes about 20 seconds instead of 5 minutes doing it by hand.
Then I had to roll the seam in my finger as I ironed the tube flat before we could sew the tubes together.
We decided an angled seam between links would look better visually than a 90 degree one.
Now we're left with these humps of a seem. To get the flattest look possible we snipped the center of them so each side could be ironed a different direction.
Hand stitching using a curved needle we tacked the bands in a few places. We didnt want to fully sew in case the wrap was too tight or too loose for his arms.
Helm:
This is one of the only pieces I free handed the template and also contains a lot of detail so I thought I would show the process.
Using screenshots from game and math to scale up I came up with this template:
Sketched a design, transferred to leather, cut lines and hammered:
Let dry two days on a WW2 helmet insert for the proper shape.
I set snaps into folded canvas then hidden stitched that to three points on helm. Those keep the helm in place on the hood. But I still had the problem of the points getting bent out. So I took apart a bra to use the wire then epoxied it to the points. Now the wire fits through holes on the hood preventing the points from moving.
Mask:
I don't have many pictures here, but I'll tell you what I did. Similar template process to tooled as the helm.
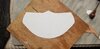
But the shaping was a little trickier since the chin needed to be folded two ways. Long story short, I used the ball on the back of a dining chair that was the perfect curve and just kept pressing it along the chin line.
It worked, but the sides kept spreading out like wings so I cut a V shape on the underside of his chin. This worked and once dried I awled holes along the V and sewed it together.
I sent snaps in it and the ski mask and I put a grommet in so that he could hang the mask on his body when not being worn.
Cape:
There was no preparing me for how hard this was going to be. My mom and I worked together for 7 hours and made 3 1/2 capes.
We found a real wool poncho at goodwill for $4. I bought a table cloth as well for $2
First we cut the table cloth the same shape/size as the wool poncho so we know what we're working with. We brainstormed shapes and proportions for the hood and cape. I first decided to cut away the front of the cape. This way he didn't have to worry about the cape falling forward covering up the armor.
Then we tried to determine the shape of the hood which was really hard. We made Ken doll sized mocks ups to see what they looked like once sewn.
After many revisions we had something to work with.
The result of that weekend was worth it.
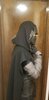