- Member DIN
- S068
Last time we talked about the helmet it was a fancy solid chunk of 3D model waiting to be turned into a wearable bucket. My usual order of operations for this is to make two supplementary shapes, a visor cutout and a neck cutout, take them all into Blender and do some magic BECAUSE MESHMIXER DIDN'T FEEL LIKE COOPERATING.
In Blender I first import the main body of the helmet and under Modifiers I select the helmet and Solidify to create an interior hollow of the helmet to the desired thickness. For a correctly scaled 3D print I'll usually go for a 5mm thickness to allow for two outer walls of 1.2mm (three perimeters) and small section of infill to help keep weight down. With this hollowed out helmet I then import the two cutout shapes and selecting the now hollow helmet form and one of the cutouts under Modifiers again I use Boolean > Difference to make a pair of openings in the helmet.
The new Blender 2.8 Beta is really nice and I highly recommend giving it a try. The UI is greatly improved and there's definitely a bit more processing power to do some of the more complex tasks. Unfortunately my models were a bit to high poly or there was some sharp angles and intersections that threw Blender for a loop and made a bunch of weird internal faces. Normally I'd be perfectly fine with that as long as everything was printable because I'd just run it through Azure 3D Printing Tools to quick fix the mesh and get something that works. For this model though I wanted to make it available to everyone on the forums for free so I had to go in and clean up the mesh to guarantee the .stl file works for every slicer without issue. SketchUp is a hero here and using the Solid Inspector extension any internal faces or holes in the mesh are easily identified and quick* to remove.
Printing was rather painless with two printers chugging away. I had done all the slicing and hollowing after scaling the model on my Armorsmith avatar so I already had a pretty good idea that everything would fit. I also got to do my best Viper 466 impression with a cheapo version of his 'Ronto Trooper as well as test the shoulders for collisions.
It's very close fitting which is good for the slim anime stylings but not so great for the impending sense of claustrophobia this helmet will likely impart if the air gets stale and it gets warm. Luckily the cheeks and the ridge allow for plenty of space to tuck fans into. I haven't checked to see if I can tuck my microphone into the chin yet but I'm thinking it may be a bit awkward in the space.
Everything was glued together using Devcon 5 Minute Epoxy and clamped together working from top front, top back, bottom back, chin to allow clamping surfaces to be accessible through the whole process. Welcome to the family little guy!
*I still spent about 6-8 hours cleaning up the helmet so quick is relative.
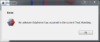
In Blender I first import the main body of the helmet and under Modifiers I select the helmet and Solidify to create an interior hollow of the helmet to the desired thickness. For a correctly scaled 3D print I'll usually go for a 5mm thickness to allow for two outer walls of 1.2mm (three perimeters) and small section of infill to help keep weight down. With this hollowed out helmet I then import the two cutout shapes and selecting the now hollow helmet form and one of the cutouts under Modifiers again I use Boolean > Difference to make a pair of openings in the helmet.
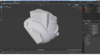
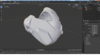
The new Blender 2.8 Beta is really nice and I highly recommend giving it a try. The UI is greatly improved and there's definitely a bit more processing power to do some of the more complex tasks. Unfortunately my models were a bit to high poly or there was some sharp angles and intersections that threw Blender for a loop and made a bunch of weird internal faces. Normally I'd be perfectly fine with that as long as everything was printable because I'd just run it through Azure 3D Printing Tools to quick fix the mesh and get something that works. For this model though I wanted to make it available to everyone on the forums for free so I had to go in and clean up the mesh to guarantee the .stl file works for every slicer without issue. SketchUp is a hero here and using the Solid Inspector extension any internal faces or holes in the mesh are easily identified and quick* to remove.
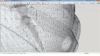
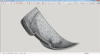
Printing was rather painless with two printers chugging away. I had done all the slicing and hollowing after scaling the model on my Armorsmith avatar so I already had a pretty good idea that everything would fit. I also got to do my best Viper 466 impression with a cheapo version of his 'Ronto Trooper as well as test the shoulders for collisions.
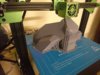
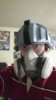
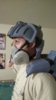
It's very close fitting which is good for the slim anime stylings but not so great for the impending sense of claustrophobia this helmet will likely impart if the air gets stale and it gets warm. Luckily the cheeks and the ridge allow for plenty of space to tuck fans into. I haven't checked to see if I can tuck my microphone into the chin yet but I'm thinking it may be a bit awkward in the space.
Everything was glued together using Devcon 5 Minute Epoxy and clamped together working from top front, top back, bottom back, chin to allow clamping surfaces to be accessible through the whole process. Welcome to the family little guy!
*I still spent about 6-8 hours cleaning up the helmet so quick is relative.