Re: Duke's Halo 4 Venator Pep Build *WIP (1st suit Step-by-Step) +photos!
Finally the bondo is done! I have to say that using a sanding tool is much faster than doing it by hand. :rolleyes Some have mentioned using a mouse sander, but I went with an oscillating tool from the pawn shop. It was $10 more than a mouse sander, but it has way more uses. One down side is that it is pretty heavy.
Photo Update:
Applied the first coat of body filler:
Using the very handy technique of razoring off the clumps when it hasn't fully hardened yet:
Fully covered in the first coat. Even though I did the whole thing, I only did sections using a golf ball of bondo at a time and cleaning it up as it dried.
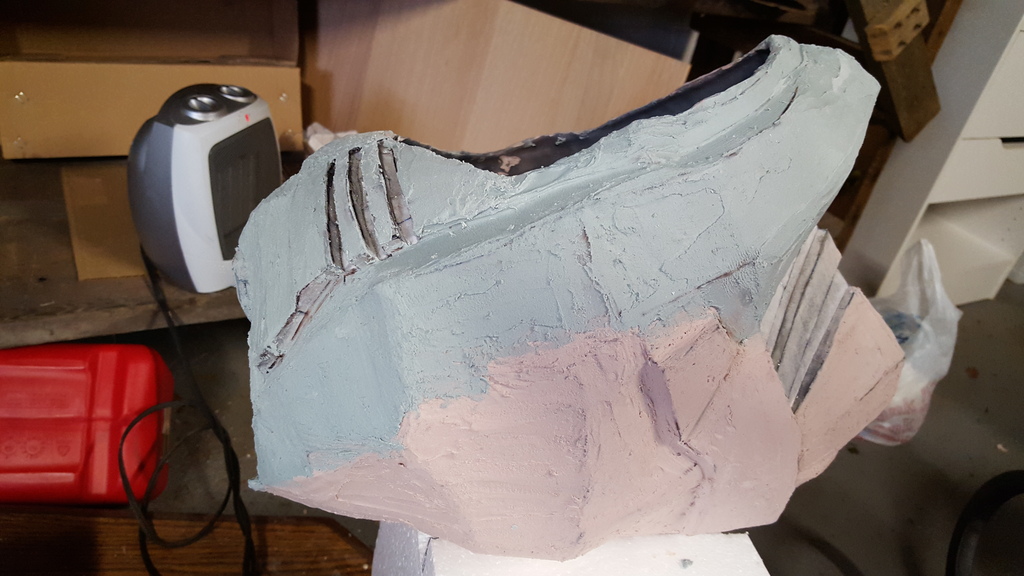
The reason for the red and blue is just because I used up the last of my bondo brand body filler before opening up my generic brand.
This is midway through the second coat. After sanding down the first coat, you can see in the light pink part up front that there are some darker patches. Those are pits in the first coat that I am filling in by applying a second coat.
Tons of sanding later!!!!!
I'm pretty pleased with it. My next step will be to cut out everything that needs to be cut out (visor, light holes, AI slot) then painting, then install all of the cool stuff. Good night to all and happy building!
*I don't claim to be an expert on this. Be sure to watch
Cereal Kill3rs' youtube videos. Below is my summarization of his work, including what I've learned.*
Tips on Shaping with Bondo (Body Filer):
- Don't get confused by the name.. Bondo is a brand. They are known for their body filler, which people just refer to as bondo.
- Get a plan. My project features curves and hard angles, so I don't want to smooth everything. I marked lines I want to stay defined.
- Don't get impatient, this will take a while with multiple coats.. there is no workaround.
Prepping the piece:
1. Using a Dremel or file (or sander), knock down anything that might poke or cut you while handling the piece (like the fiberglass edges).
2. Use markers to make notations to yourself on the piece. Which lines you need to keep defined, where you need to build up more.
3. Get a coarse file and file down every glue seem that is sticking up (mountain folds and pretty much every one). This will reduce the amount of bondo you need.
4. If you break through the paper with the file, get some super glue (Krazy Glue) and let all the paper fibers soak up glue. They can now be sanded without the risk of the fibers poking through your bondo or paint.
First Coat:
1. Always work in small batches, about as much bondo as would fill up a golf ball. Be sure to mix in about an inch line of hardener cream.
2. Use a putty spreader to press in the bondo. (I bought cheap 4" ones and cut them in half to save money).
3. Press it on and spread it around evenly and
very thin.
4. Don't get too hung up on it being even. You only have about 10 minutes to work and you'll want to use up all the bondo before that point, so move on and come back later.
5. Stay working in a small section. Once you run out of body filler, check the areas you just did and even them out with the spreader.
6. It should be getting difficult to evenly move the bondo now.
Grab a paper towel and wipe up any bondo on the piece that shouldn't be there (ie, drips, over spreading).
7. After about 3-5 more minutes the bondo should still be a little soft, not quite rock hard yet. This is a great time to clean up what you've spread around.
Grab a razor blade, or any any thin knife and cut down any high points, clean up edges, anything that will save you from sanding too much.
8. From here you can move on to another section with another golf ball size, or try to finish the one section. Just depends on how you like to work. (I like to do all of the first coat in one sitting)
Second Coat:
1. Bust out a sanding tool or those meat mitts you've got and start smoothing down the first coat. I'd recommend anything from 40 grit to 80 grit.
2. Once you've got it pretty good, you'll see pits that don't have enough bondo. Don't get carried away trying to sand at them, that is what the second coat is for.
3. Using the putty spreader again and still working in golf ball sized clumps of bondo, apply a second layer thinly, making sure to fill in the pits.
4. You'll find it's a lot easier applying the second coat. Take this time to apply more bondo to areas that need to be built up. Still follow the same techniques as used in the first coat.
5. Once done with the second coat, it's time for sanding again. I'd start with a minimum of 60 grit.
6. Determine if you're going to need a third coat (are there any pits you don't like, still areas that need to be built up?)
7. If not, keep sanding, working your way to finer grits. 60 grit, then 80 grit, then 120 grit, then 180 followed by 220 grit. You can skip some of the grits, but you risk leaving scratch marks. You should be able to end on 220 or follow that up with a 320 grit for a super smooth finish. Any higher grits are not necessary.
8. After many hours of hand sanding, or many minutes of machine sanding, you're piece should be done.
9. You can fill in any little pits or smoothing left with bondo brand Spot Putty, applied with you fingers.
Note: It is a fine investment to buy a sanding machine. There are some options. An
orbital sander is large and very practice if you have other wood-working-type projects to use it on. A
mouse sander is cute. Basically, it's a tiny orbital sander that has a point to get into tight places. The uses afterwards are rather limited.
I chose to buy an osculating tool with a sanding attachment. Buying it used costs only a little more than a mouse sander and the functionality for other uses is vast. I found the shape of the sanding attachment to be perfect for both large and tight spaces. The downside is that it is heavy. I had to switch between my left and right hand every minute or two.