Weapon/Anti-Vehicle Model 6 Grindell/Galilean Nonlinear Rifle "Spartan Laser"
Halo Reach Variant
Construction
No matter what, this was going to be a big model with need for extra structural support and as much weight reduction as possible to save time in printing, cost of material and ultimately the shoulders of the poor bastard (me) who has to carry this thing. With that in mind the design process focused on blocking out the main body shape of the laser and then shelling them before the level of complexity increased beyond the point that Fusion360 can handle.
The overall form of the laser body changed slightly between concept art and the in game version. The concept art was a little more streamlined and less "tall". I have a feeling that it was intended to be even longer than it ended up as in it's final form and was adjusted to what we know and love.
From the references and in game files it showed that the laser is almost mirror symmetric along it's body except for a few additional warning labels on the right side and extra controls on the left side. This made modelling simple since one half could be completed, mirrored and then extras added onto the base form.
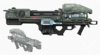
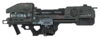
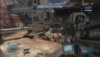
To further reduce demands of printing, materials already available were integrated into the design to add structure without having to strain the print robots. 5mm steel rods, 2" OD ABS and 20mm aluminum square tubing were used for support rods, the barrel base and the upper shroud housing support respectively.
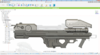
The upper housing of the main body is removable to store a battery pack and the absolute mass of wires needed to toss the 18 LEDs into the removable panel and the 9 LEDs throughout the rest of the body. The foregrip rotates to lock into two different positions. The model allows for the upper shroud to close but for stability and strength of a clumsy operator (me) it's locked in place currently. Please enjoy some renders of the big goofy space laser model.
All said and done the main body of the laser was 39 separate files for printing excluding 32 hex-bolt and other fasteners modeled to be added on after painting to reduce amount of masking required in the paint step. Each main body section roughly was 36-48 hours of print time and the entire model consumed 4kg of filament plus or minus some tail ends of spools.
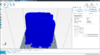
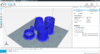
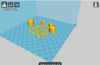
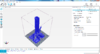
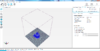
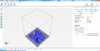
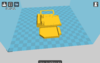
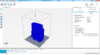
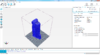
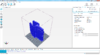
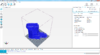
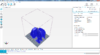
To supplement the painting I designed some stencils and stickers of warning labels and indicators that appear on the body of the prop. I haven't added them at the time of writing this due to vinyl supply I had on hand being a butt and not cutting properly but soon enough I'll have some glamour shots with the full meal deal.
Printing out these beastly parts was fun watching the real scale of the prop become apparent. When you know the dimensions but don't really think about how big it actually is all together it makes for a giddy maker. I can be quoted as giggling and laying out parts on the floor and chanting "BIG CHUNGUS".
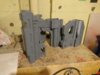
Assembling everything made the weight of it apparent with the extra steel and aluminum supports. This is something that sticks near a booth when in SPARTAN gear or is a team effort with a handler since hefting it for long periods of time will get tiring real quick. Sanding and body work was done over the course of four very late nights and then it was coated with two to three rounds of filler primer depending on the area.
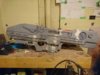
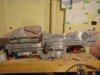
Electronics install for certain parts such as the barrel needed to be done post-paint and pre-final assembly so that they could be reached and properly soldered together in a reasonable fashion without having to feed wires through with fishing line. It was interesting to say the least. The whole prop is powered by a standard USB power bank so it's as easy as plugging your Splazer into the wall to recharge. All said and done there are 27 LEDs that are between 2.1V and 3.4V so resistor values are varied depending on location.
- 2 firing indicator 5mm Red LEDS
- 3 laser emitter 5mm Red LEDS
- 2 forward housing 5mm Red LEDS
- 2 shroud raised indication 5mm Blue LEDS
- 2 triangular indicator 5mm Red LEDS
- 16 emitter housing 5mm LEDS (Red, Orange, Amber, Yellow, Warm White)
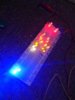
And the mandatory "I made a thing" picture at the 98% assembled stage. Tiny Charizard included in image so I can still be identified.
Materials Used
eSun PLA+ Gray - 4kg
5mm stainless steel rod - 3m
20mm aluminum square pipe - 10cm
2" OD ABS pipe - 60cm
Devcon 5 Minute Epoxy
BSI InstaCure+
BSI InstaSet
Bondo Body Filler
Bondo Glazing Putty
Rustoleum Filler Primer Gray
Duplicolor Filler Primer Red
Rustoleum 2X Black Primer
Vallejo 74.612 NATO Green Surface Primer
Vallejo Metal Colour 77.720 Gunmetal Gray
Vallejo Metal Colour 77.712 Steel
Vallejo Metal Colour 77.701 Aluminum
20 AWG Solid Core Wire
Perfboard
Resistors (+/-5% set) various
USB cable
LEDs various
Caffeine - lots
Alchohol - various